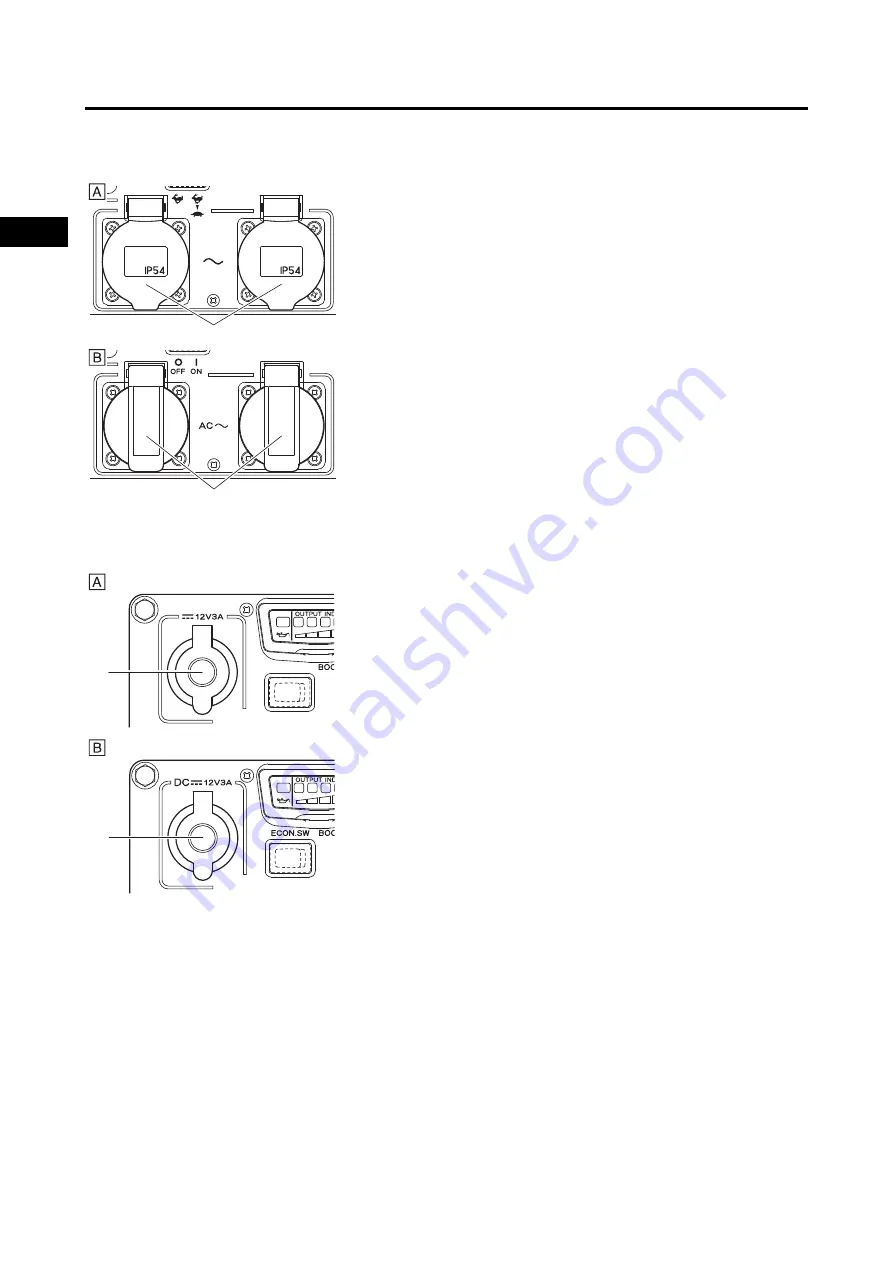
PERIODIC MAINTENANCE
2-28
1
2
3
4
5
6
7
8
9
10
PERIOD
IC C
H
ECK
S
AN
D AD
JU
STMEN
T
S
RECEPTACLE
1.
Check:
• AC receptacle “1”
Cracks/damage
Replace.
Poor connection
Correct.
ACCESSORY SOCKET
1.
Check:
• Accessory socket “1”
Cracks/damage
Replace.
Poor connection
Correct.
1
1
A. For Europe and Korea
B. For Australia and China
1
1
A. For Europe and Korea
B. For Australia and China
Содержание EF2200iS
Страница 1: ...SERVICE MANUAL EF2200iS 7PC F8197 E0 2019 09 1 E 7PC F8197 E0_Hyoshi indd 1 2 2019 08 28 16 31 47 ...
Страница 2: ...7PC F8197 E0_Hyoshi indd 3 4 2019 08 28 16 31 47 ...
Страница 18: ...SPECIAL TOOLS AND TESTERS 1 8 1 2 3 4 5 6 7 8 9 10 GENERAL INFORMATION MEMO ...
Страница 50: ...PERIODIC MAINTENANCE 2 32 1 2 3 4 5 6 7 8 9 10 PERIODIC CHECKS AND ADJUSTMENTS MEMO ...
Страница 99: ...FUEL PUMP 4 7 1 2 3 4 5 6 7 8 9 10 CARBURETOR MEMO ...
Страница 116: ...ELECTRICAL COMPONENTS 5 17 1 2 3 4 5 6 7 8 9 10 ELECTRICAL MEMO ...
Страница 136: ...WIRE ROUTING DIAGRAM 7 14 1 2 3 4 5 6 7 8 9 10 SPECIFICATIONS CONTROL PANEL AND CONTROL BOX FOR AUSTRALIA AND CHINA ...
Страница 138: ...WIRE ROUTING DIAGRAM 7 16 1 2 3 4 5 6 7 8 9 10 SPECIFICATIONS ENGINE AND GENERATOR ...
Страница 140: ...WIRE ROUTING DIAGRAM 7 18 1 2 3 4 5 6 7 8 9 10 SPECIFICATIONS UPPER SIDE AND LEFT SIDE VIEW ...
Страница 142: ...WIRE ROUTING DIAGRAM 7 20 1 2 3 4 5 6 7 8 9 10 SPECIFICATIONS CONTROL UNIT ...
Страница 144: ...WIRE ROUTING DIAGRAM 7 22 1 2 3 4 5 6 7 8 9 10 SPECIFICATIONS GENERATOR ...
Страница 146: ...WIRE ROUTING DIAGRAM 7 24 1 2 3 4 5 6 7 8 9 10 SPECIFICATIONS UPPER SIDE AND AIR FILTER SIDE VIEW ...
Страница 148: ...WIRE ROUTING DIAGRAM 7 26 1 2 3 4 5 6 7 8 9 10 SPECIFICATIONS CARBURETOR AND AIR FILTER ...
Страница 150: ...WIRE ROUTING DIAGRAM 7 28 1 2 3 4 5 6 7 8 9 10 SPECIFICATIONS FUEL TANK AND FUEL HOSES ...
Страница 152: ...WIRE ROUTING DIAGRAM 7 30 1 2 3 4 5 6 7 8 9 10 SPECIFICATIONS ...
Страница 154: ...WIRE ROUTING DIAGRAM 7 32 1 2 3 4 5 6 7 8 9 10 SPECIFICATIONS OIL LEVEL SWITCH CRANKCASE COVER AND CDI MAGNETO 10 10 ...
Страница 160: ...MEMO ...
Страница 161: ...7PC F8197 E0_Hyoshi indd 3 4 2019 08 28 16 31 47 ...
Страница 162: ...SERVICE MANUAL EF2200iS 7PC F8197 E0 2019 09 1 E 7PC F8197 E0_Hyoshi indd 1 2 2019 08 28 16 31 47 ...