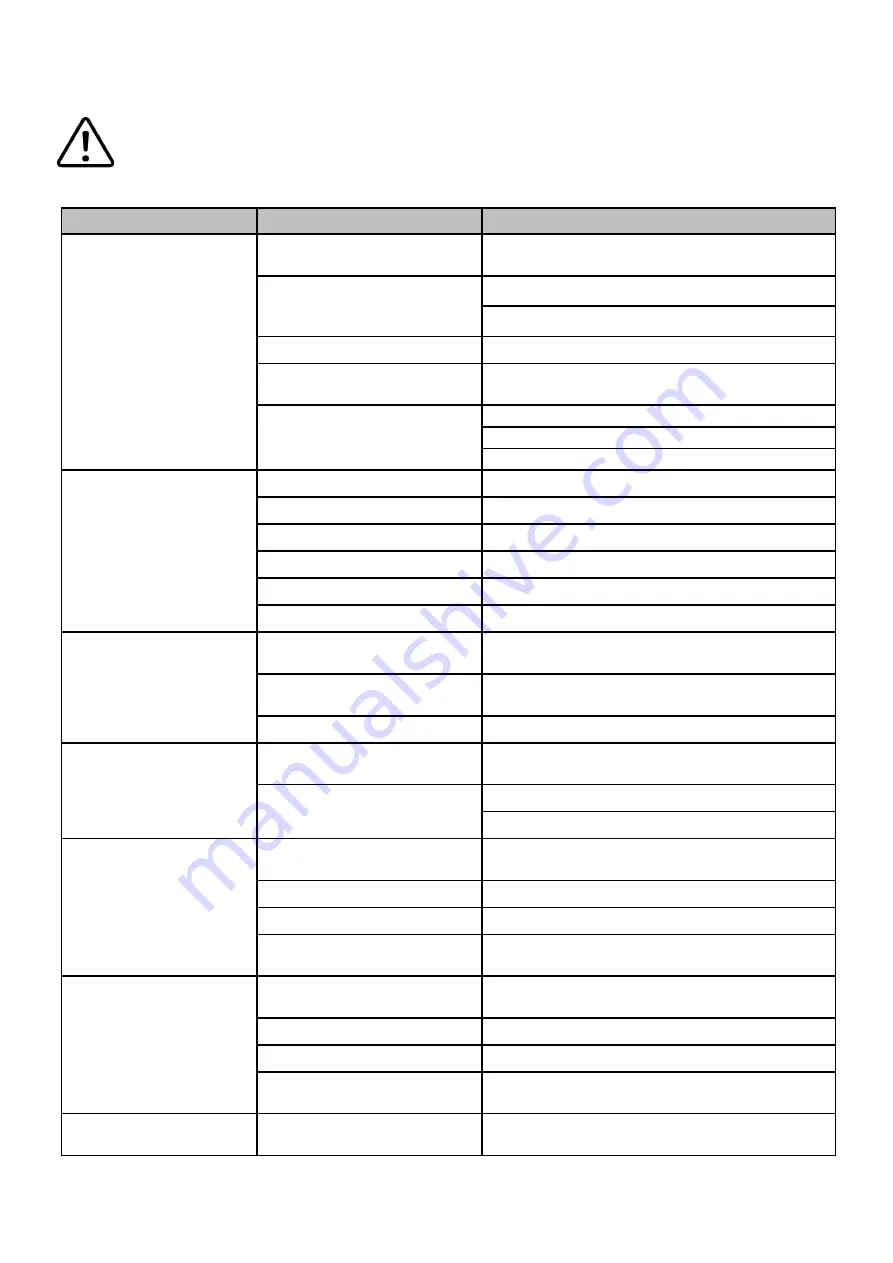
30
WELDING TROUBLESHOOTING
The following basic level of troubleshooting can be performed without special equipment or
knowledge and without removing the covers from the power source or the wire feed unit.
If further investigation work is required then please consult with a fully trained Technician.
Welding problem
Possible cause
Action
Excessive tungsten use
TIG set to DCEP
(DC Electrode Positive)
Connect TIG for DCEN (DC Electrode Negative)
Insufficient shield gas flow
Check for blockages and correct flow rate
Check for drafts
Electrode size to small
Select correct size
Electrode contamination
during cooling time
Extend post flow gas period
Electrode melting up into
shield cup when welding in AC
Balance control may be set too high in cleaning
Electrode type incorrect
Electrode size too small
Porosity/weld
contamination
Loose torch or hose fittings
Check and tighten all fittings
Inadequate shield gas flow
Adjust flow rate – normally 8-12L/m
Incorrect shield gas
Use correct shield gas
Gas hose damaged
Trace and replace damaged component
Base material contaminated
Clean material properly
Incorrect filler material
Check correct filler material grade in use
No operation when the
torch switch is operated
Torch switch faulty
Check the torch switch continuity and replace if
faulty
Mains fuse blown
Check circuit breakers or fuses and replace as
necessary
Fault inside the equipment
Have a technician check the equipment
Low or no output current
Weld circuit broken
Check all connections and cables continuity,
especially torch cables
No shield gas flowing
Check cylinder contents, regulators and valves
Could be a power source fault
Unstable arc when
welding in AC
Poor cleaning of base material
Check and adjust balance control where
necessary
Arc length incorrect
Arc length should be between 3-6mm
Material contaminated
Clean all base and filler materials
Frequency setting incorrect
Check and reset to a parameter where the
welding arc is stable
Unstable arc when
welding in DC
Tungsten electrode
contaminated
Break off contaminated end and regrind the
electrode
Arc length incorrect
Arc length should be between 3-6mm
Material contaminated
Clean all base and filler materials
Electrode connected to the
wrong polarity
Reconnect to correct polarity
Arc is difficult to start
Incorrect electrode type or
shield gas being used
Check that the correct electrode and gas is being
used (argon shield gas) also check for leaks
Содержание Jasic JT-500D
Страница 1: ......