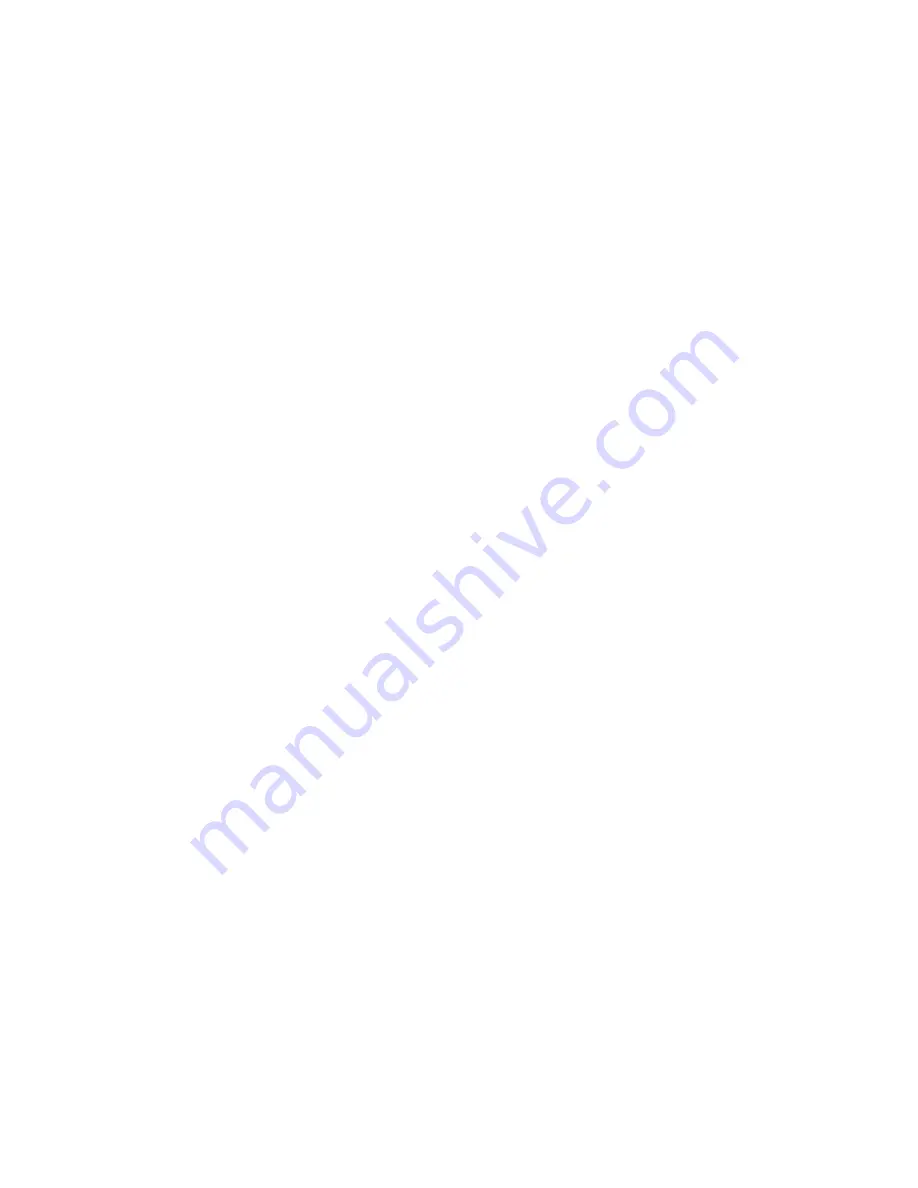
OPERATIONS
QTFSB 98351 04/25/03
3-9
TOWING OR PUSHING MACHINE
The machine my be slowly towed being careful to
attach towing chains to avoid damaging the
machine.
MACHINE JACKING
The machine may be jacked up for service or
inspection by using the specified jack locations.
Always block the tires when jacking up the machine.
The right front jack location is the base of the side
broom, just ahead of the right tire.
The left front jack location is the lower front frame
channel just ahead of the left front tire.
The rear jack location is the steel beam mount
located at the rear of the machine, centered under
the plastic bumper.
TO JACK UP MACHINE
1.
Empty and lower the hopper.
2.
Turn the key switch off and set the parking
brake.
FOR SAFETY:
Before leaving or servicing machine;
stop on level surface, set parking brake, turn off
machine and remove key.
3.
Block the tires that are not being raised to
prevent the machine from rolling.
FOR SAFETY:
When servicing machine, block
machine tires before raising machine.
4.
Use a jack of adequate capacity, raise the
machine using the designated jack locations.
FOR SAFETY:
When servicing machine, use hoist
or jack of adequate capacity, jack machine at
designated jack locations only. Block machine with
jack stands when raised.
5.
When the machine is raised, use jack at the
designated jack locations.
FOR SAFETY:
Block machine at designated jack
locations with jack stands when raised.
6.
Slowly lower the machine onto the jack stands.
7.
Be sure that the machine is secure.
8.
Service or inspect the machine as required.
9.
When finished working on the machine, raise
the machine off the jack stands.
10.
Remove the jack stands.
11.
Lower the machine to the floor. Remove the
blocks from the tires.
MACHINE TIE-DOWNS
There is a tie-down location at each corner of the
machine. The front attach points are the frame
cutouts located directly above each front tire. The
rear attach points are the right and left lower flange
of the frame channels, where they join the rear
bumper. An alternate single rear attach point is
around the pivot of the rear axle beam, located at
the center of the machine behind the rear jack point.
NOTE: When transporting the machine on a trailer
or in a truck, in addition to tie-downs, be sure to set
the machine parking brake, and block the tires to
prevent the machine from rolling.
Содержание TRACER FS
Страница 11: ...CONTROLS QTFSB 98351 05 17 03 3 3...
Страница 19: ...QTFSB 98351 04 25 03 3 11 THIS PAGE LEFT BLANK INTENTIONALLY...