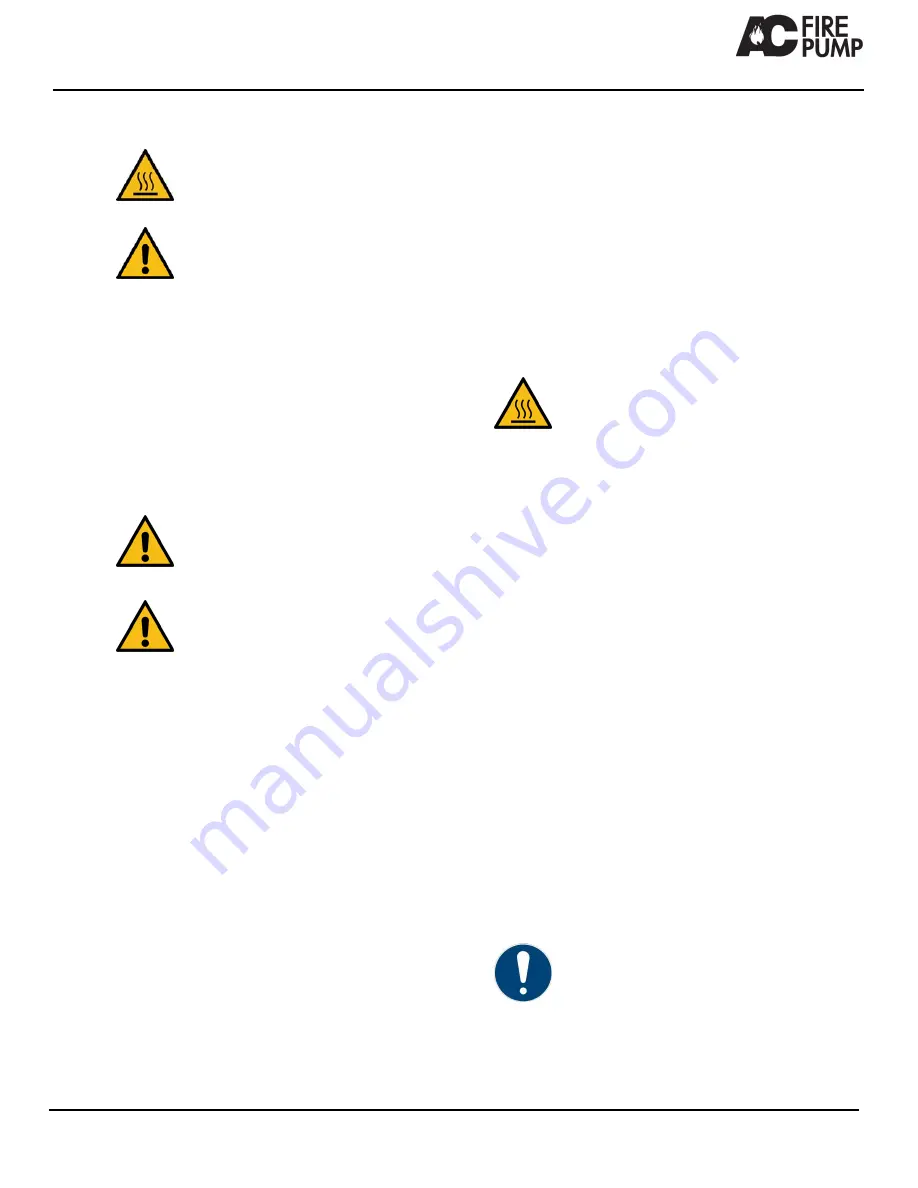
AC6102 Rev 0
5
30
9.3.2
Grease Lubrication
WARNING
Never check the temperature of the bearing
frame by hand, use a temperature measuring
device.
CAUTION
Greases of different bases (lithium, polyurea,
etc.) may not be compatible when mixed.
Mixing greases can result in reduced
lubricant life and premature bearing failure.
Grease lubricated ball bearings are packed with grease at the
factory and ordinarily will require no attention before starting,
provided the pump has been stored in a clean, dry place prior
to its first operation.
The bearing temperature, measured at the bearing frame,
should never exceed 225°F [107°C] for polyurea-based
grease, and 180°F [82°C] for lithium-based grease when
checked monthly. Should the temperature of the bearing
frame rise above the limit, the pump should be shut down to
determine the cause.
9.3.3
Lubrication procedure
CAUTION
Over-greasing is the most common cause of
overheating and premature bearing failure.
CAUTION
Use only manual grease gun. High pressure
may damage the bearings or seals, cause
unnecessary loss of grease, create a danger of
overheating due to over-greasing, and produce
unsightly conditions around the bearing.
Add grease while the pump is stopped to avoid overloading.
Adequate lubrication is assured if the level of grease is
maintained at about the capacity of the bearing and 1/3 to 1/2
of the cavity between the bearing and grease fitting. Any
greater amount will, as a rule, be discharged by the seal or
vent and be wasted.
To lubricate the bearings with grease, proceed as follows:
1.
Remove dirt from the grease fitting.
2.
Fill the grease cavities through the fittings with the
recommended grease.
3.
Wipe off any excess grease.
4.
Run the pump to distribute the grease.
The bearing temperature usually increases after you re-
grease due to an excess supply of grease. Temperatures
return to normal as the pump runs and purges the excess
grease from the bearings.
9.4
Packed Stuffing Box
9.4.1
Packing specifications
Pumps are supplied with a graphite-coated general service
fiber packing as standard, using
Y.C. Industries Grade 608D
,
or equivalent.
9.4.2
Packing maintenance
In accordance with the maintenance schedule, the packing
should be visually inspected once a month and the leakage
rate checked. If the leakage rate is excessive then the gland
nuts may be tightened, until the required leak rate is obtained,
which should be least 40 to 60 drops per minute.
When the gland follower has reached the limit of its
movement and the packing cannot be compressed any
further, all of the packing should be removed and replaced.
Never reuse old and lifeless packing or merely add some
new rings.
9.4.3
Removal of Packing
WARNING
Ensure that the pump has cooled sufficiently to
allow safe handling of the stuffing box. A
packing tool should be used to remove all old
packing from the stuffing box. Make sure the
stuffing box is thoroughly cleaned before new
packing is installed. Also check the condition of
the shaft or sleeve for possible scoring or
eccentricity. Any parts with significant damage
should be replaced.
9.4.4
Installing Packing
New packing may be supplied as molded rings made to
specified dimensions or, more usually, as a length of coil.
When supplied as a continuous length, it is necessary to cut
off lengths of material to make the required number of rings.
Usually 5 or 6 rings are required per stuffing box.
If molded rings are used, the rings should be opened
sideways and the joints pushed into the stuffing box first.
If coil packing is used, wrap the packing around the shaft and
mark the cutting position. The packing should be cut 1/8-1/4
in. [3-6mm] over size. The larger the shaft diameter, the more
excess length is required. The packing must not be cut
undersized. Cut one ring to accurate size with either a butt or
mitered (45°) joint. (An accurately cut butt joint is superior to a
poor fitting mitered joint).
Fit the ring over the shaft to assure proper length. Then
remove and cut all other rings to the first sample. When the
rings are placed around the shaft a tight joint should be
formed.
Place the first packing ring around the shaft, and form a neat
butt or mitered joint between the two ends. Push the ring into
the stuffing box. Push the joint first, then the side opposite to
the joint, and then the two remaining sides. It is essential that
the two packing ends are pushed tightly together.
Push the ring to the bottom of the stuffing box, applying
reasonable pressure to ensure that the ring is seated properly
but it is not over compressed.
NOTICE
The packing rings must be fitted individually
and under no circumstances should complete
sets be fitted as a unit.
The rings are installed one at a time, each ring seated firmly
and the joints staggered at about 90° rotation from each
preceding joint. For 3 adjacent rings, use the 4, 8 and 12
o’clock positions.
Содержание AC Fire Pump 8100 Series
Страница 2: ...Series 8100 8150 8200 9100 Fire Pump 1 AC6102 Rev 05...
Страница 4: ...Series 8100 8150 8200 9100 Fire Pump 3 AC6102 Rev 05...
Страница 8: ...Series 8100 8150 8200 9100 Fire Pump 7 AC6102 Rev 05...
Страница 41: ...AC6102 Rev 05 40 Table 14 Troubleshooting List...
Страница 50: ...Series 8100 8150 8200 9100 Fire Pump 49 AC6102 Rev 05 A Appendix...