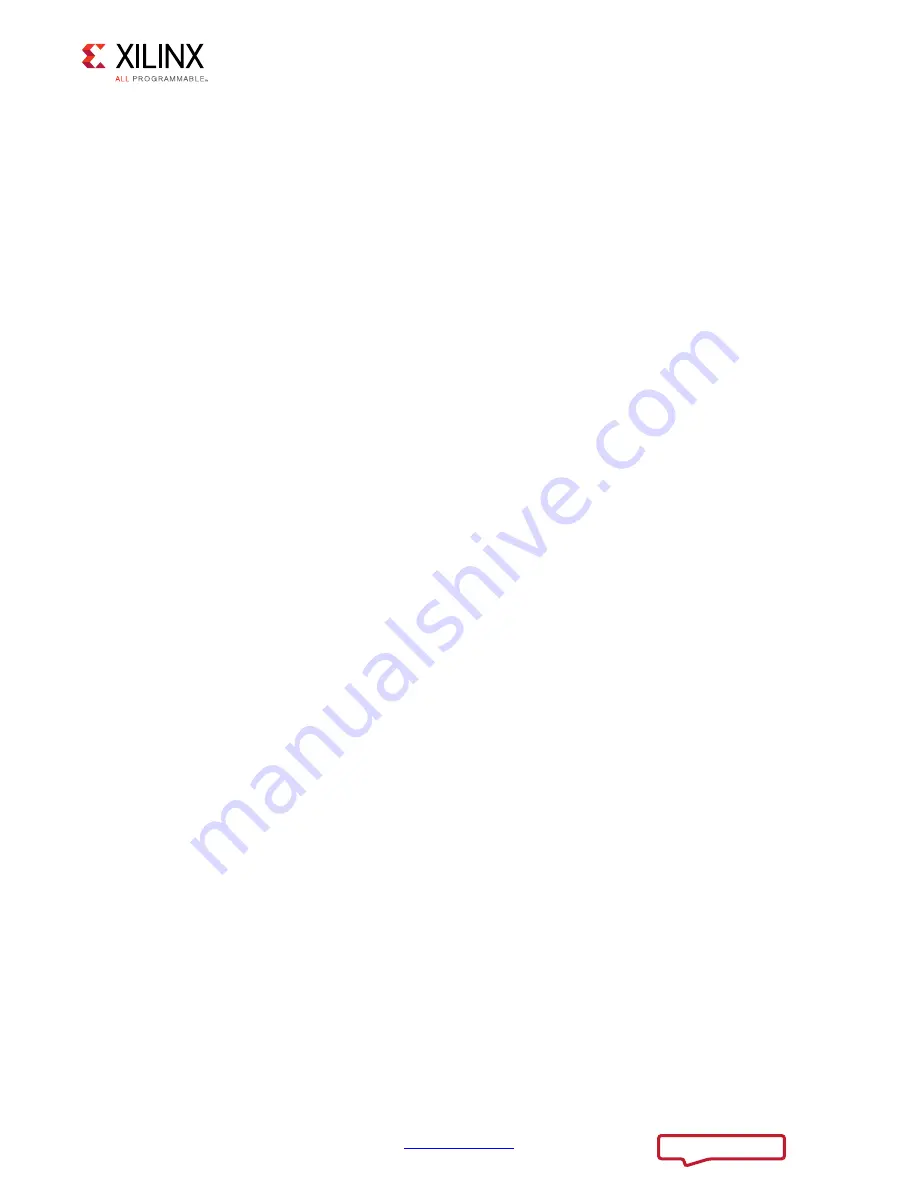
Zynq-7000 PCB Design Guide
9
UG933 (v1.8) November 7, 2014
Chapter 2:
PCB Technology Basics
Lands
For the purposes of soldering surface mount components, pads on outer layers are typically
referred to as lands or solder lands. Making electrical connections to these lands usually
requires vias. Due to manufacturing constraints of PTH technology, it is rarely possible to
place a via inside the area of the land. Instead, this technology uses a short section of trace
connecting to a surface pad. The minimum length of the connecting trace is determined by
minimum dimension specifications from the PCB manufacturer. Microvia technology is not
constrained, and vias can be placed directly in the area of a solder land.
Dimensions
The major factors defining the dimensions of the PCB are PCB manufacturing limits, AP SoC
package geometries, and system compliance. Other factors such as Design For
Manufacturing (DFM) and reliability impose further limits, but because these are
application specific, they are not documented in this user guide.
The dimensions of the AP SoC package, in combination with PCB manufacturing limits,
define most of the geometric aspects of the PCB structures described in this section, both
directly and indirectly. This significantly constrains the PCB designer. The package ball pitch
(1.0 mm for FF packages) defines the land pad layout. The minimum surface feature sizes of
current PCB technology define the via arrangement in the area under the device. Minimum
via diameters and keep-out areas around those vias are defined by the PCB manufacturer.
These diameters limit the amount of space available in-between vias for routing of signals
in and out of the via array underneath the device. These diameters define the maximum
trace width in these breakout traces. PCB manufacturing limits constrain the minimum trace
width and minimum spacing.
The total number of PCB layers necessary to accommodate an AP SoC is defined by the
number of signal layers and the number of plane layers.
• The number of signal layers is defined by the number of I/O signal traces routed in and
out of an AP SoC package (usually following the total User I/O count of the package).
• The number of plane layers is defined by the number of power and ground plane layers
necessary to bring power to the AP SoC and to provide references and isolation for
signal layers.
Most PCBs for large AP SoCs range from 12 to 22 layers.
System compliance often defines the total thickness of the board. Along with the number of
board layers, this defines the maximum layer thickness, and therefore, the spacing in the Z
direction of signal and plane layers to other signal and plane layers. Z-direction spacing of
signal trace layers to other signal trace layers affects crosstalk. Z-direction spacing of signal
trace layers to reference plane layers affects signal trace impedance. Z-direction spacing of
plane layers to other plane layers affects power system parasitic inductance.