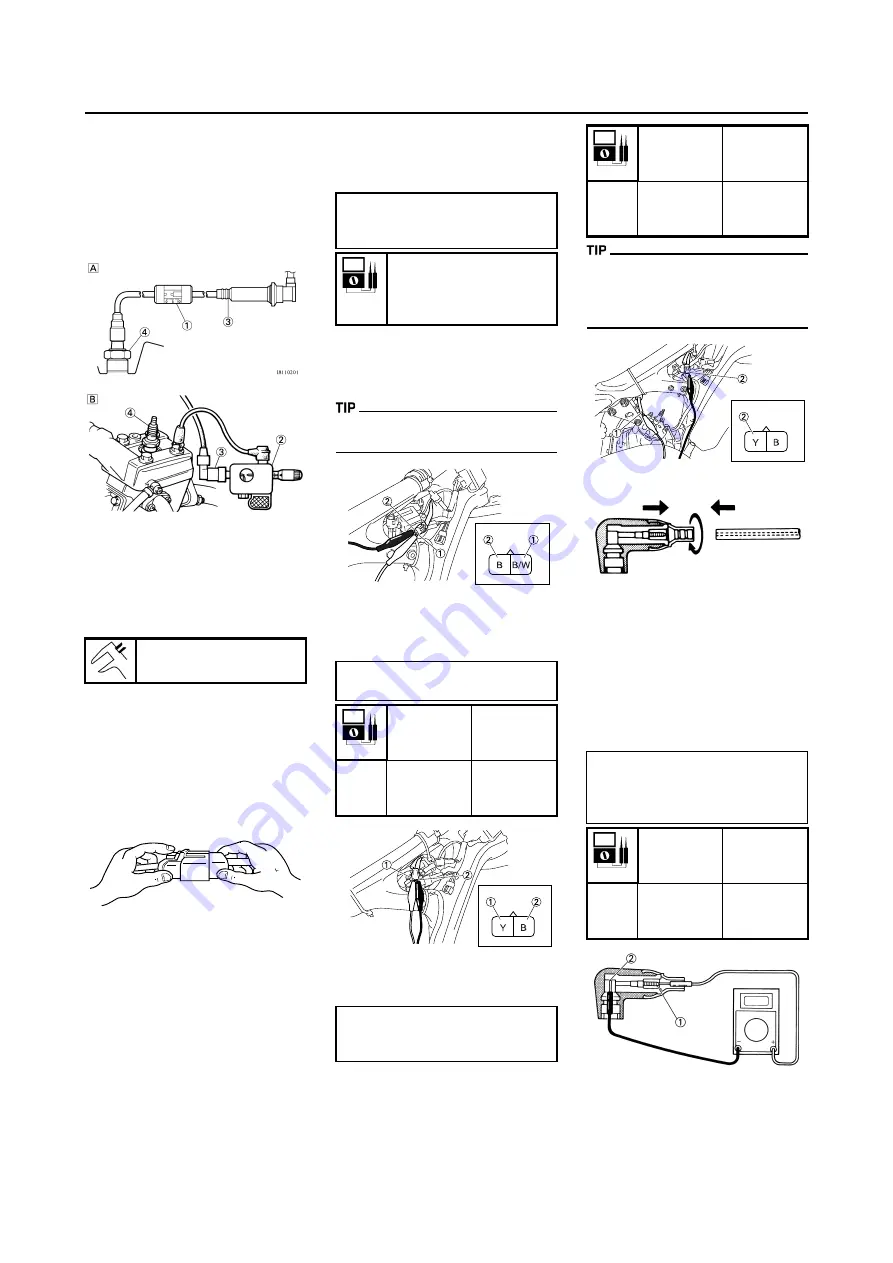
6-4
IGNITION SYSTEM
SPARK GAP TEST
1. Disconnect the spark plug cap
from spark plug.
2. Connect the dynamic spark tester
"1" (ignition checker "2") as
shown.
• Ignition coil "3"
• Spark plug "4"
A. For USA and CDN
B. Except for USA and CDN
3. Kick the kickstarter crank.
4. Check the ignition spark gap.
5. Start engine, and increase spark
gap until misfire occurs. (for USA
and CDN only)
CHECKING THE COUPLERS,
LEADS AND IGNITION COIL
CONNECTION
1. Check:
• Couplers and leads connection
Rust/dust/looseness/short-cir-
cuit
→
Repair or replace.
CHECKING THE ENGINE STOP
SWITCH
1. Inspect:
• Engine stop switch conduction
Not conductive while it is pushed
→
Replace.
Conductive while it is freed
→
Re-
place.
Set the tester selection position to "
Ω
× 1".
CHECKING THE IGNITION COIL
1. Inspect:
• Primary coil resistance
Out of specification
→
Replace.
2. Inspect:
• Secondary coil resistance
Out of specification
→
Replace.
• Remove the spark plug cap by turn-
ing it counterclockwise and inspect.
• Install the spark plug cap by turning
it clockwise until it is tight.
CHECKING THE SPARK PLUG
CAP
1. Inspect:
• Spark plug cap
Loose connection
→
Tighten.
Deteriorated/damaged
→
Re-
place.
• Spark plug cap resistance
Out of specification
→
Replace.
Minimum spark gap:
6.0 mm (0.24 in)
Tester (+) lead
→
Black/White lead
"1"
Tester (-) lead
→
Black lead "2"
Result
Conductive (while the
engine stop switch is
pushed)
Tester (+) lead
→
Yellow lead "1"
Tester (-) lead
→
Black lead "2"
Primary
coil resis-
tance
Tester se-
lector posi-
tion
0.24–0.36
Ω
at 20 °C
(68 °F)
Ω
× 1
Tester (+) lead
→
Spark plug lead
"1"
Tester (-) lead
→
Yellow lead "2"
Secondary
coil resis-
tance
Tester se-
lector posi-
tion
5.7–8.5
k
Ω
at 20 °C
(68 °F)
k
Ω
× 1
Tester (+) lead
→
Spark plug lead
terminal "1"
Tester (-) lead
→
Spark plug termi-
nal "2"
Spark plug
cap resis-
tance
Tester se-
lector posi-
tion
4–6 k
Ω
at
20 °C (68
°F)
k
Ω
× 1
Содержание YZ125(D)
Страница 4: ......
Страница 12: ...1 2 LOCATION OF IMPORTANT LABELS ...
Страница 13: ...1 3 LOCATION OF IMPORTANT LABELS EUROPE AUS NZ ZA ...
Страница 37: ......
Страница 138: ...5 30 STEERING 9 Bearing race 2 Refer to removal section Order Part name Q ty Remarks ...
Страница 167: ......
Страница 168: ...PRINTED IN JAPAN E PRINTED ON RECYCLED PAPER ...