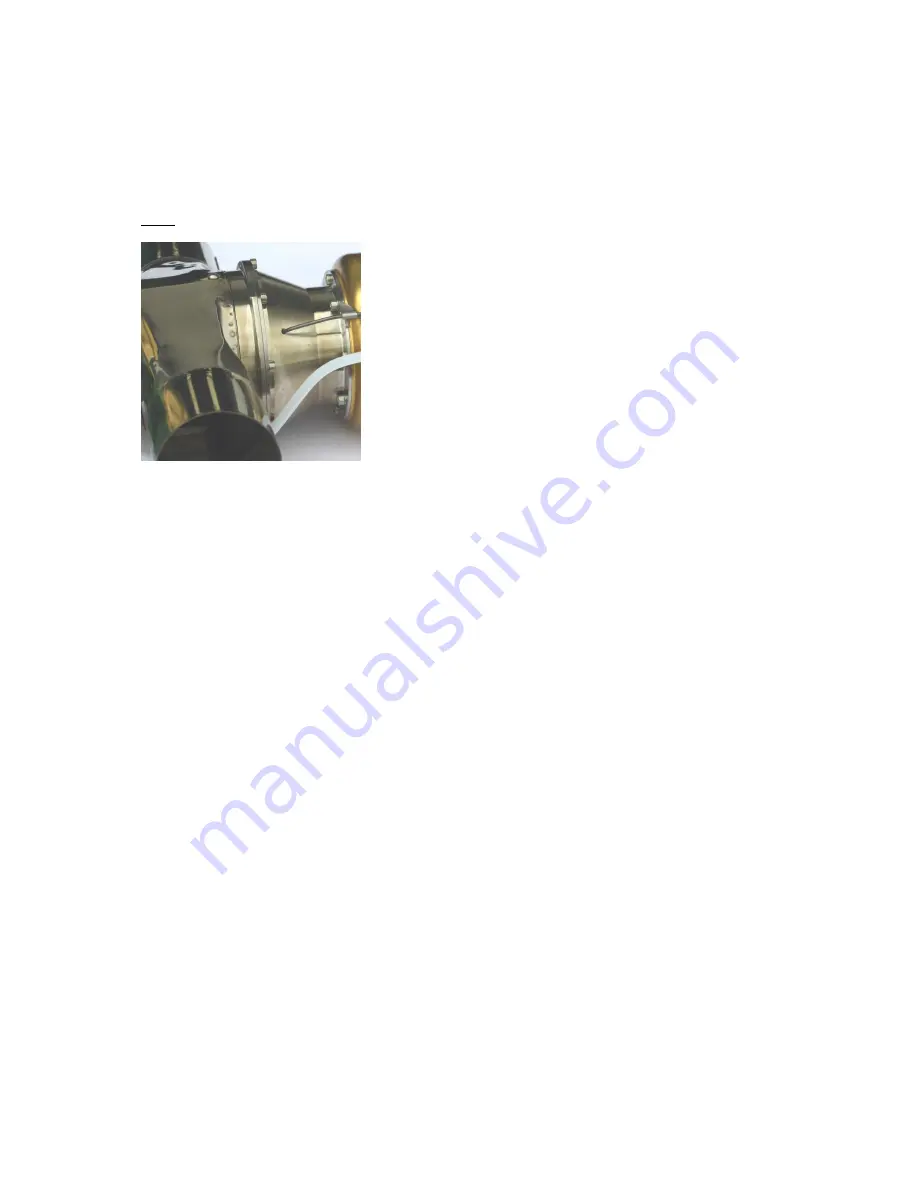
Wren 44 Gold Helicopter Owners Manual
Page 11
There are several kits for conversions to the popular helicopter airframes. Each has its own
method of securing the engine but all are simple and effective. Allowance for heat expansion
of the unit should be considered in the mounting.
The aim is to eliminate engine movement while attached firmly via the gearbox as this places
very high point loads on the hot section coupling point in the centre of the unit and at the
gearbox fixings. Note that 3D flying imposes extremely high forces onto the unit and these
must be controlled by a suitably rigid mount.
Heat issues?
The exposed metal components between the engine and
exhaust are called the
interstage
and will get very hot in
normal use. The standard fan and shroud supplied for i/c
engine use is ideal to help control this and will help to
prevent damaging buildup of heat in the immediate vicinity
of the helicopter airframe.
There is no possibility of keeping the unit cool to touch –
the gas flow internally will be at 400-500’C and releases
over 100kw energy per second but these components are
designed to withstand this heat without problems. Aim just
to stop other parts being affected by the heat. Bear in mind
too, these parts will retain heat for a considerable time after shutdown so please be
extremely careful with fingers in this area.
In normal running the gold part of the engine casing will only reach about 100-130'C
minimizing the chances of heat damage to the aircraft fuselage and as long as some airflow
can get in and around. No further stiffening is required or advised for the unit, this approach
enabling the conversion from I/C engine to turbo-shaft power to be accomplished with ease.
The mounting should support the engine at the approximate centre of gravity to withstand all
normal loads such as might be subjected to during flying maneuvers.
Aren't gas turbines more dangerous than I/C engines?
No. Turbine fuel has a high flashpoint which means at normal ambient temperatures it is
extremely difficult to ignite, unlike gasoline or glow fuel which is a low vapour temperature
and ignites easily. The 2nd stage fully encloses the outlet of the gas turbine section affording
a high degree of protection against any component failure due to accidental damage or
persistent operation beyond the normal operational duty cycle. The main issues of concern
are the requirement for a high degree of structural integrity with the helicopter framework
and mechanics, and need to operate the power unit within the capabilities of the helicopter
main components like main and tail rotors. As there is little control possible over the choice
of airframe the engine is fitted to it is important the user considers carefully the power
settings and choice of components used before running the unit.
What's it like to operate?
“Magic” – customer quote! The power unit itself is operated as a normal miniature gas
turbine and possesses all the standard qualities such as automatic push-button starting and
cooling, totally vibration free operation, very quiet running and exceptional power and of
course has the “right” noise and smell. The throttle response is of the best in its class - the
small gas generator rotor is small and light allowing very quick spooling to be achieved
safely. Being a very small gas turbine its fuel consumption has been described as "stingy" -
a typical 10minute flight being easily achieved with a single 1ltr fuel tank, depending on the
flying style.
How does it compare to I/C power?
The exceptional power to weight ratio which is close in performance levels to an 80cc