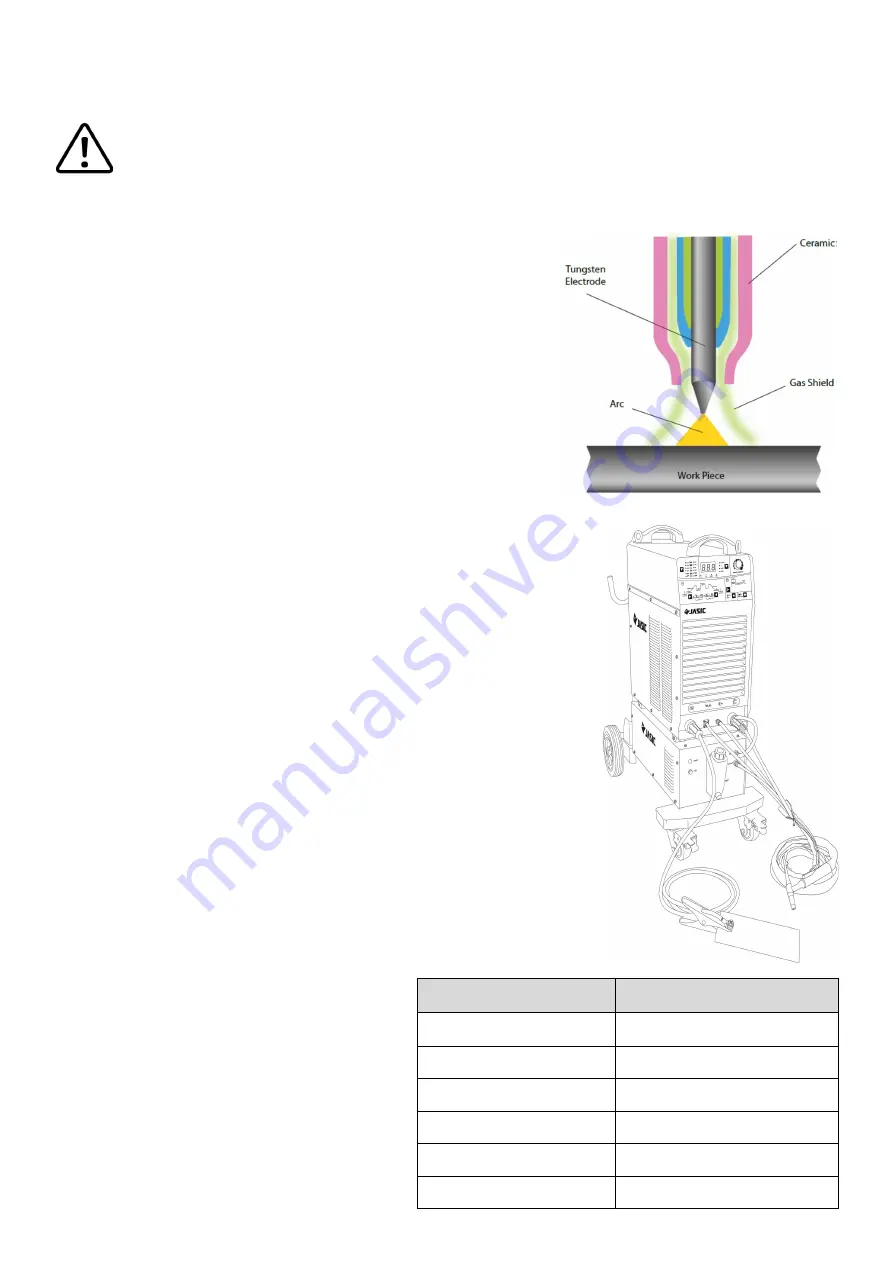
19
OPERATION
Before starting any welding activity ensure that you have suitable eye protection and
protective clothing. Also take the necessary steps to protect any persons within the welding
area.
TIG welding
Terms used: TIG – Tungsten Inert Gas, GTAW – Gas Tungsten Arc
Welding.
TIG welding is an arc welding process that uses a non-consumable
tungsten electrode to produce the heat for welding.
The weld area is protected from atmospheric contamination by a
shielding gas (usually an inert gas such as argon or helium) and a
filler rod matching the base material is normally used, though some
welds, known as autogenous welds, are carried out without the
need for filler wire.
TIG process can be either DC or AC modes:
DC - Direct current for welding steel, stainless steel, copper etc.
AC - Alternating current for welding aluminium and it’s alloys.
DC TIG welding
Connect the TIG torch leads as shown
Ensure that a suitable inert gas supply is connected
Switch the power switch on the back panel to “ON” the machine
is started with the power LED on and the fan working
Select TIG mode by switching to the welding mode selection key
to either TIG DC or TIG DC with pulse depending on your welding
application (see page 10)
Open the gas valve of the cylinder and adjust the gas regulator
and flow gas meter to obtain the desired flow rate. Press the
torch trigger briefly, the solenoid valve will operate and gas will
flow
Adjust the welding current according to the thickness of the work
piece to be welded (for a guide to welding parameters, please
refer to the table below)
Hold the torch 2-4mm away from the work piece and then press
the torch trigger. After arc is ignited, the HF discharge will cease,
the current will maintain the preset value and welding can be
carried out
After releasing the torch trigger, the welding
arc stops but gas continues flowing for the
post flow time and welding ends
Adjust the downslope time potentiometer
to change the time according to the welding
process requirements
This amperage guide for TIG welding tungsten
sizes shown can vary depending on material,
work piece thickness, welding position and joint
form.
Tungsten Size
DC – Electrode Negative
1.0mm
15 – 80A
1.6mm
70 – 150A
2.4mm
150 – 250A
3.2mm
250A – 400A
4.0mm
400A – 500A
6.0mm
750A – 1000A
Содержание Jasic JT-500D
Страница 1: ......