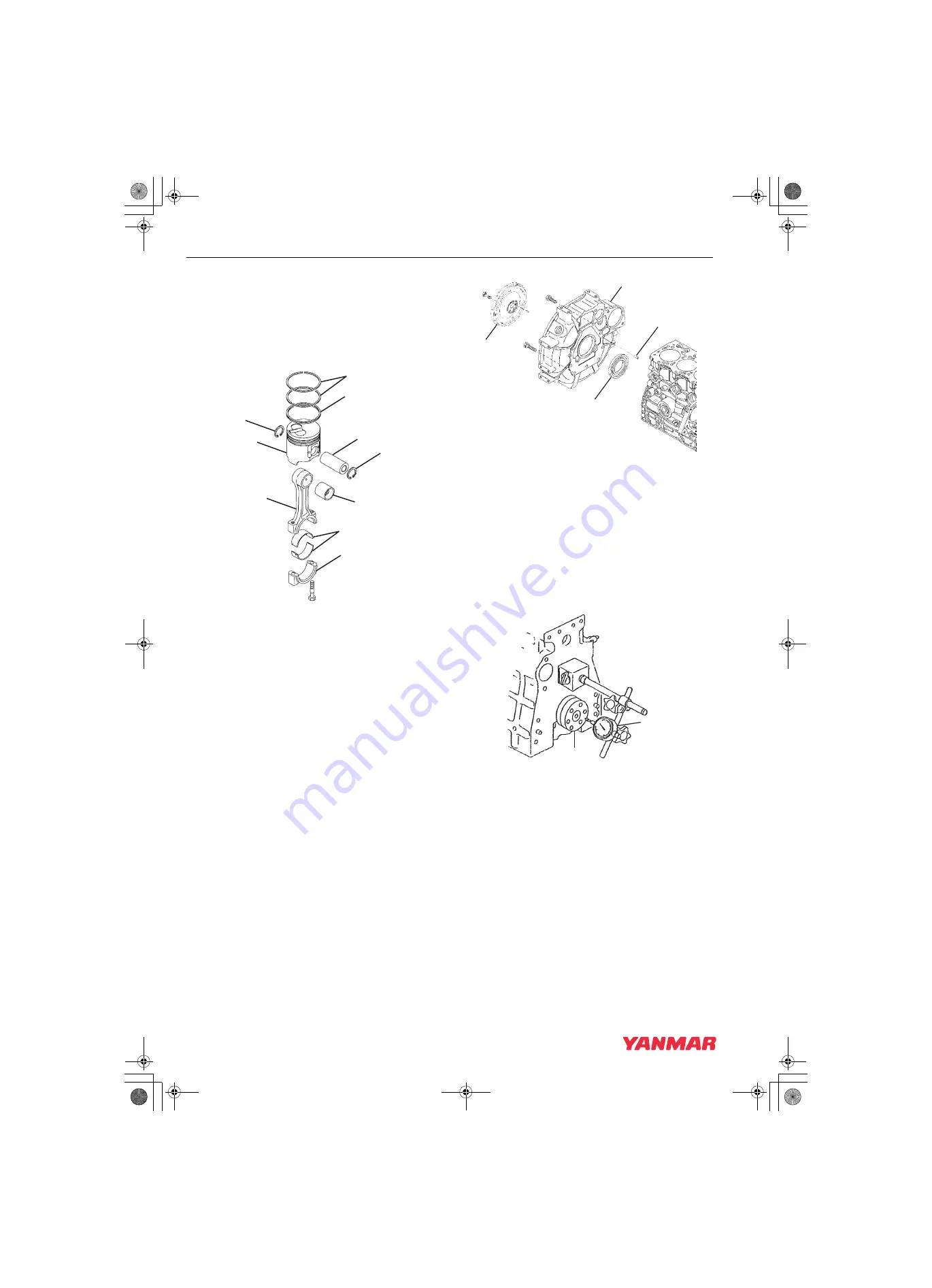
ENGINE
6-42
TNV IDI Service Manual
Cylinder Block
11. Remove the bearing inserts
(Figure 6-53, (2))
.
12. Remove the compression rings
(Figure 6-53, (3))
from the piston using a piston
ring expander.
13. Remove the oil ring
(Figure 6-53, (4))
from the
piston using a piston ring expander.
Figure 6-53
14. Remove the circlips
(Figure 6-53, (5))
from the
wrist pin.
15. Remove the wrist pin
(Figure 6-53, (6))
and
connecting rod
(Figure 6-53, (8))
from the
piston
(Figure 6-53, (9))
.
16. Repeat steps until all pistons are removed and
dissembled.
Removal of Crankshaft
1. Remove the flywheel
(Figure 6-54, (1))
from
the crankshaft.
2. Remove the bolts
(Figure 6-54, (2))
from the
flywheel housing assembly. Remove the
flywheel housing from the engine.
Figure 6-54
3. Before removing the main bearing caps,
measure the crankshaft end play. Use either of
the following two methods:
•
Method A:
Install a dial gauge
(Figure 6-55, (1))
on the cylinder block. Move
the crankshaft
(Figure 6-55, (2))
in and out to
measure the end play. Record the
measurement.
Figure 6-55
0001705A
(3)
(4)
(6)
(7)
(5)
(2)
(1)
(8)
(9)
(5)
00021
88
(3)
(2)
(1)
(4)
(1)
(2)
0001961
TNV_IDI_ServiceManual_A4.book 42 ページ 2012年2月24日 金曜日 午前10時24分