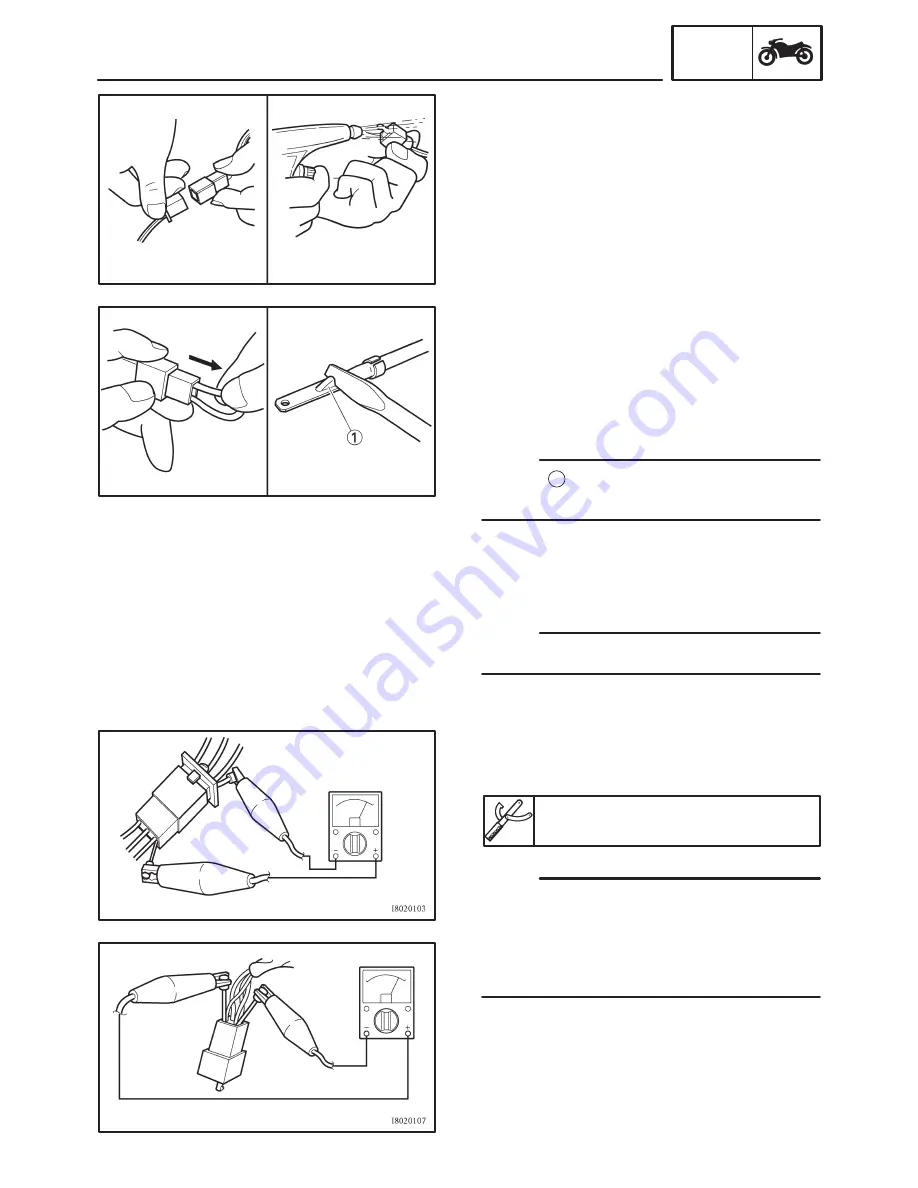
1-9
CHECKING THE CONNECTIONS
GEN
INFO
NOTE:
NOTE:
NOTE:
EAS00026
CHECKING THE CONNECTIONS
Check the leads, couplers, and connectors for
stains, rust, moisture, etc.
1. Disconnect:
S
lead
S
coupler
S
connector
2. Check:
S
lead
S
coupler
S
connector
Moisture
!
Dry with an air blower.
Rust / stains
!
Connect and disconnect sev-
eral times.
3. Check:
S
all connections
Loose connection
!
Connect properly.
If the pin
1
on the terminal is flattened, bend it
up.
4. Connect:
S
lead
S
coupler
S
connector
Make sure all connections are tight.
5. Check:
S
continuity
(with the pocket tester)
Pocket tester
90890-03112, YU-3112
S
If there is no continuity, clean the terminals.
S
When checking the wire harness, perform
steps (1) to (3).
S
As a quick remedy, use a contact revitalizer
available at most part stores.
Содержание 2002 YZF-R6R
Страница 1: ......