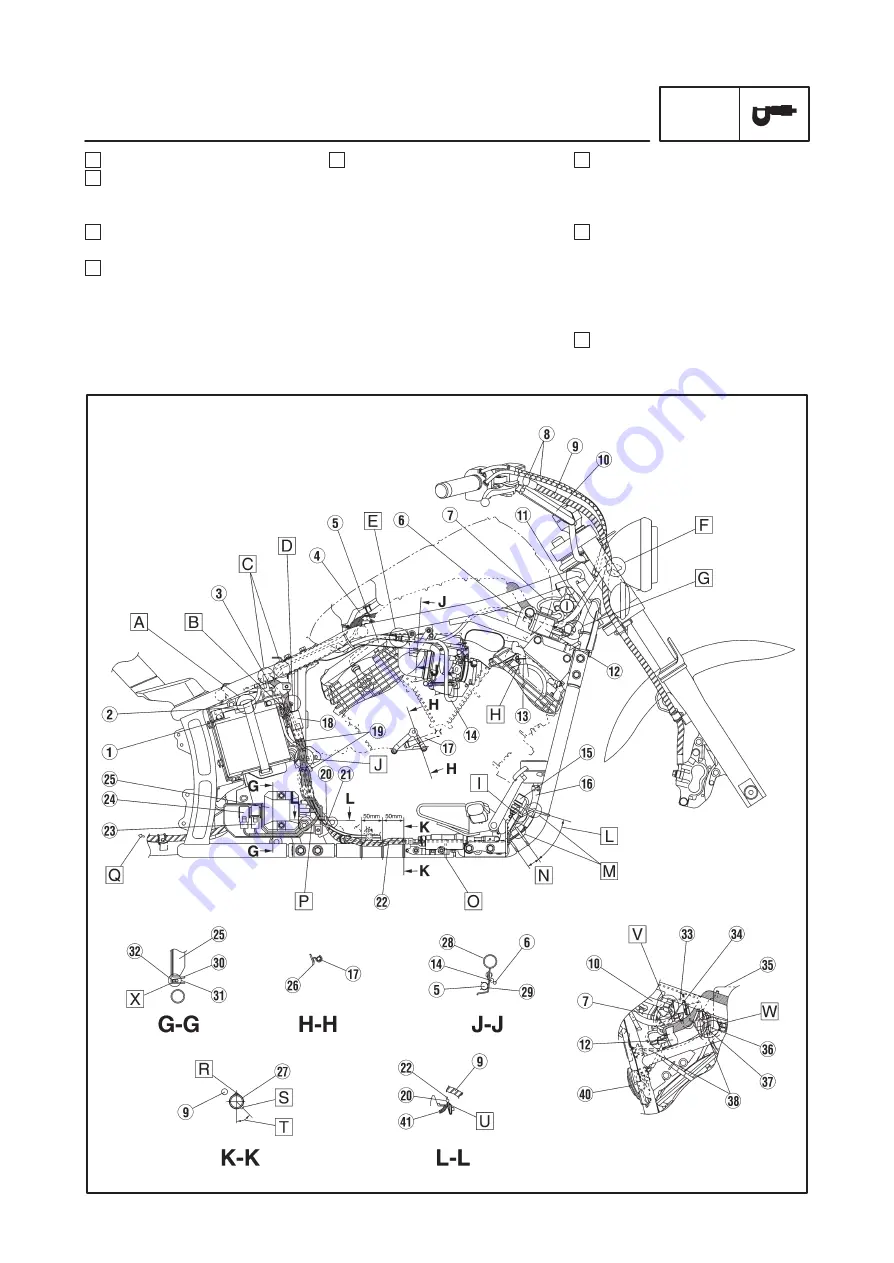
–14–
Q To rear brake.
R Fasten the rear brake switch
lead with a band to down tube.
(four point)
S Cutting part at the edge of the
band.
T About 30
45
CABLE ROUTING
SPEC
U Fasten the oil level sensor lead
with a locking tie to battery box.
Fix to the battery box with the
band. To fix, align the band to the
bottom of the box’s hole while fix-
ing the lead to the back of the box
(inside the body). The cutting part
at the edge of the band comes to
the front side of the body.
V Clamp the handlebar switch lead
(right) to the frame with a holder.
The part to open and shut is out-
side of the body.
W Arrange the throttle position sen-
sor connector, carburetor heater
connector and thermo switch
connector between the starting
circuit cut off relay and high ten-
sion code.
X Put the light reduce relay lead,
carburetor heater lead into the
bottom of the groove.