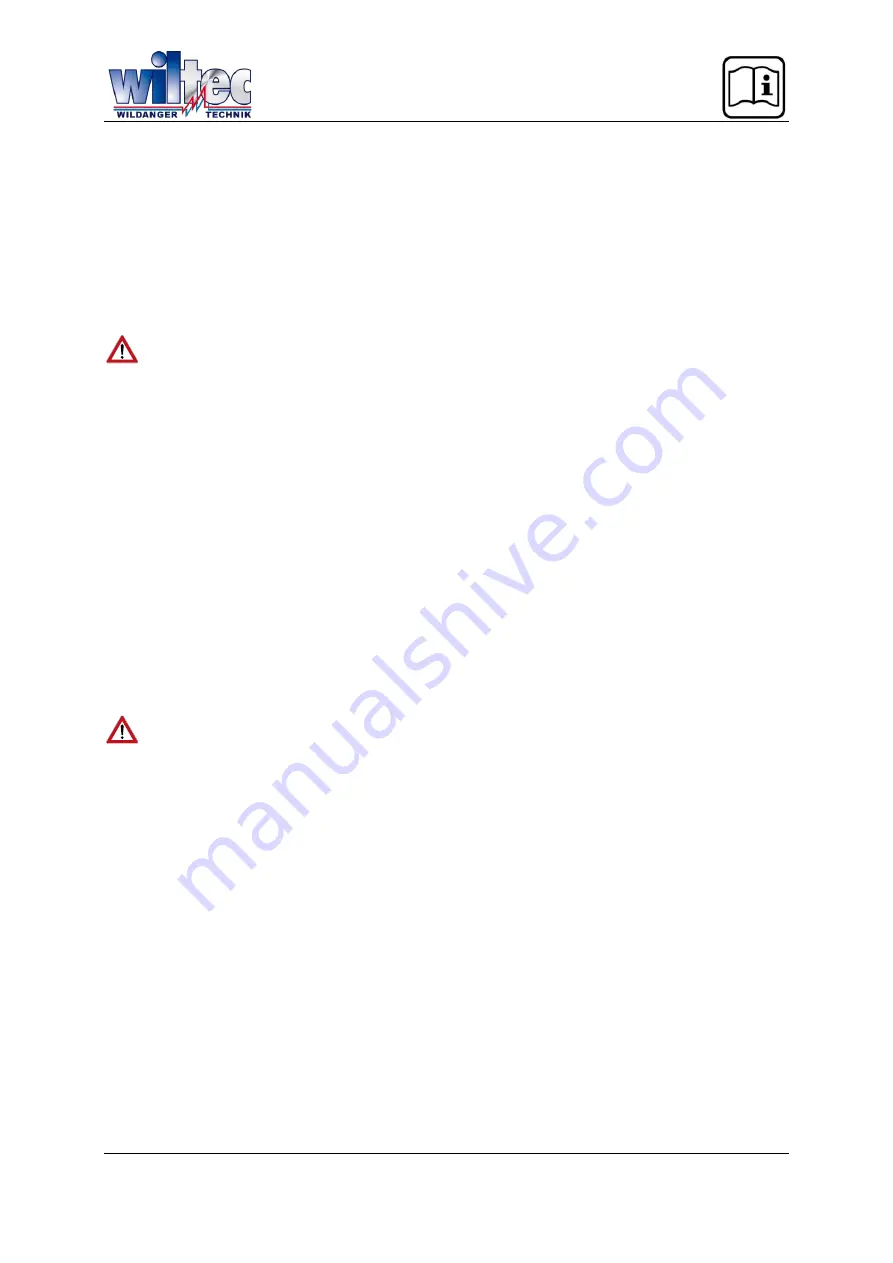
© by WilTec Wildanger Technik GmbH
Item 51552, 51553
Page 4
08 2021
-1
•
The user is responsible for the compliance with location specific safety and installing regula-
tions. Ask an electrician.
•
Consequential damage arising from flooded rooms caused by dysfunctions of the appliance
must be avoided by means of the appropriate measures (e.g., installing an alarm system, a
reserve pump).
•
In case of malfunction, the repair work can be carried out only by a qualified electrician or spe-
cialist.
•
The pump must not run dry or with the intake port completely closed. The manufacturer’s guar-
antee is no longer valid if the damage is caused by dry running.
•
The submersible pump must not be used for swimming pools.
•
The pump cannot be employed for potable water circuits.
WARNING:
Read all safety guidelines and instructions carefully.
Non-compliance with the safety rules and reg-
ulations can lead to an electric shock, fire and/ or serious injury. Keep the instructions and the safety
guidelines in a safe place in case you need them in the future.
Resistance
•
The maximum temperature of the pumped liquids should not 40
℃
during continuous
operation.
•
This pump is not allowed to be used for burnable and explosive liquids, as well as gas.
•
The transport of other liquids, especially engine fuels, cleaning detergents and other chemical
products is prohibited!
Installation
Installing the pump can be done the following way: either in a fixed position with fixed piping or in a fixed
position with flexible piping.
ATTENTION:
•
Please note that the pump may not be installed hanging of its pressure pipe or of its electricity
cable. The submersible pump engine must be hung up via its handle/ stand on its shaft floor. If
the water level is too low, the mud in the shaft can easily dry up and hinder the water flow.
Therefore, it is required to check the submersible pump engine frequently (by doing a start-up
test).
•
The float switch has been adjusted for immediate use.
Maintenance
•
Check the supply cable frequently; change them if necessary.
•
After 2000 hours of operating time, the pump should be maintained the following way:
◦
Demounting the pump
Check the parts easily worn, e.g., bearings, mechanical parts, oil seals, O-rings; exchange
the parts warn.
◦
Oil change
Open the oil exchange cap and pour mineral oil up to a height of 80 % of the shaft volume.
◦
Leak test
After the maintenance work the leak tightness needs to be checked up on with air pressure:
Fill the pump with 2 bar and watch the pressure gauge. If the air pressure does not drop
within 3 min, the pump is leak proof.