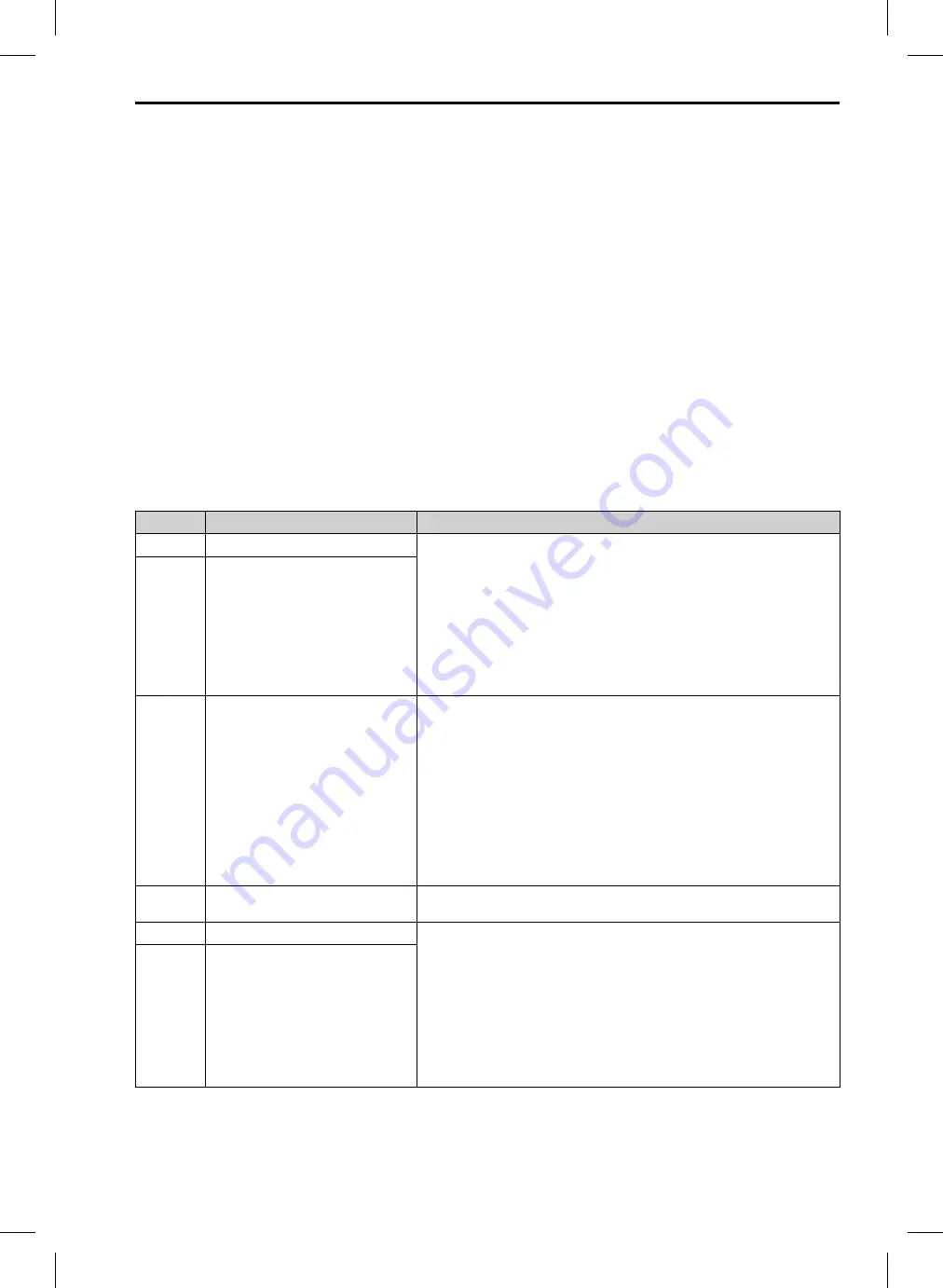
3 Startup Procedure and Test Run
YASKAWA ELECTRIC
SIEP C710617 19A YASKAWA AC Drive CR700 Technical Manual
171
Input Signal Setup
Multi-Funciton Digital Inputs (Terminals S1 to S10)
Use the
H1 Parameters
to set functions to the MFDI terminals (S1 to S10). For more information about MFDI
functions, refer to
H1-xx: MFDI Function Selections on page 458
.
Multi-Function Digital Outputs
Use the
H2 Parameters
to set functions to the MFDO terminals (M1-M6, MA, MB, MC, P1-C1, P2-C2). Refer to
H2-xx: MFDO Function Selections on page 464
for more information about MFDO functions.
Multi-Function Analog Inputs
Use the
H3 Parameters
to set functions to the MFAI terminals (A1, A2, A3). Refer to
for more information about MFAI functions.
Multi-Function Analog Outputs
Use the
H4 Parameters
to set functions to the MFAO terminals (FM, AM). When you enter the
“
x-xx
”
part of the
monitor
Ux-xx
, you can set the MFAO functions. Refer to
for more information about
the monitors.
■
Brake Sequence
To ensure the appropriate amount of torque for the load at start and stop when opening and closing the brake, the
Brake release command is output based on the drive internal frequency reference, the motor current, and the
torque reference.
Related Parameters
Table 3.13 Parameters for the Brake Sequence
No.
Name
Adjustment Method
S1-01
Brake Release Frequency(FWD)
Set a value that is lower than
S1-03
, but higher than
b2-01 [DC Injection/Zero
SpeedThreshold]
and
E1-09 [Minimum Output Frequency]
.
•
Closed Loop Vector Control
Usually, used at 0 Hz.
If slipping occurs when starting to hoist the load in a crane that does not use a
counterweight, then set a high value in
S1-09
.
•
Open Loop Vector Control Method
Set a value that is 1.0 to 1.5 times the motor rated slip.
•
V/f Control Mode
Because it is difficult to ensure enough torque in V/f Control, set a value that is
1.5 to 2.0 times the motor rated slip.
S1-02
Brake Release Frequency(REV)
S1-03
Brake Delay Frequency
Set a value that is equal to
S1-01
and
S1-02
, or a value that is higher than
S1-01
and
S1-02
.
•
Closed Loop Vector Control
Usually, used at 0 Hz.
However, if the 1-notch reference is 1 Hz or less, then
SE2 [Brake Sequence
Fault 2 (SE2)]
may occur due to the lack of current flowing through the motor
at start. In such cases, decrease the setting as low as 0.5 Hz.
•
OLV Control, V/f Control
Set with the target value as the motor rated slip plus 1 Hz.
Note:
If the setting value is too high, shock will likely occur during startup. If the
setting value is too low, then
SE2 [Brake Sequence Fault 2 (SE2)]
may occur
due to the lack of current flowing through the motor at start.
S1-04
Brake Delay Time
Sets a delay time from when the Brake release command is issued until the brake
is actually released.
S1-05
Brake Release Current (FWD)
•
CLV Control, OLV Control
Set
E2-03 [Motor No-Load Current]
× 100 /
E2-01 [Motor Rated Current]
.
•
V/f Control Mode
For hoisting, set
S1-05 = 100%, S1-06 = 50%
. For traveling, set 50%.
Note:
•
If the load differs when operating forwards and in reverse, then change the
setting appropriately to match the load.
•
If the setting value is too low for hoisting the load, then load slips will likely
occur at start.
•
If the setting value is too high, then
SE2 [Brake Sequence Fault 2 (SE2)]
may
occur, and the brake may slip just before it is released.
S1-06
Brake Release Current (REV)