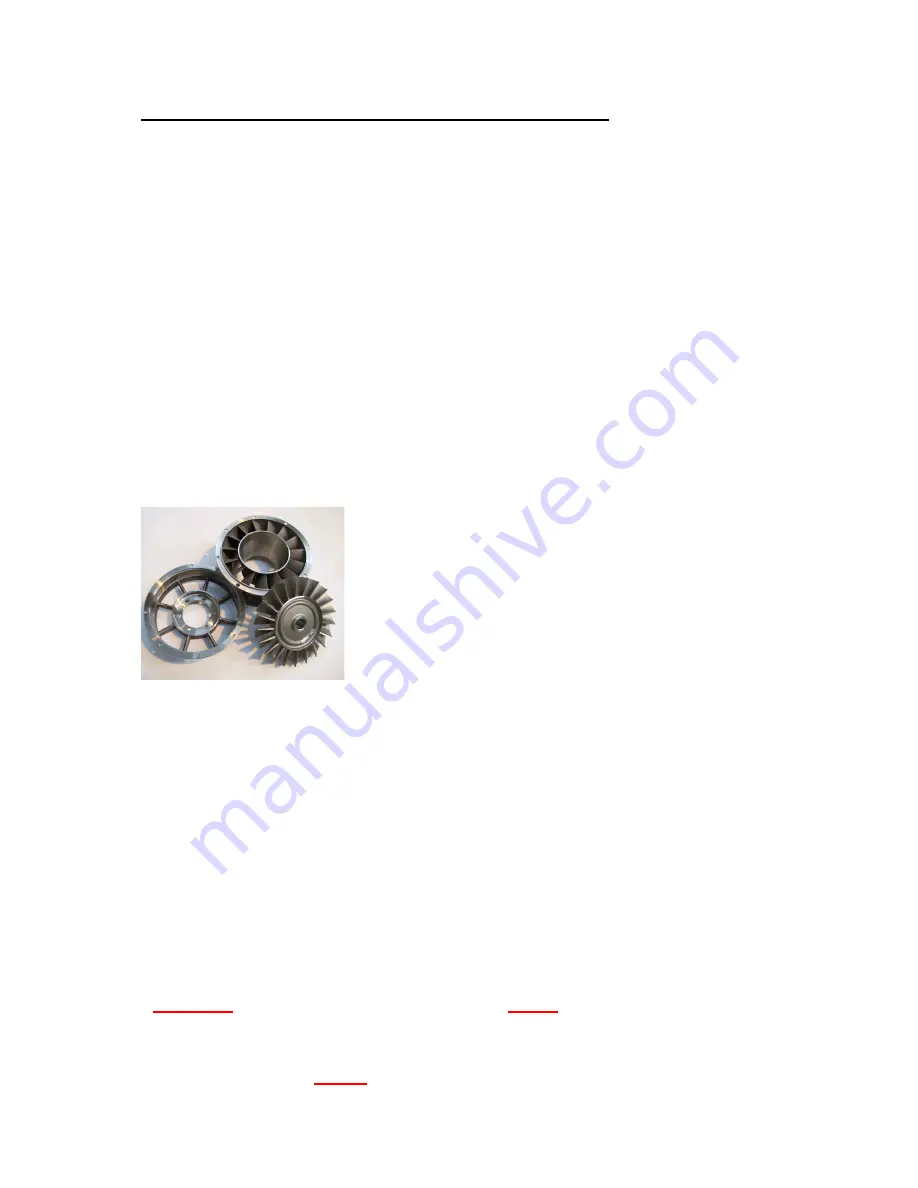
Wren 44 Gold Helicopter Owners Manual
Page 8
General description of the Wren 44 two-shaft drive system
The following notes introduce the main parts of the assembly and offer an insight to the use
and operation of the unit as a whole;
The Wren 44 Helicopter Unit is the world’s smallest commercial 2-shaft helicopter engine. It
is designed for use in miniature helicopter applications in place of an I/C engine. It is
generally suited to helicopters up to 25kg (55lb) in all up weight and will replace I/C engines
of around 15-30cc (0.9 to 1.8cu inch).
What is a two-shaft system?
The two shaft drive system means there are two independent shafts running within the unit.
The first shaft is contained within the engine end of the unit and rotates at very high speed
(up to 195,000rpm) with just a small compressor wheel at one end and axial flow turbine at
other end. This forms the
gas generator
. The engine end of the unit generates a flow of gas
at high pressure and volume, and its operation is exactly as a small gas turbine engine. If a
nozzle was attached to the outlet of the engine it would imparts a slight squeezing of the gas
into a high velocity jet for producing jet thrust as would be the configuration for a thrust
engine. For a gas generator version of the engine, instead of squeezing the gas through a
nozzle it is redirected by another vane assembly to turn a 2nd turbine wheel mounted on the
2nd stage shaft. This is driven round in the gas stream and this rotation drives the input shaft
to the gearbox and onwards to the helicopter drive.
The 2nd turbine is larger in diameter (66mm) than the 1st
stage and runs much slower - up to
only around
80,000rpm -
still far higher than any 2-stroke or electric motor could
achieve, but at a higher torque level. The energy given up by
the gas driving the 2nd stage turbine drastically reduces the
velocity of the exhaust gas with the result than only a small
residual thrust remains from the exhaust outlets.
What happens if I stall the output shaft in a bad landing?
In a situation that causes the output shaft to stall, the gas
generator will continue to function normally with little ill-effects. On releasing the shaft from
its stalled form it will spin back up to it's normal running speed. This should be born in mind
when retrieving the model from long grass or crash situation – never try to pick up the model
whilst the engine is running.
What sort of gearbox is required to convert the 2
nd
turbine speed to something I need?
The rpm generated by the large diameter 2nd stage turbine is from zero to around
75,000rpm depending on loading and gas generator flow. This enables a suitable reduction
to be contained in a simple single stage gearbox, the ratio of which is chosen to suit the
operational needs of the load driven. The 44Heli reduction is 4.285:1 and this gives an
output shaft speed range of zero-20,000rpm. The 2nd turbine has a wide operating rpm
range and may be slowed with high load or allowed to speed up with low load without
upsetting the 1st stage, therefore the choice of rotor blade or subsequent reduction beyond
the engine is not at all critical, providing it presents enough load for the system. The main
criteria for reduction ratio choice being the type of heli the unit is fitted to (scale, aerobatic,
sports etc) and the length of rotor blade required to be driven.
WARNING - it is most important that there must always be some load on the output
shaft as otherwise the 2nd stage turbine will be running unrestrained and may easily
speed up beyond it's safe running speed, even when the gas generator is running at
only a modest rpm.
The unit must
NEVER
be revved up without a suitable load attached.