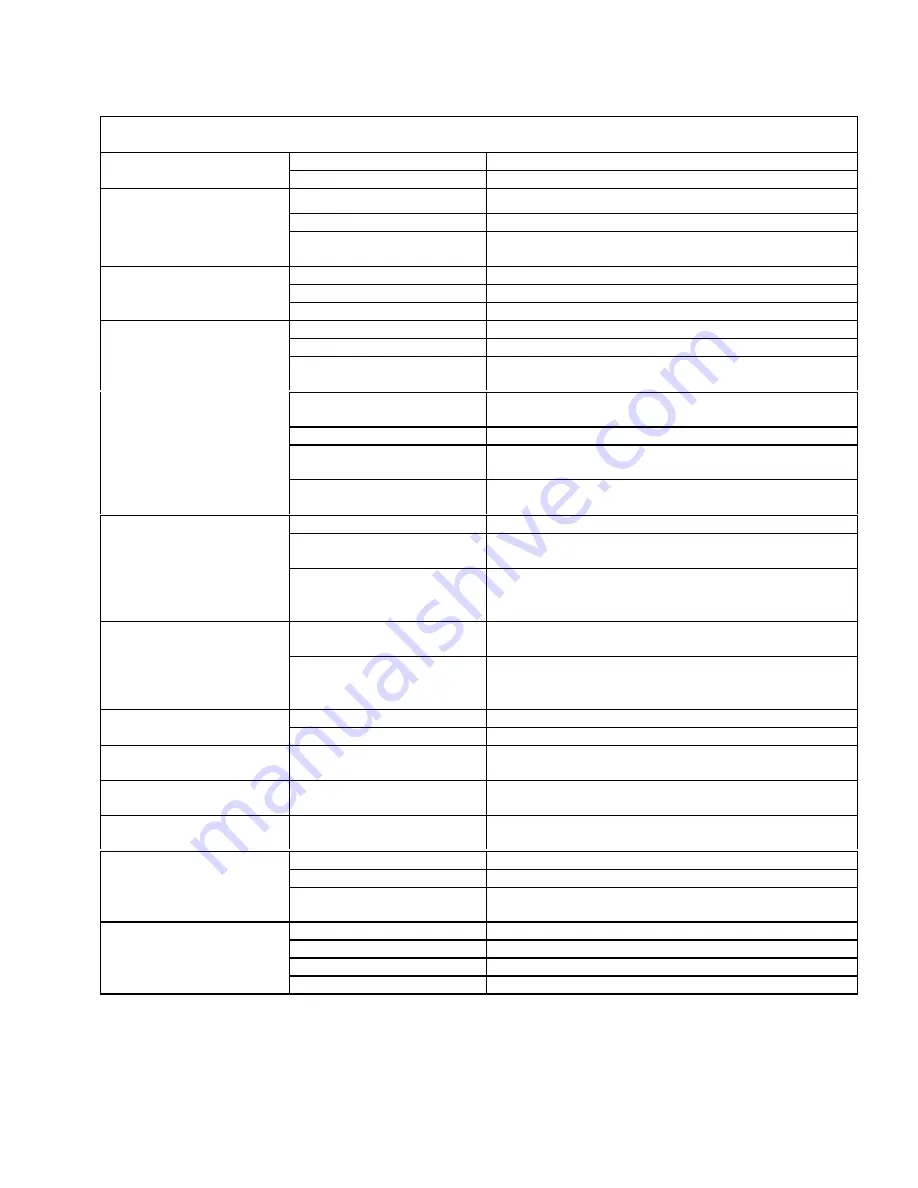
TROUBLESHOOTING
ENSIGN 98635 03/26/04
4-4
PROBLEM
CAUSE
SOLUTION
Dead electrical circuit
Check building circuit breaker or fuse box.
Loss of Power
Faulty power cord
Replace
Equipment not grounding
Follow grounding instructions exactly
Receptacle not grounded
Contact an electrician to check building’s wiring
Electrical shock
Internal wiring problem
Have a trained service technician check machine’s
wiring
Worn motor brushes
Replace
Motor worn out
Replace
Vac motor speed varies
or doesn’t run
Faulty switch
Replace
Loose vacuum dome
Center and seal dome over tank
Crack in dome of poor joint
Replace or repair using acrylic plastic cement only
Lint or dirt clogging
vacuum screen
With power off clean screen
Loose cuffs on vacuum
hose
Tighten cuffs turning counterclockwise
Vac motor seals leaking
Replace
Floor tool vac chamber
clogged
Wash out with hose. Pick lint out with a wire
Loss of vacuum
Vac motor, hose, or dome
gasket
Replace
Pump inlet screen plugged
Clean inlet screen
Pump air locked
Press trigger to open valve on cleaning wand to
relieve air
Pump runs no solution
Internal or external
solution line damaged and
leaking
Replace
Internal pump components
wearing out
Replace, see pump kit components (pg 4-3)
Pump runs, loss of
pressure
Check valves in pump
head for particles or cuts in
seals
Take piston from BPR and lubricate with Superlube.
If problem still exists change BPR kit
Unit not plugged in
Connect unit to 3 prong grounded outlet
Pump will not run
Loose wiring
See dealer
Solution hose fitting hard
to connect
Corrosion on fittings.
Clean with steel wool. Soak in acetic acid (white
vinegar). Lubricate lightly with silicone base lubricant.
Carpet not getting clean
Severe soil conditions
Make several passes at right angles to each other.
Use a pre-spray.
Carpet too wet
Over saturation
Adjust solution pressure to lower settings. Make
several passes without spray
Leaving carpet too wet
Check for loss of vac pressure
Too much chemical
Check label for correct solution concentration
Carpet browning
Light carpet with no brown
prevention
Go over carpet with browning prevent only
Solution hose connection
Check for positive connection
Faulty pump
Repair or replace
Faulty floor tool valve
Repair or replace
Solution not flowing
properly
Faulty pump switch
Repair
Содержание Ensign E50
Страница 10: ...CONTROLS ENSIGN 98635 04 04 03 3 2 1 Vacuum Switch 2 Pump Switch ON OFF OFF ON VAC PUMP 1 2 ...
Страница 16: ...PUMP GROUP ENSIGN 98635 04 04 03 5 1 1 2 3 5 6 7 8 2 3 4 ...
Страница 22: ...VACUUM MOTOR GROUP ENSIGN 98635 04 04 03 5 7 3 1 2 4 5 ...
Страница 24: ...WIRING DIAGRAM ENSIGN 98635 04 04 03 5 9 ...
Страница 26: ...NOTES ENSIGN 98635 04 04 03 5 11 ...