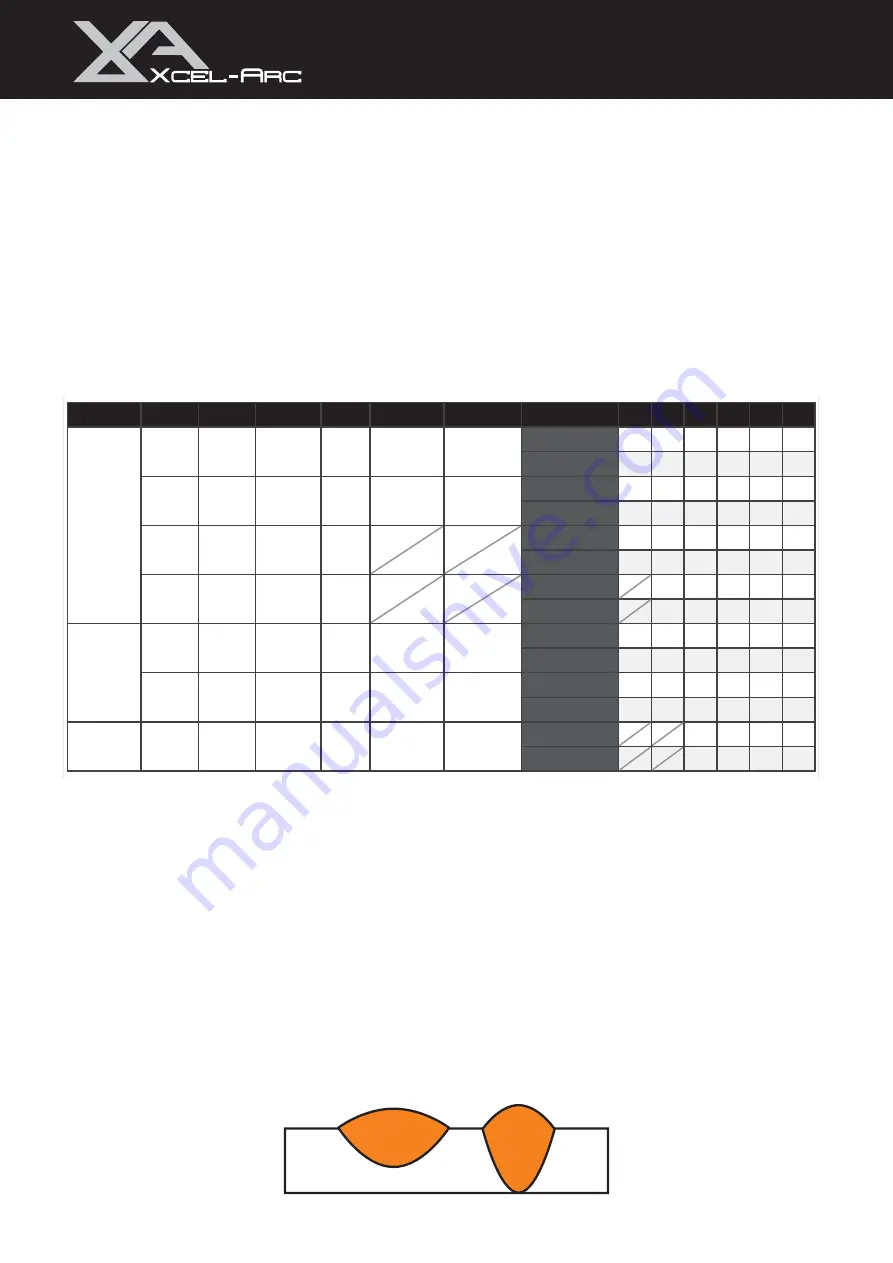
28
VIPER MIG 165
OPERATING MANUAL
11.8 Wire Types and Sizes
Use the correct wire type for the base metal being welded. Use stainless steel wire for stainless steel, aluminium wires for
aluminium and steel wires for steel.
Using poor quality milled wire can result in poor performance and appearance. To ensure optimal performance
when welding, use standards approved wire.
Use a smaller diameter wire for thin base metals. For thicker materials use a larger wire diameter and larger machine.
Check the recommended welding capability of your machine.
As a guide, refer to the "Welding Wire Thickness Chart" below.
11.9 Gas Selection
The purpose of the gas in the MIG process is to shield the wire, the arc and the molten weld metal from the atmosphere.
Most metals when heated to a molten state will react with the air in the atmosphere, without the protection of the shielding
gas the weld produced would contain defects like porosity, lack of fusion and slag inclusions. Additionally, some of the gas
becomes ionised (electrically charged) and helps the current flow smoothly.
The correct gas flow is critical in protecting the welding zone from the atmosphere.
Too low a flow will give inadequate coverage and result in weld defects and unstable arc conditions.
Too high a flow can cause air to be drawn into the gas column and contaminate the weld zone.
Use the correct shielding gas. CO2 is suitable for steel and offers good penetration characteristics; the weld profile is
narrower and slightly more raised than the weld profile obtained from Argon CO2 mixed gas. Argon CO2 mix gas offers
better weldability for thin metals and has a wider range of setting tolerance on the machine. Argon 5/2 is a good all-round
mix suitable for most applications.
MIG: Welding Guide
Argon-CO₂
CO₂
Material
Type
Electrode Type Electrode Thickness 2.5mm 3.2mm 4.0mm
Steel
HYPERARC™
GP 6013
Amperage Range (A)
50-9/0A 90-130A 110-170A
Polarity
DCEP+
HYPERARC™
16TC
Amperage Range (A)
50-90A 80-130A 110-180A
Polarity
DCEP+
Stainless
Steel
HYPERARC™
316L
Amperage Range (A)
50-90A 70-110A 100-150A
Polarity
DCEP+
Tungsten
Diameter
Filler
Rod
Material
1.6mm
3.2mm 4.8mm 6.0mm
1.6mm
1.6mm
Steel
60-90A
80-115A
Stainless
40-70A
65-110A
2.4mm
2.4mm
Steel
115-165A
Stainless
100-150A
3.2mm
2.4mm
Steel
160-200A
Stainless
135-180A
Manual MIG Setup Guide
Synergic MIG Setup Guide
Stick Setup Guide
TIG Setup Guide (Pure Argon Gas / DC- Polarity)
Polarity: MIG
Polarity: TIG
Polarity: Stick
Material Type
Wire Type
Wire Size
Drive Roller
Polarity
Shielding Gas
Gas Flow Rate
Material Thickness
1mm 2mm 3mm 4mm 6mm 8mm
Steel
ER70S-6
0.8mm
V Groove
DCEP+
Argon 5/2
8-12L/min
Voltage (V)
14.4
15.5
17.6
18.4
19.7
21.7
Wire Speed (m/min)
3.9
4.3
6.1
7.1
9.6
11.9
ER70S-6
0.9mm
V Groove
DCEP+
Argon 5/2
8-12L/min
Voltage (V)
15.5
17
18
18.8
20.7
22
Wire Speed (m/min)
4.4
5
6.3
7
9.1
9.6
E71T-11
0.8mm
F Groove
(Knurled)
DCEN-
Voltage (V)
14
15
15.8
16.5
17.7
18.4
Wire Speed (m/min)
4
4.6
5.2
5.3
7
7.4
E71T-11
0.9mm
F Groove
(Knurled)
DCEN-
Voltage (V)
15.3
16
16.8
18.1
19
Wire Speed (m/min)
4.7
5.5
5.8
7.3
7.8
Stainless Steel
316LSi
0.8mm
V Groove
DCEP+
Argon CO
2
98/2
8-12L/min
Voltage (V)
14.5
15.4
18.1
18.9
20.8
21.8
Wire Speed (m/min)
4
4.4
7
9.8
9.9
12.9
316LSi
0.9mm
V Groove
DCEP+
Argon CO
2
98/2
8-12L/min
Voltage (V)
15.8
17.4
19
19.8
21
22
Wire Speed (m/min)
4.5
5.2
7.1
8
9.7
11.7
Aluminium
5356
1.0mm
U Groove
DCEP+
Pure Argon
8-12L/min
Voltage (V)
15.7
16.7
17.6
20.4
Wire Speed (m/min)
9.7
10.2
11.4
13.9
Material Type
Wire Type
Wire Size
Drive Roller
Polarity
Shielding Gas
Gas Flow Rate
Material Thickness
1mm 2mm 3mm 4mm 6mm 8mm
Steel
ER70S-6
0.8mm
V Groove
DCEP+
Argon 5/2
8-12L/min
Amp
70
80
95
110
130
155
ER70S-6
0.9mm
V Groove
DCEP+
Argon 5/2
8-12L/min
Amp
95
100
110
125
140
165
E71T-11
0.8mm
F Groove
(Knurled)
DCEN-
Amp
90
95
100
110
130
135
E71T-11
0.9mm
F Groove
(Knurled)
DCEN-
Amp
125
130
135
145
155
Stainless Steel
316LSi
0.8mm
V Groove
DCEP+
Argon CO
2
98/2
8-12L/min
Amp
55
65
80
95
125
150
316LSi
0.9mm
V Groove
DCEP+
Argon CO
2
98/2
8-12L/min
Amp
60
80
95
110
130
155
Aluminium
5356
1.0mm
U Groove
DCEP+
Pure Argon
8-12L/min
Amp
110
115
125
140
DC+ Electrode
(Gas-shielded)
Earth Clamp (-)
Polarity Cable (+)
Polarity Cable (-)
Earth Clamp (+)
DC- Electrode
(Gasless)
Earth Clamp (+)
TIG Torch (-)
This setup information is intended to act as a guide only. Individual results may vary depending on technique, skill and material. Please refer to the operating manual for further instructions.
Please refer to electrode packaging
for correct polarity settings.
DC+ Electrode
Electrode Holder (+)
Earth Clamp (-)
DC- Electrode
Earth Clamp (+)
Electrode Holder (-)
DC+ Electrode
DC- Electrode
VIPER MULTI 165
Welding Setup Guide
0802 VIPER 165 SYNERGIC Setup Guide AUG22.indd 1
0802 VIPER 165 SYNERGIC Setup Guide AUG22.indd 1
16/08/2022 9:07:26 AM
16/08/2022 9:07:26 AM