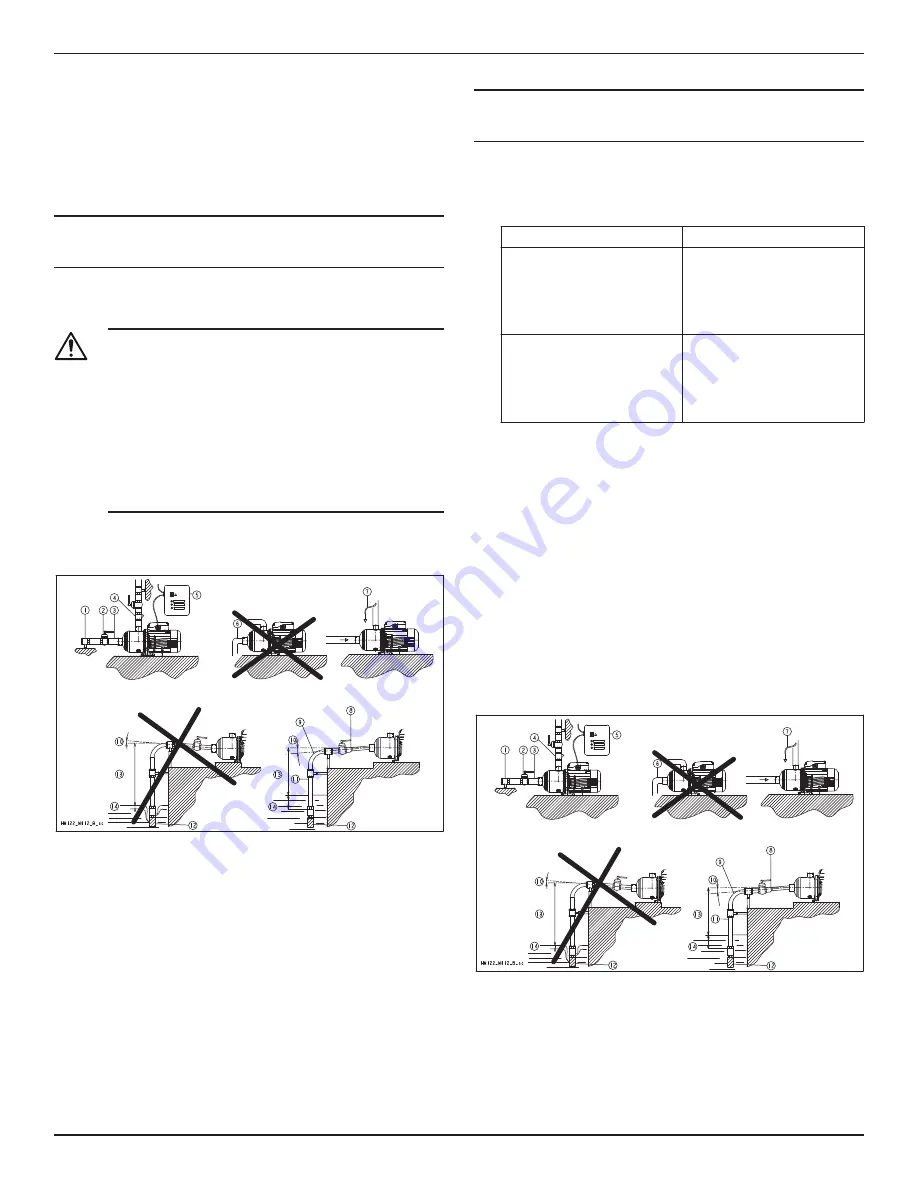
Installation above liquid source (suction lift)
The theoretical maximum suction height of any pump is 34 ft. In prac-
tice, this is not achieved due to the following conditions affecting the
suction capability of the pump:
• Temperature of the liquid
• Elevation above the sea level (in an open system)
• System pressure (in a closed system)
• Resistance of the pipes
• Own intrinsic flow resistance of the pump
• Height differences
NOTICE:
Do not exceed the pumps suction capacity as this could cause cavita-
tion and damage the pump.
4.1.2 Piping requirements
Precautions
CAUTION:
• Use pipes suited to the maximum working pressure of
the pump. Failure to do so can cause the system to rup-
ture, with the risk of injury.
• Make sure that all connections are performed by quali-
fied installation technicians and in compliance with the
regulations in force.
• Do not use the on-off valve on the discharge side in the
closed position for more than a few seconds. If the
pump must operate with the discharge side closed for
more than a few seconds, a bypass circuit must be instal-
led to prevent overheating of the water inside the
pump.
Piping checklist
• Pipes and valves must be correctly sized.
• Pipe work must not transmit any load or torque to pump flanges.
4.2 Electrical requirements
• The local regulations in force overrule these specified require-
ments. In the case of fire fighting systems (hydrants and/or sprin-
klers), check the local regulations.
Electrical connection checklist
Check that the following requirements are met:
• The electrical leads are protected from high temperature, vibra-
tions, and collisions.
• The power supply line is provided with:
• A short-circuit protection device
• A main disconnect switch.
The electrical control panel checklist
NOTICE:
The control panel must match the ratings of the electric pump. Improp-
er combinations could fail to guarantee the protection of the motor.
Check that the following requirements are met:
• The control panel must protect the motor against overload and
short-circuit.
• Install the correct overload protection (thermal relay or motor pro-
tector).
P
Pump Type
Protection
Single phase standard electric
pump up to 3 HP
• Built-in automatic reset
thermal-overload protec-
tion
• Short circuit protection
(must be supplied by the
installer)
Three-phase electric pump
• Thermal protection (must
be supplied by the instal-
ler)
• Short circuit protection
(must be supplied by the
installer)
• The control panel must be equipped with a dry-running protec-
tion system to which a pressure switch, float switch, sensors, or
other suitable device is connected.
• The following devices are recommended for use on the suction
side of the pump:
• When the liquid is pumped from a water system, use a pres-
sure switch.
• When the liquid is pumped from a storage tank or reservoir,
use a float switch or sensors.
• When thermal relays are used, relays that are sensitive to phase
failure are recommended.
The motor checklist
Use cable according to rules with 3 leads (2+earth/ground) for single
phase versions and with 4 leads (3+earth/ground) for three-phase ver-
sion.
4.3 Install the pump
4.3.1 Install the pump on a concrete foundation
1.
Piping support
2.
On-off valve
3.
Flexible pipe or joint
4.
Check valve
5.
Control panel
6.
Do not install elbows close to the pump
7.
Bypass circuit
8.
Eccentric reducer
9.
Use wide bends
10. Positive gradient
11. Piping with equal or greater diameter than the suction port
4 Installation
4
Model e-HM Installation, Operation, and Maintenance Manual
Содержание GOULDS e-HM Series
Страница 1: ...Installation Operation and Maintenance Manual Model e HM ...
Страница 2: ......