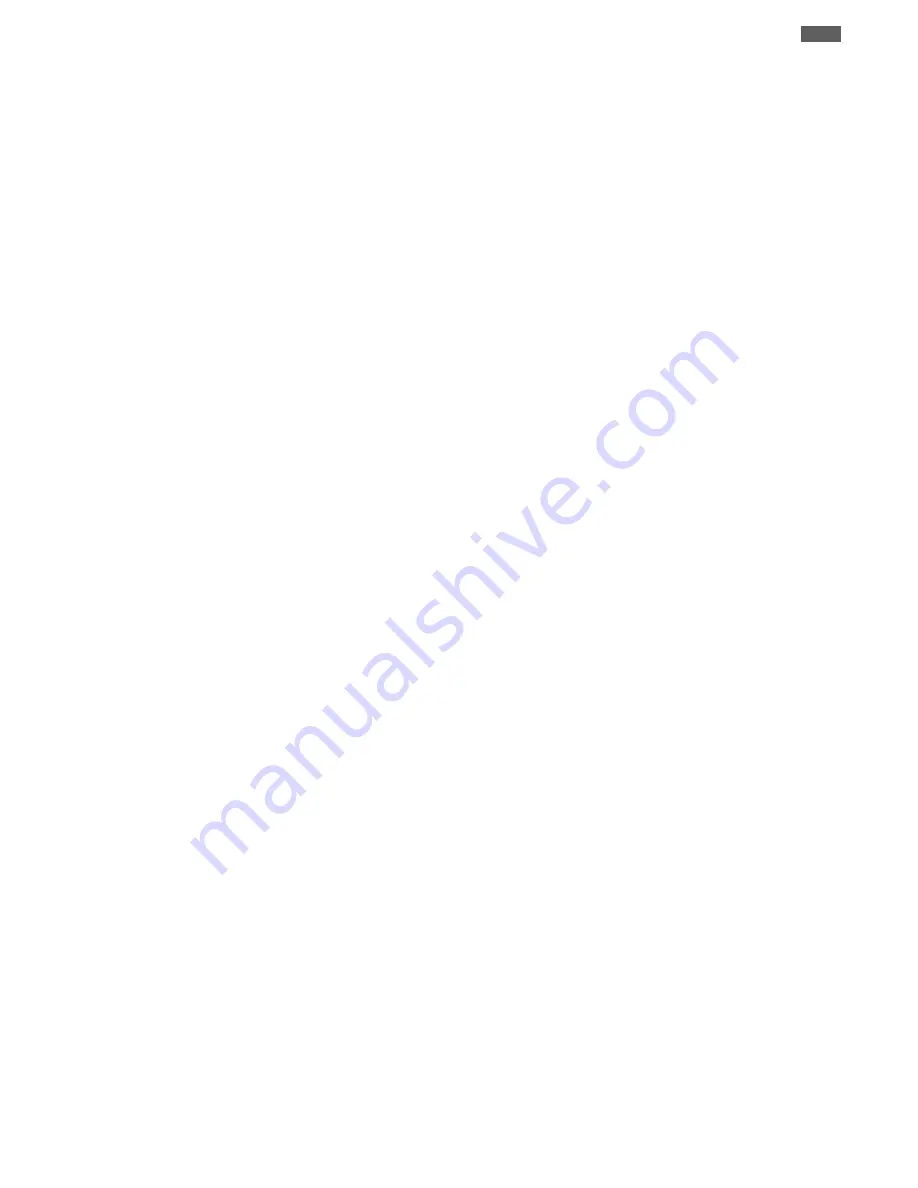
Application/use
en
Installation and operating instructions Wilo-EMU FA + FK 17.1, FK 202, FK 34, FK 42
9
▪ If the motor emerges during operation as well as in dry well installation, the motor
housing can reach temperatures in excess of 40 °C.
▪ Open all gate valves in the piping on the suction and pressure side.
▪ Ensure minimum water submersion through dry-running protection.
▪ Under normal operating conditions, the sound pressure level of the device is below
85 dB(A). However, the actual sound-pressure level depends on several factors:
– Installation depth
– Installation
– Fixation of accessories and pipe
– Duty point
– Immersion depth
▪ If the device is operated under normal operating conditions, the operator must measure
the sound pressure. Ear protection must be worn for sound pressure level of 85 dB(A)
and above and this must be noted in the work regulations!
2.9
Maintenance tasks
▪ Wear the following protective equipment:
– Closed safety goggles
– Safety shoes
– Safety gloves against cuts
▪ Always carry out maintenance tasks outside the operating space/installation site.
▪ Only carry out maintenance tasks mentioned in this installation and operating instruc-
tions.
▪ Only original parts from the manufacturer may be used for maintenance and repairs.
Use of parts other than the original parts releases the manufacturer from any liability.
▪ Collect any leakage of fluid and operating fluid immediately and dispose of it according
to the locally applicable guidelines.
▪ Store tools at the designated locations.
▪ After completing work, reattach all safety and monitoring devices and check that they
function properly.
Changing operating fluid
In case of a defect, a pressure
of several bar can build up
in the motor! This pressure
escapes when the screw plugs are
opened
. If screw plugs are opened without due cau-
tion, they can be ejected at high speed! To avoid injuries, observe the following instruc-
tions:
▪ Adhere to the prescribed sequence of work steps.
▪ Unscrew the screw plugs slowly, but never unscrew them completely. As soon as the
pressure escapes (audible whistling or hissing of air), stop turning the screw plug any
further.
WARNING! Hot operating fluid can also spray out when the pressure is escaping. This
can result in scalding! To avoid injuries, allow the motor to cool down to the ambient
temperature before carrying out any work!
▪ When the pressure has completely dissipated, fully unscrew the screw plug.
2.10
Operating fluid
Motor in the motor compartment and the sealing chamber is filled with white oil or a
water-glycol-mixture. Operating fluids must be replaced during regular maintenance
work and disposed off according to the local guidelines.
2.11
Operator responsibilities
▪ Installation and operating instructions must be in a language which the personnel can
understand.
▪ Make sure that the personnel is relevantly trained for the specified work.
▪ Provide the necessary protective equipment and make sure that the personnel wears it.
▪ Safety and information signs mounted on the device must be always legible.
▪ Train the personnel pertaining to the functioning of the system.
▪ Eliminate risk from electrical current.
▪ Equip hazardous components inside the system with an on-site guard.
▪ Identify and cordon off the work area.
▪ To ensure safe working practice, define the responsibilities of the employees.
Children and persons below 16 years or with reduced physical, sensory or mental capa-
cities or limited experience are prohibited from handling the device! A technician must
supervise persons below 18 years!
3
Application/use
3.1
Intended use
Submersible pumps are suitable for pumping:
▪ Sewage containing faeces (in accordance with EN 12050-1)