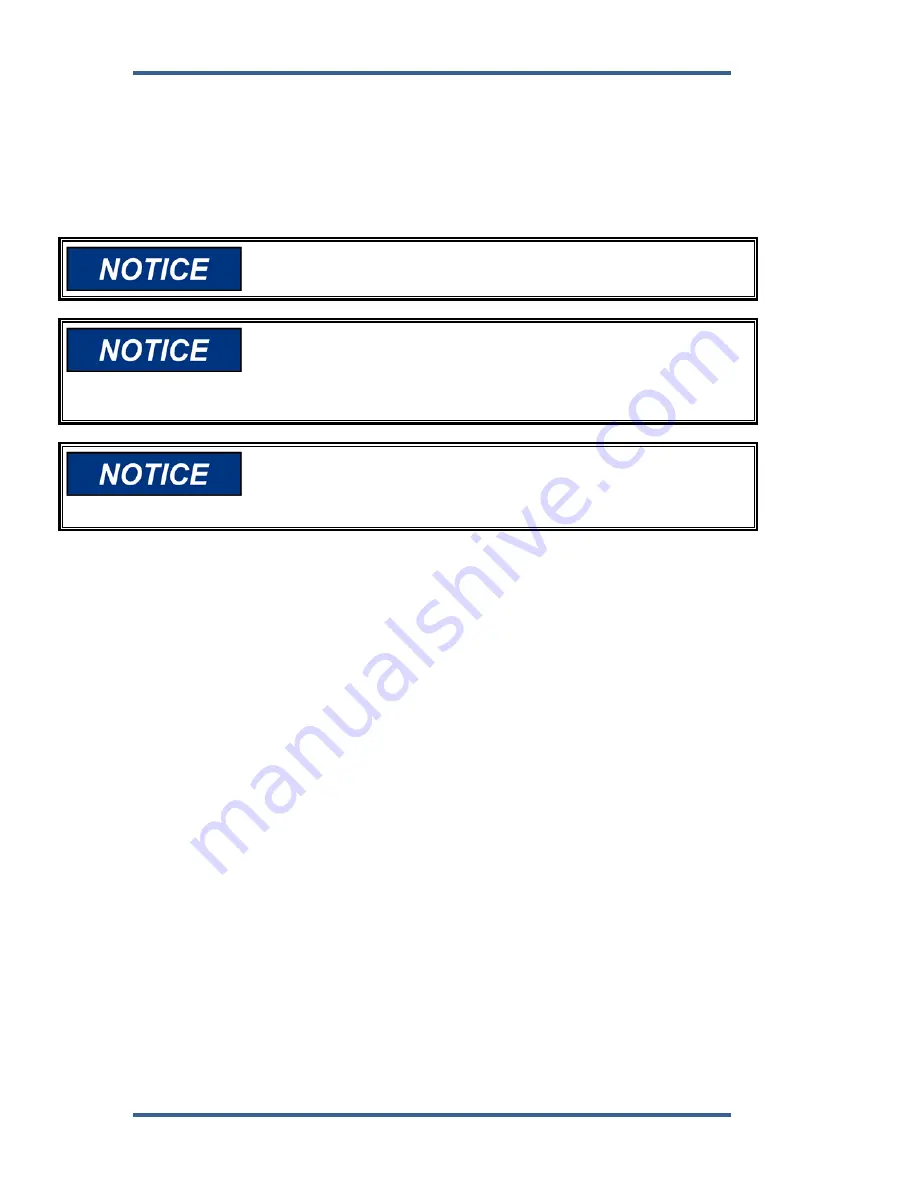
ProAct I/II
Manual 04121
26
Woodward
Run the power leads directly from the power source to the control. DO NOT
POWER OTHER DEVICES WITH LEADS COMMON TO THE CONTROL. Avoid
long wire lengths. Connect the positive (line) to terminal 24 and the negative
(common) to terminal 25. If the power source is a battery, be sure the system
includes an alternator or other battery-charging device.
DO NOT turn off control power as part of a normal shutdown procedure. Use the
Run/Stop discrete input (terminal 23) for normal shutdown.
Do NOT apply power to the control at this time. Applying power may
damage the control.
To prevent damage to the engine, apply power to the ProAct control
for at least ten seconds before starting the engine. The control must
have time to perform its power-up diagnostics and become
operational. Do not attempt to start the engine if the diagnostic tests
fail, because test failure turns off the output of the control.
To prevent possible damage to the control or poor control
performance resulting from ground loop problems, follow the
electrical connection instructions. The control common is electrically
isolated from the power supply input.
Actuator and Position Feedback Wiring
The ProAct actuator will rotate in either direction. In models I and II, the actuator
direction of rotation is selected by wiring in the actuator and the drift spring.
Connect the actuator wiring from the actuator to the ProAct control to terminals 1
(+) and 2 (–). Connect the actuator position feedback wires to terminals 7 (+), 8
(0), and 9 (–). Position feedback nominal voltages are approximately 3 V at
minimum actuator position and 2 V at maximum actuator position.
Discrete Inputs
Discrete inputs are the switch input commands to the ProAct Digital Speed
Control. The discrete inputs are usually powered by the positive power supply.
Isoch/Droop Contact
The Isoch/Droop contact (open for droop, closed for isochronous) connects to
terminal 16. When terminal 16 is open, the ProAct control will operate in droop at
the percentage entered in menu 3. When closed, the control will operate in
isochronous.
The percent of droop entered in Menu 3 is based on 75° of actuator rotation
between minimum and maximum positions. If the installation uses less than 75°,
the amount of droop must be increased proportionally.
Содержание ProAct I
Страница 10: ...ProAct I II Manual 04121 8 Woodward Figure 1 3 Example of ProAct II Actuator...
Страница 11: ...Manual 04121 ProAct I II Woodward 9 Figure 1 4 Outline Drawing of ProAct I or II Actuator...
Страница 12: ...ProAct I II Manual 04121 10 Woodward Figure 1 5 ProAct Wiring Diagram...
Страница 13: ...Manual 04121 ProAct I II Woodward 11 Figure 1 6 Outline Drawing of ProAct Control Box...
Страница 39: ...Manual 04121 ProAct I II Woodward 37 Figure 4 2 Typical Transient Response Curves...