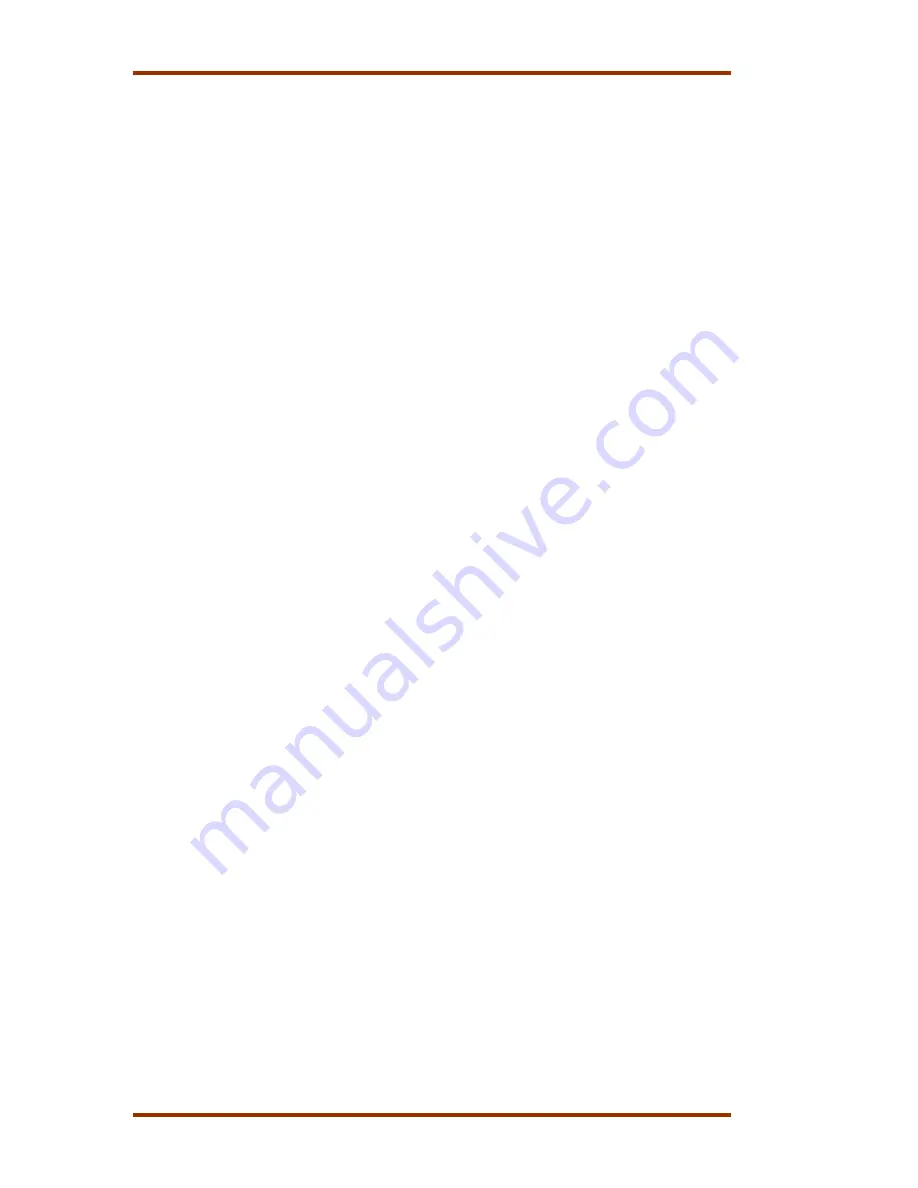
ProAct III/IV Actuator/Driver
Manual 04127
8
Woodward
A 25-turn potentiometer (Offset) adjusts the actuator position with a minimum
input signal from the speed control.
A 25-turn pot (Span) adjusts how far the actuator travels when the speed control
signal varies from minimum to maximum. This pot adjusts the maximum position
of the actuator. The Span adjustment range is approximately 40 degrees to 75
degrees.
The Span and Offset adjustments are interrelated. The adjustments may need to
be repeated until the desired actuator travel is achieved.
A one-turn pot (ACT. BANDWIDTH) adjusts how quickly the actuator responds to
a change in signal from the speed control (bandwidth 2–9 Hz).
4–20 mA Output Models
Units which provide a 4–20 mA output proportional to actuator position have two
additional 25-turn potentiometers (Position Span and Position Offset). These
potentiometers adjust the 4–20 mA output to correspond to minimum and
maximum positions of the actuator. The Position Offset adjusts the output at
minimum position to be 4 mA. The Position Span adjusts how much the output
changes with a given actuator position change and is used to adjust the
maximum output current. The adjustments are interrelated and may need to be
repeated until the desired output is achieved.
Actuator Position Signal
The feedback device is located on the closed shaft of the actuator. The device is
a rotary transducer which changes resistance proportional to the location of the
shaft. The device is a non-contacting unit, thereby eliminating most wear
problems. The feedback voltage is approximately 2 Vdc at 0° and 3 Vdc at 75°
(measured from 0 to –).
Actuator
The rotary design of the ProAct actuators gives 75 degrees of shaft rotation to
position fuel controls. The actuators apply torque in both directions. Torque is
proportional to the current supplied to the actuator by the driver.
The actuator uses sealed bearings, eliminating the need for maintenance. The
feedback mechanism attaches to the end of the rotor not being used to control
the engine. The device is enclosed in a Ryton housing and is sealed against the
elements. Avoid pressure washing the actuator.
An inertia disc is installed on the actuator output shaft. The disc is necessary for
stable actuator operation with light, low-friction linkages. Do not remove the disc
(see Figures 2-2 and 2-3).
Содержание ProAct III
Страница 6: ...ProAct III IV Actuator Driver Manual 04127 iv Woodward ...
Страница 10: ...ProAct III IV Actuator Driver Manual 04127 4 Woodward Figure 1 2 ProAct III Actuator Outline Drawing ...
Страница 11: ...Manual 04127 ProAct III IV Actuator Driver Woodward 5 Figure 1 3 ProAct IV Actuator Outline Drawing ...