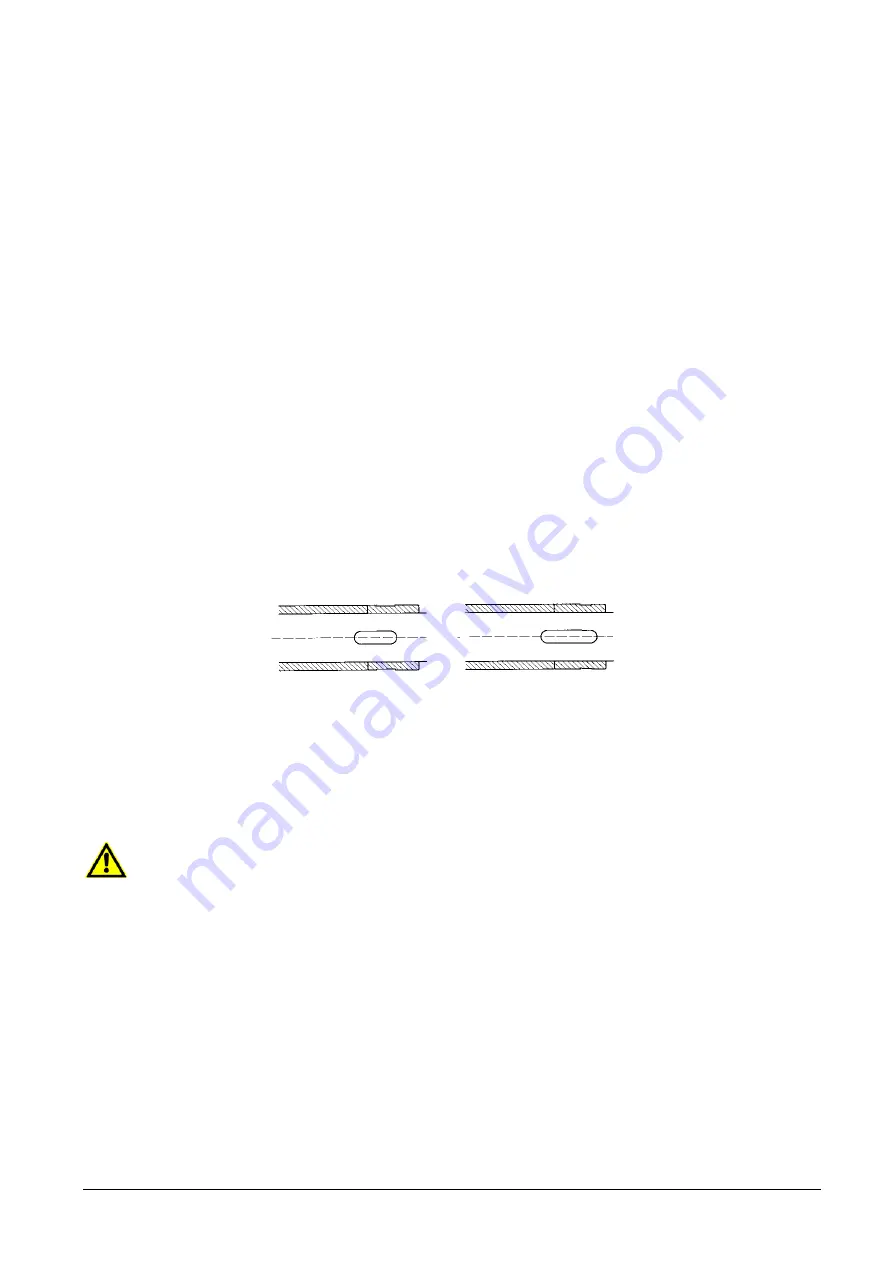
Mounting Instructions MPE
Slide the rotating unit of the mechanical seal off the shaft sleeve (44). If the mechanical seal has securing
screws these must be loosened earlier.
Clean and check all parts for wear. Mechanical seals must always be replaced. Repairing mechanical
seals is only to be recommended with specialist training.
Assembly
Placing the pump in a vertical position is advantageous for the assembly.
Always use a lubricant when mounting mechanical seals. We recommend lubricating the O-ring or rubber
bellows with soap water shortly before it is mounted. Do not use any mineral grease or oil if you are not
absolutely certain that the O-ring is resistant to it.
Insert the counter ring of the mechanical seal (GLRD) in the casing cover (18U). Slide the rotating unit of
the mechanical seal (GLRD) onto the shaft sleeve (44) and secure (if possible).
Work on mechanical seals with a rubber bellows must proceed quickly. This is the only way to guarantee
that the rotating mechanical seal element can still be moved during assembly and can be brought into the
correct position.
Slide on the O-ring (OR4) and apply lubricating agent (e.g. silicon grease) using a brush.
Lubricate the shaft protective sleeve (44) in the borehole so that the O-ring groove remains clean (start
approx. 10-15mm inside).
Standard O-rings made of EP rubber are not resistant to mineral oil or
greases and must not come into contact with them.
Once resistance has been ascertained (e.g. beef
dripping as lubricant or oil-resistant O-rings) the entire shaft (24) may be lubricated.
Slide on the shaft sleeve (44). When sliding on the shaft protective sleeve take care that the O-ring can
slide easily into the groove.
Insert the O-ring (OR3) in the casing and secure with silicon grease. If possible, the O-ring should lie
touching the outer diameter (the O-ring can be enlarged slightly by pulling).
Carefully mount the seal cover (19), taking care that the pin is in the correct direction (S4), (groove in
bearing bracket).
Insert feather key (PF3) and slide on the spacer sleeve (72). Pump must be assembled in the following
direction.
44 → 72
44 → 72
Slide on flinger (73) and bearing cover (12)
For further assembly work see chapter 2.1 and 2.2 (replacing roller bearings) "Assembly".
2.4 Replacement of Balancing bush and Balancing drum
This chapter describes the replacement of the balancing bush and the balancing drum.
The dismantling of the pump body is done best in vertical position. Position the pump on the suction side
bearing bracket (10). A lifting tool is absolutely required for this work.
Secure the pump so that it cannot fall over.
See the "Appendix" for relevant sectional drawing.
Dismantling
Dismantle the pump according chapter 2.1 and 2.2 (dismantling the bearings), as well as chapter 2.3
(replacement of the shaft sleeve at the stuffing box / replacement of the mechanical seal).
Loosen nuts (M1) and remove the tie bolts (25).
Lift the discharge casing (4) (careful blows with a rubber mallet on the discharge casing tie bolt bosses)
and remove the o-ring (OR1).
Remove the balancing bush (53) by striking out of the discharge casing (4).
Pull down the balancing drum (52) together with the spacer ring (71) and the o-ring (OR7).
Remove inside key (PF3).
Assembly
In opposite sequence.
7
/
16