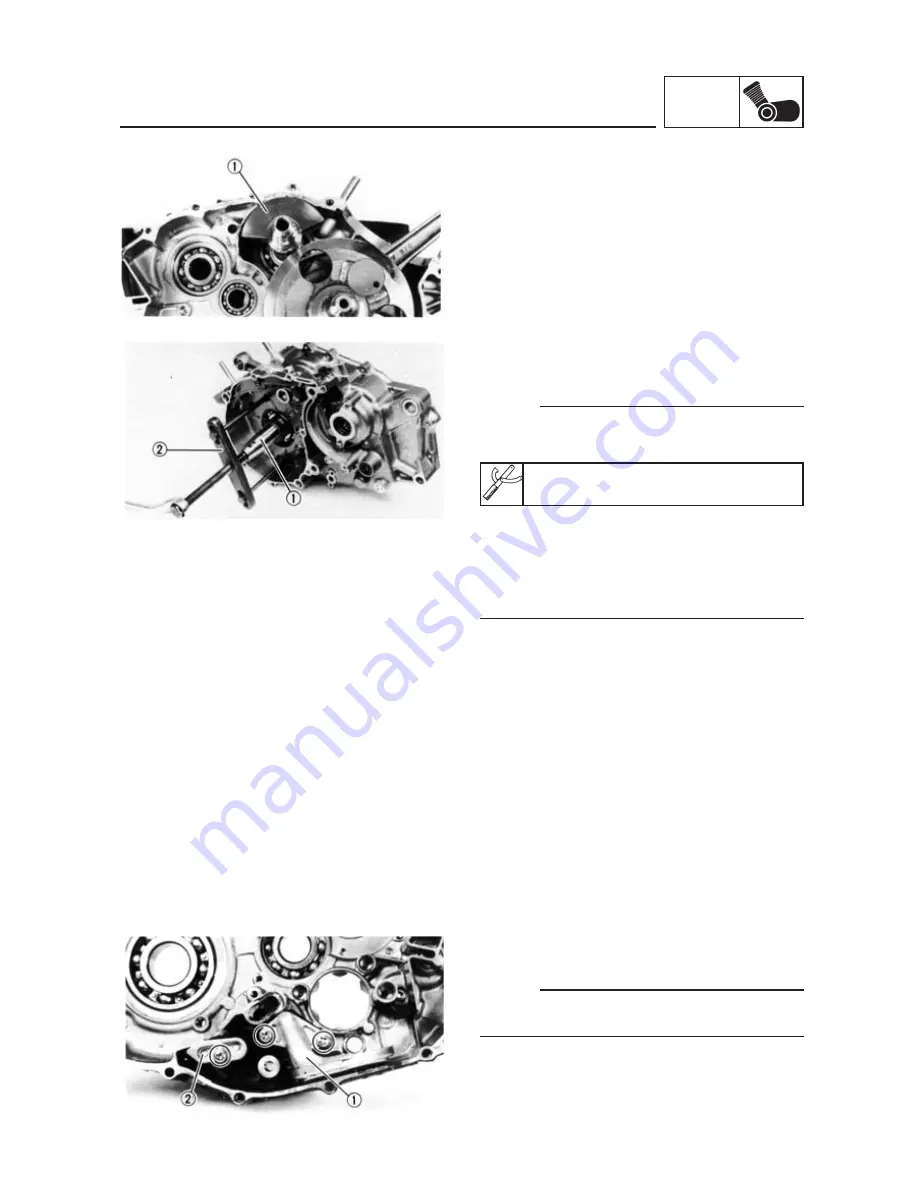
ENG
ENGINE DISASSEMBLY
5-17
BALANCER SHAFT AND CRANKSHAFT
1. Remove:
•
Balancer shaft (1)
2. Remove:
•
Crankshaft (1)
NOTE:
•
Remove the crankshaft by using the
crankcase separating tool (2).
Crankcase separating tool:
P/N. 90890-01135
•
Tighten the separating tool bolts, making sure
that the tool body is parallel with the engine
crankcase. If necessary, a screw may be
backed out slightly to level tool body.
OIL STRAINER
NOTE:
It is advisable to replace the oil strainer every time
the engine is disassembled.
1. Remove:
•
Oil strainer (1)
•
Oil passage cover (2)
•
Gasket
Содержание TT600R
Страница 1: ...YAMAHA TT600R M Y 1997 2007 SERVICE MANUAL ...
Страница 5: ......
Страница 6: ...1 GEN INFO ...
Страница 8: ...GEN INFO ...
Страница 17: ...2 SPEC ...
Страница 19: ...SPEC ...
Страница 49: ...SPEC ...
Страница 50: ...3 INSP ADJ ...
Страница 110: ...INSP ADJ ...
Страница 111: ...4 CHAS ...
Страница 200: ...ENG 5 ...
Страница 251: ...ENG ENGINE ASSEMBLY AND SETTING 5 49 ENGINE OIL PUMP AND OIL STRAINER 1 Oil strainer 2 Oil pump 3 Oil pump gear ...
Страница 256: ...ENGINE ASSEMBLY AND SETTING 5 54 ENG TIMING CHAIN 1 Install Timing chain 1 Chain guide 2 ...
Страница 258: ...ENGINE ASSEMBLY AND SETTING 5 56 ENG CYLINDER 1 Gasket 2 Cylinder 3 O Ring 4 Gasket 5 Dowel pin 6 Dowel pin ...
Страница 281: ...6 CARB ...
Страница 283: ...CARB ...
Страница 300: ...7 ELEC ...
Страница 302: ...ELEC ...
Страница 312: ...7 10 ELEC ...
Страница 322: ...7 20 ELEC ...
Страница 336: ...7 34 ELEC ...
Страница 342: ...ELEC 7 40 ...
Страница 352: ...7 50 ELEC ...
Страница 366: ...7 64 ELEC ...
Страница 367: ...8 TRBL SHTG ...
Страница 369: ...TRBL SHTG ...
Страница 379: ...TRBL SHTG ...