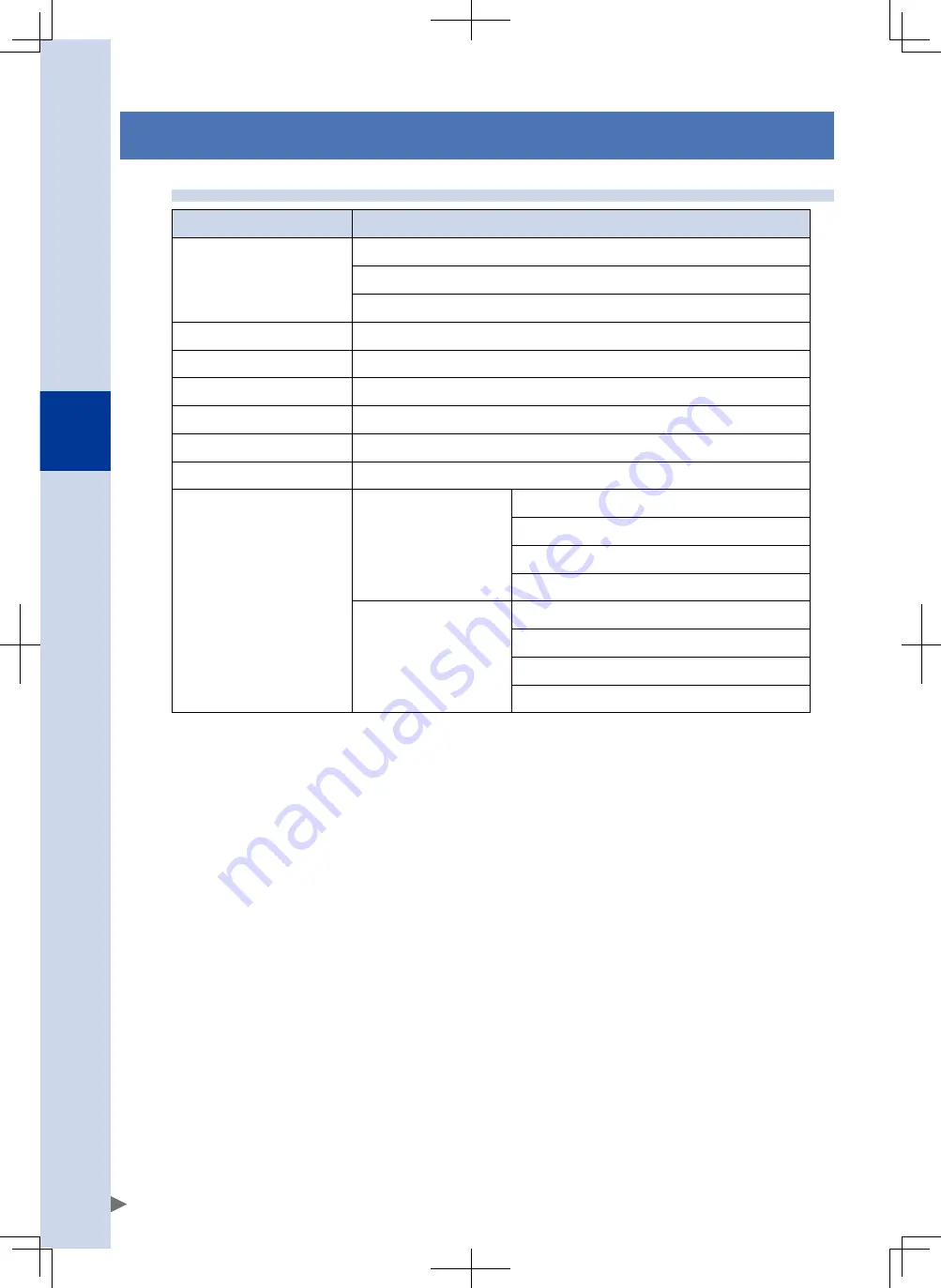
12
Specifications
30
12. Specifications
12.1 Network specifications
Spec. Item
Contents
Supported software versions
RCX340
: V1.62 or later
PBX/PBX-E
: V1.08 or later
RCX-Studio Pro : V2.1.9 or later
ESI file name
YAMAHA RCX340 EtherCAT 1_00.xml
Transmission speed
100Mbps (Auto-negotiation)
Connector specifications
RJ-45 connector (8-pole modular connector) 2 ports
Conforming cable specifications
CAT 5e or higher STP cable (double shield)
Max. cable length
100 m
Monitor LEDs
RUN, ERROR, Link/Activity:Port1-2
Input/output data size
Input : 48bytes
Dedicated word input 2 words (4 bytes)
General-purpose word input 14 words (28 bytes)
Dedicated bit input 16 bits (2 bytes)
General-purpose bit input 112 bits (14 bytes)
Output : 48bytes
Dedicated word output 2 words (4 bytes)
General-purpose word output 14 words (28 bytes)
Dedicated bit output 16 bits (2 bytes)
General-purpose bit output 112 bits (14 bytes)
Содержание RCX340
Страница 1: ...EtherCAT EUSH18A101 E138 Ver 1 01 User s Manual RCX340 YAMAHA NETWORK BOARD ...
Страница 2: ......
Страница 39: ......