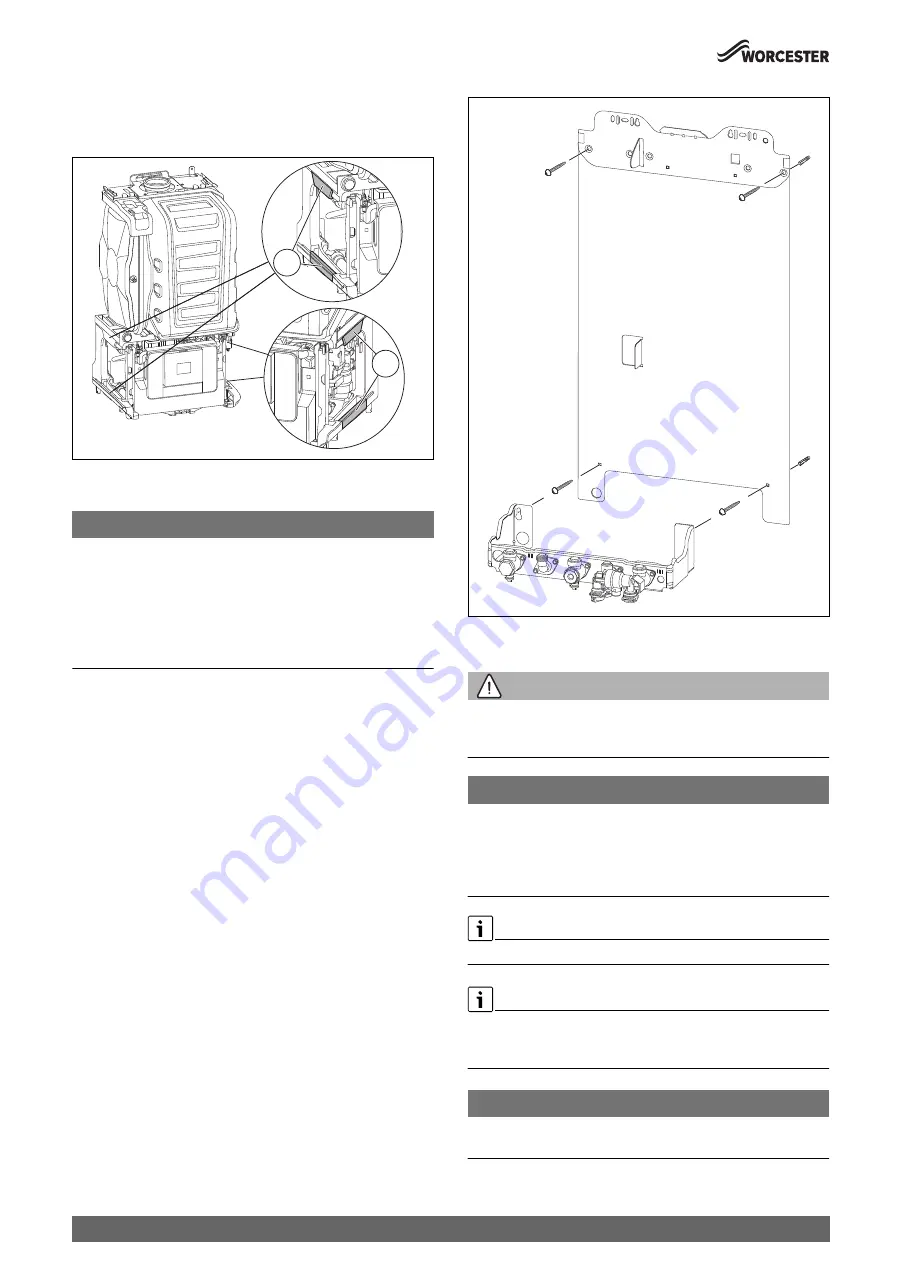
Installation
Greenstar 8000 Life – 6720883865 (2019/02)
30
Carry handles
For transportation of the appliance always use the carry handles [1] and
[2] (with the control unit in the closed position).
Fig. 38 Transport, lifting and handling
Preparing the appliance installation
NOTICE:
Incorrect mounting can cause material damage.
If the appliance is mounted incorrectly, it may fall off the wall.
▶ Only install the appliance on a rigid, solid wall. This wall must be able
to carry the weight of the appliance and must at least be as large as
the bearing surface of the appliance.
▶ Only use screws and wall plugs that are suitable for the wall type and
weight of the appliance.
▶ Remove the packaging, observing all notices in the packaging.
▶ Make sure that the gas type specified on the data plate is the same as
the gas type supplied.
▶ Make sure that the installation location is in the country of destination
specified on the data plate.
▶ Fasten the wall mounting plate to the wall using 4 screws and wall
plugs.
▶ Attach the pre-plumbing manifold to the lower screws and tighten.
Fig. 39 Fitting the wall mounting plate and pre-plumbing manifold
5.2
Appliance connections
WARNING:
Appliance gas connection
▶
Ensure the mains gas supply is isolated before starting any work
and follow all relevant safety precautions.
NOTICE:
Appliance hydraulic connections
▶ Ensure all water pipe work, to be connected, is isolated/drained and
observe all relevant safety precautions.
▶ Be aware of plastic components when using a naked flame on pipe
work.
Surplus water may be present inside the appliance due to factory testing.
External condensate pipe work or internal pipe runs in unheated areas
such as lofts, basements and garages exposed to prolonged cold
temperatures should be protected
chapter 4.5.
NOTICE:
Commissioning without water damages the appliance!
▶ Operate this appliance only when filled with water
0010023273-001
2
1
0010023431-001