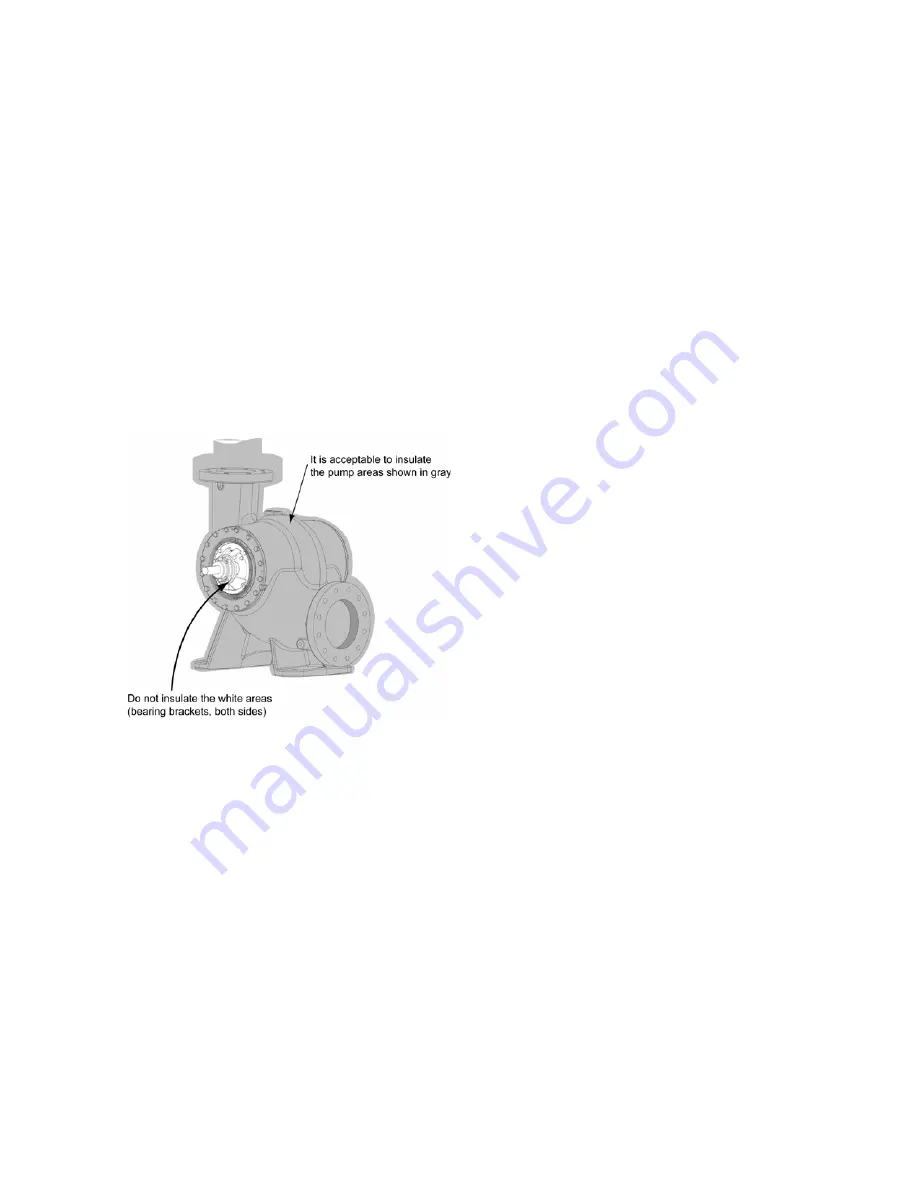
1
Pressure Gauges
Properly sized pressure gauges should be
installed in both the suction and discharge
nozzles in the gauge taps. The gauges will
enable the operator to easily observe the
operation of the pump, and also determine if
the pump is operating in conformance with
the performance curve. If cavitation, vapor
binding, or other unstable operation should
occur, widely fluctuating discharge pressure
will be noted.
Pump Insulation
On applications where pumps are insulated,
the pump bearing brackets should not be
insulated since this would tend to trap heat
inside the housing. This could lead to
increased bearing temperatures and
premature bearing failures.
Figure 16: Pump Insulation
PUMP SEALING
Mechanical Seals
Mechanical seals are preferred over packing
on some applications because of better
sealing qualities and longer serviceability.
When a seal is properly installed, it will last
longer than packing on similar applications.
The change from packing to an alternate
arrangement may be made in the field by
competent service personnel. Conversion
parts may be ordered from your local Bell &
Gossett representative.
Packing
Contaminants in the pumped liquid must not
enter the stuffing box. These contaminants
may cause severe abrasion or corrosion of
the shaft sleeve, and rapid packing
deterioration; they can even plug the stuffing
box flushing and lubrication system. The
stuffing box must be supplied at all times with
a source of clean, clear liquid to flush and
lubricate the packing.
If the pump system pressure conditions vary
during the day, packing adjustment becomes
difficult. Consideration should be given to
using a mechanical seal.
Standard pumps are normally packed before
shipment. If the pump is installed within 60
days after shipment, the packing will be in
good condition with a sufficient supply of
lubrication. If the pump is stored for a longer
period, it may be necessary to repack the
stuffing box. In all cases, however, inspect
the packing before the pump is started.
NOTE:
Packing adjustment is covered in the
section entitled
Maintenance
.
On some applications, it is possible to use internal
liquid lubrication (pumped liquid) to lubricate
packing. Only when all of the following conditions
prevail, can this be done:
1. Liquid is clean, free from sediment and
chemical precipitation and is compatible
with seal materials.
2. Temperature is above 32°F and below
160°F.
3. Suction pressure is below 75 psig.
4. Lubrication (pumped liquid) has lubricating
qualities.
5. Liquid is non-toxic and non-volatile.
When the liquid being pumped contains solids or
is otherwise not compatible with packing materials,
an outside supply of flush liquid should be
furnished. In general, external-flush liquid (from an
outside source) is required when any of the above
conditions cannot be met.
The standard stuffing box consists of rings of
packing (See the
Assembly and Disassembly
Procedures
section for the number of rings), a
lantern ring, and a gland. A shaft sleeve that
extends through the box and under the gland is
provided to protect the shaft.
A tapped hole is supplied in the stuffing box
directly over the lantern ring to introduce a clean,
cooling medium. The stuffing box must, at all
Содержание Bell & Gossett VSC Series
Страница 5: ......
Страница 19: ...1 Figure 18 Vee cut Impeller Diameters ...
Страница 22: ......
Страница 23: ......
Страница 28: ...26 SERVICE Figure 22 Mechanical View ...
Страница 37: ...3 5 ...
Страница 43: ...NOTES ...