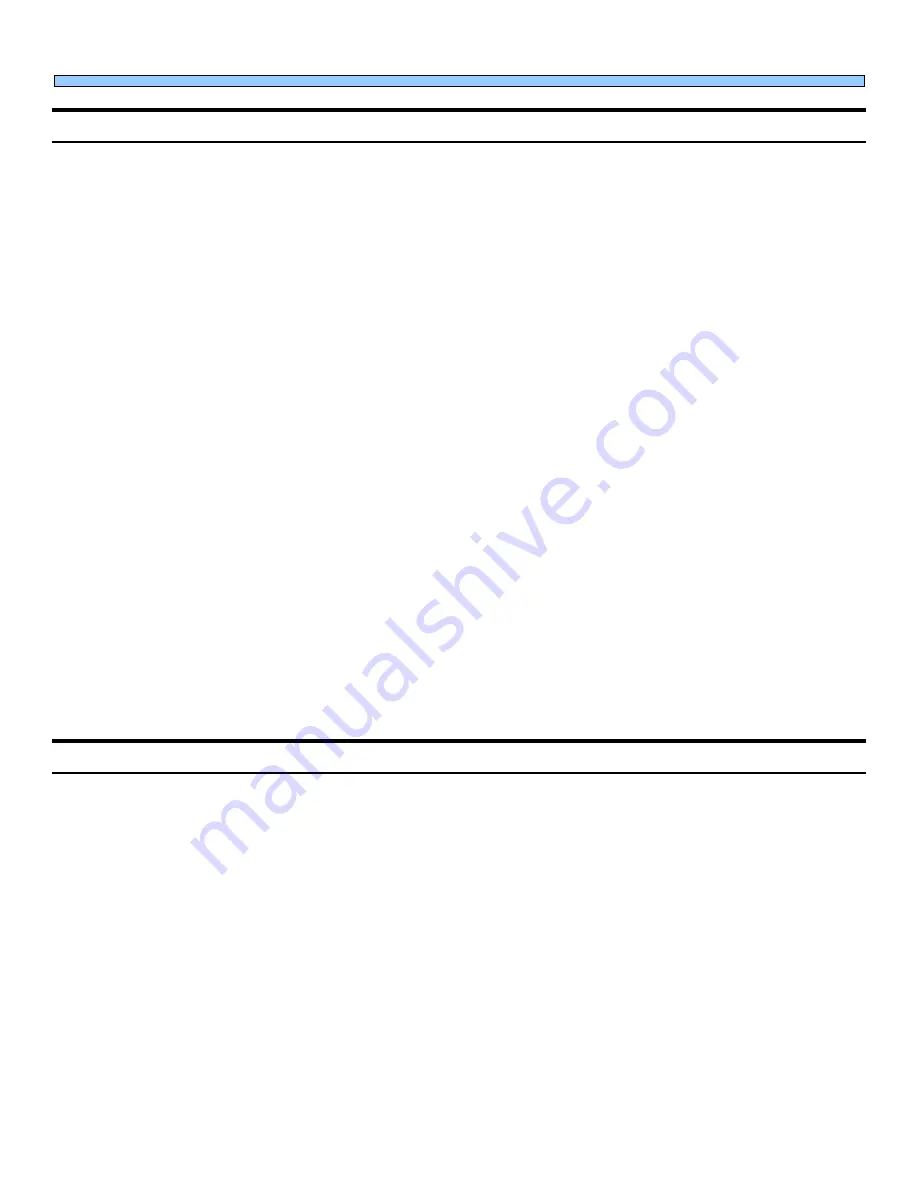
For more information on Genuine Xerox Supplies, call 1-800-822-2200 in the USA and 1800-668-0133 in Canada
4
Side t o Side Regist rat ion Considerat ions- Paper St ret c h
When running two sided printing applications side to side registration may be effected by the inherent
paper stretch that occurs as the paper passes through the high pressure and temperature nip.
Typical paper stretch for light uncoated materials is between 0.2% and 0.6% of the paper size in the
process direction. For coated materials the effect can be as high as 0.9% of the paper size in the
process direction.
As a summary, the following observations are relevant to the stretch of paper in belt-nip fusing:
1) The paper stretch problem is most apparent with coated papers. Most coated papers stretch
significantly more than uncoated papers due to the larger frictional stresses experienced by
coated stocks and softening of the paper.
2) The direction of feed with respect to the orientation of paper fibers also determines the amount of
stretch. Papers fed in the CD (grain perpendicular to process direction) stretch significantly more
than papers fed in the MD (grain parallel to process direction).
3) Increasing the basis weight decreases the stretch since less stress is experienced due to the
increased thickness.
4) The synthetic material tested (DuraPaper 10 pt) actually contracts as it passes through the fuser.
Paper stretch correction can be done using the “tools” mode registration adjustment, but front-to-back
trim mark registration may not always be possible. This is because the side-1 image expands by the
same amount that the paper stretches, thus making it necessary to expand the side-2 image by the
same distortion amount. In order to compensate for this you can use the Alignment Adjustment tool
(refer to the System Administration Guide Tools Mode Chapter). The tool will allow you to create up
to 20 custom profiles for individual paper stocks. Lead / Side registration, Perpendicularity, Skew,
and Image Magnification (Process and Cross-Process directions) parameters can be adjusted for
optimum registration performance.
Tabbed Insert s
Customers can print one-sided tabbed inserts from onboard trays 1,2 and SFM trays 3,4 using the
appropriate size and weight setting. Tabbed stock should be loaded into the trays such that the long
edge is fed first (LEF), with the tabs towards the left side of the paper tray (trail edge). Then go to
NVM Read / Write
in the tools mode (refer to the
System Administration Guide
Tools Mode Chapter)
and enter chain link 700-546. Change the default setting from “0” (on) to “1” (off). This will allow
tabbed inserts to be run without interfering with machine paper size sensors.
Please remember to
reset the default value to “0” when you are finished running tabbed inserts.
The machine will
not function properly if this value is not reset. Verify the size of the material since tabbed inserts may
need to be run as a non-standard paper size. The typical size for tabs to be used with letter size
paper is 11”x 9”. Use 11” as the “x” coordinate and 9” as the “y” dimension in the user interface non-
standard paper size window of the tools mode (refer to the System Administration Guide for
instructions to setup non-standard paper sizes). For tabs used with A4 paper use 296mm as the “x”
dimension and 223.5 mm for the “y” dimension. With guides in place, the paper tray should then be
loaded and set to “Non Standard” size. Once the drawer is closed, the user interface should