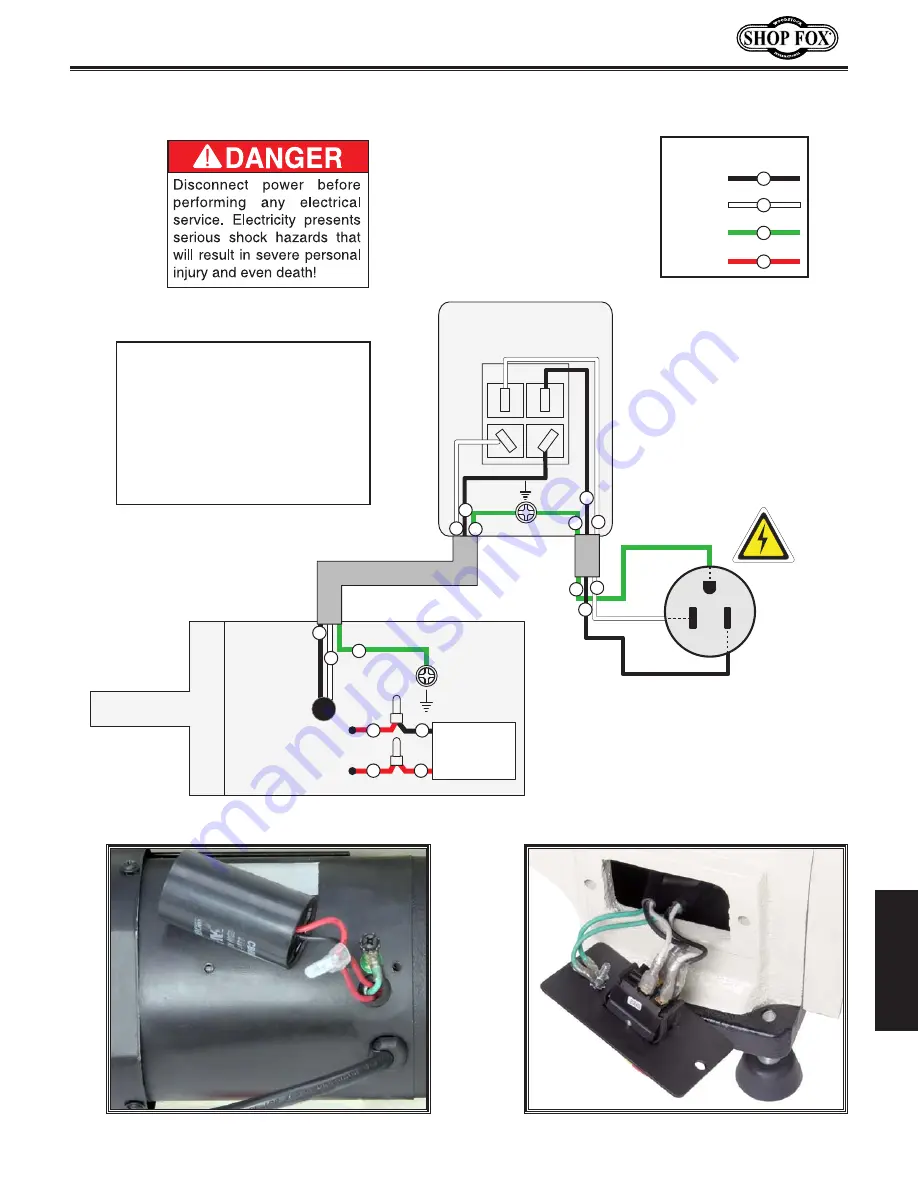
-29-
W1752 Owner's Manual (Mfg. 1/07+)
SE
RV
IC
E
Wiring Diagram W1752
5-15 Plug
White
Neutral
Black
Hot
Green
Ground
PADDLE SWITCH
(viewed from behind)
110
VAC
MOTOR
Ground
Run
Capacitor
25MFD
250VAC
Bk
Rd
Rd
Rd
BLACK
WHITE
GREEN
RED
COLOR KEY
Bk
Wt
Gn
Rd
Bk
Bk
Bk
Bk
Wt
Wt
Wt
Wt
Gn
Gn
Gn
Gn
Figure
27
. Motor connections.
Figure 28
. Switch connections.
NOTICE
This motor wiring diagram is
current at the time of printing;
however, always use the dia-
gram on the inside of the junc-
tion box cover when rewiring
your motor!
Содержание SHOP FOX W1752 s
Страница 35: ...Notes ...
Страница 36: ...Notes ...
Страница 37: ...W1752 Owner s Manual Mfg 1 07 ...