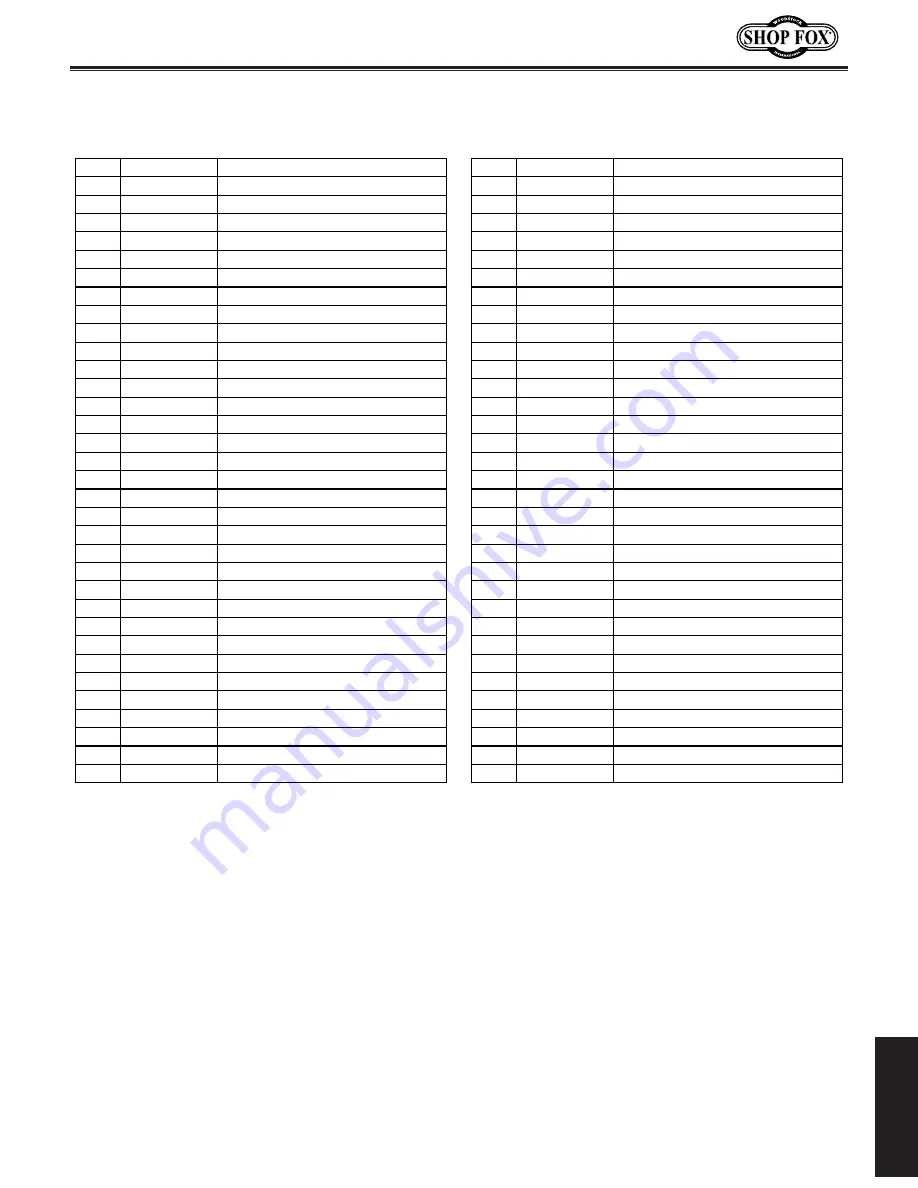
-51-
M1113 18" Wood/Metal Bandsaw
PA
RT
S
Table & Guides Parts List
REF PART�#
DESCRIPTION
REF PART�#
DESCRIPTION
101
XPB51
HEX
�
BOLT
�
1/4-20
�
X
�
3/8
136
XPS01
PHLP
�
HD
�
SCR
�
10-24
�
X
�
1/2
102
XPLW02
LOCK
�
WASHER
�
1/4
137
XPSB06
CAP
�
SCREW
�
1/4-20
�
X
�
1
103
XPW06
FLAT
�
WASHER
�
1/4
138
XM1113138
REAR
�
RAIL
104
XM1113104
GUIDE
�
BAR
�
COVER
139
XM1113139
TABLE
�
PIN
105
XPTS001
THUMB
�
SCREW
�
1/4-20
�
X
�
1/2
140
XM1113140
GAUGE
106
XM1113106
FENCE
�
SCALE
140-1 XM1113140-1 MITER
�
GAUGE
�
HANDLE
107
XM1113107
GUIDE
�
BAR
��
140-2 XM1113140-2 MITER
�
GAUGE
�
BODY
108
XM1113108
GUIDE
�
BAR
�
BRACKET
140-4 XM1113140-4 MITER
�
GAUGE
�
POINTER
109
XPW07
FLAT
�
WASHER
�
5/16
140-5 XM1113140-5 MITER
�
GAUGE
�
BAR
110
XPLW01
LOCK
�
WASHER
�
5/16
141
XM1113141
TABLE
�
INSERT
111
XPB32
HEX
�
BOLT
�
5/16-18
�
X
�
5/8
142
XM1113142
TABLE
�
(19MM
�
T-SLOT)
112
XM1113112
HANDWHEEL
�
SHAFT
143
XM1113143
GUIDE
�
BAR
�
SCALE
113
XM1113113
HANDWHEEL
144
XM1113144
POINTER
�
PLATE
114
XPSS11
SET
�
SCREW
�
1/4-20
�
X
�
1/4
146
XPB35
HEX
�
BOLT
�
3/8-16
�
X
�
2-1/2
115
XPR47M
EXT
�
RETAINING
�
RING
�
13MM
147
XM1113147
CLAMP
�
SHOE
116
XM1113116
BALL
148
XM1113148
TRUNNION
117
XM1113117
COMPRESSION
�
SPRING
149
XPB07
HEX
�
BOLT
�
5/16-18
�
X
�
3/4
119
XM1113119
GUIDE
�
BAR
�
KNOB
�
5/16-18
�
X
�
2
150
XPB58
HEX
�
BOLT
�
3/8-16
�
X
�
2
120
XM1113120
GEAR
151
XPW02
FLAT
�
WASHER
�
3/8
121
XM1113121
EXTENSION
�
TABLE
152
XM1113152
TABLE
�
BRACKET
122
XPW07
FLAT
�
WASHER
�
5/16
153
XM1113153
TABLE
�
TRUNNION
�
KNOB
�
3/8-16
123
XPB06
HEX
�
BOLT
�
5/16-18
�
X
�
2
154
XPS18
PHLP
�
HD
�
SCR
�
10-24
�
X
�
1/4
124
XM1113124
BLADE
�
COVER
155
XM1113155
TABLE
�
TILT
�
POINTER
125
XM1113125
LOCK
�
LEVER
�
1/4-20
�
X
�
3/4
156
XM1113156
TABLE
�
TILT
�
SCALE
126
XPSB05
CAP
�
SCREW
�
1/4-20
�
X
�
3/4
157
XM1113157
LOWER
�
SUPPORT
�
BRACKET
127
XM1113127
GUIDE
�
POST
�
BRACKET
158
XM1113158
BLADE
�
GUIDE
�
HOLDER
�
BOTTOM
128
XM1113128
SUPPORT
�
BEARING
�
SHAFT
159
XPB05
HEX
�
BOLT
�
1/4-20
�
X
�
3/4
129
P6200
BALL
�
BEARING
�
6200ZZ
160
XM1113160
RAIL
�
KNOB
�
5/16-18
�
X
�
5/8
130
XPR01M
EXT
�
RETAINING
�
RING
�
10MM
161
XPSN01
SQUARE
�
NUT
�
3/8-16
131
XM1113131
BLADE
�
GUIDE
�
BLOCK
162
XM1113162
FRONT
�
RAIL
132
XM1113132
BLADE
�
GUIDE
�
HOLDER
�
TOP
164
XPN02
HEX
�
NUT
�
5/16-18
133
XPSB06
CAP
�
SCREW
�
1/4-20
�
X
�
1
165
XPSB06
CAP
�
SCREW
�
1/4-20
�
X
�
1
134
XM1113134
GUIDE
�
POST
166
XM1113166
L-BRACKET
135
XM1113135
GUIDE
�
HEIGHT
�
POINTER
167
XM1113167
HANDWHEEL
�
HANDLE
Содержание SHOP FOX M1113
Страница 2: ......
Страница 5: ...3 M1113 18 Wood Metal Bandsaw INTRODUCTION...
Страница 6: ...4 M1113 18 Wood Metal Bandsaw INTRODUCTION...
Страница 47: ...45 M1113 18 Wood Metal Bandsaw SERVICE Wiring Diagram REWIRE...
Страница 50: ...48 M1113 18 Wood Metal Bandsaw PARTS PARTS Bandsaw Body Breakdown...
Страница 52: ...50 M1113 18 Wood Metal Bandsaw PARTS Table Guides Breakdown...
Страница 56: ...M1113 18 Wood Metal Bandsaw...
Страница 59: ......
Страница 60: ......