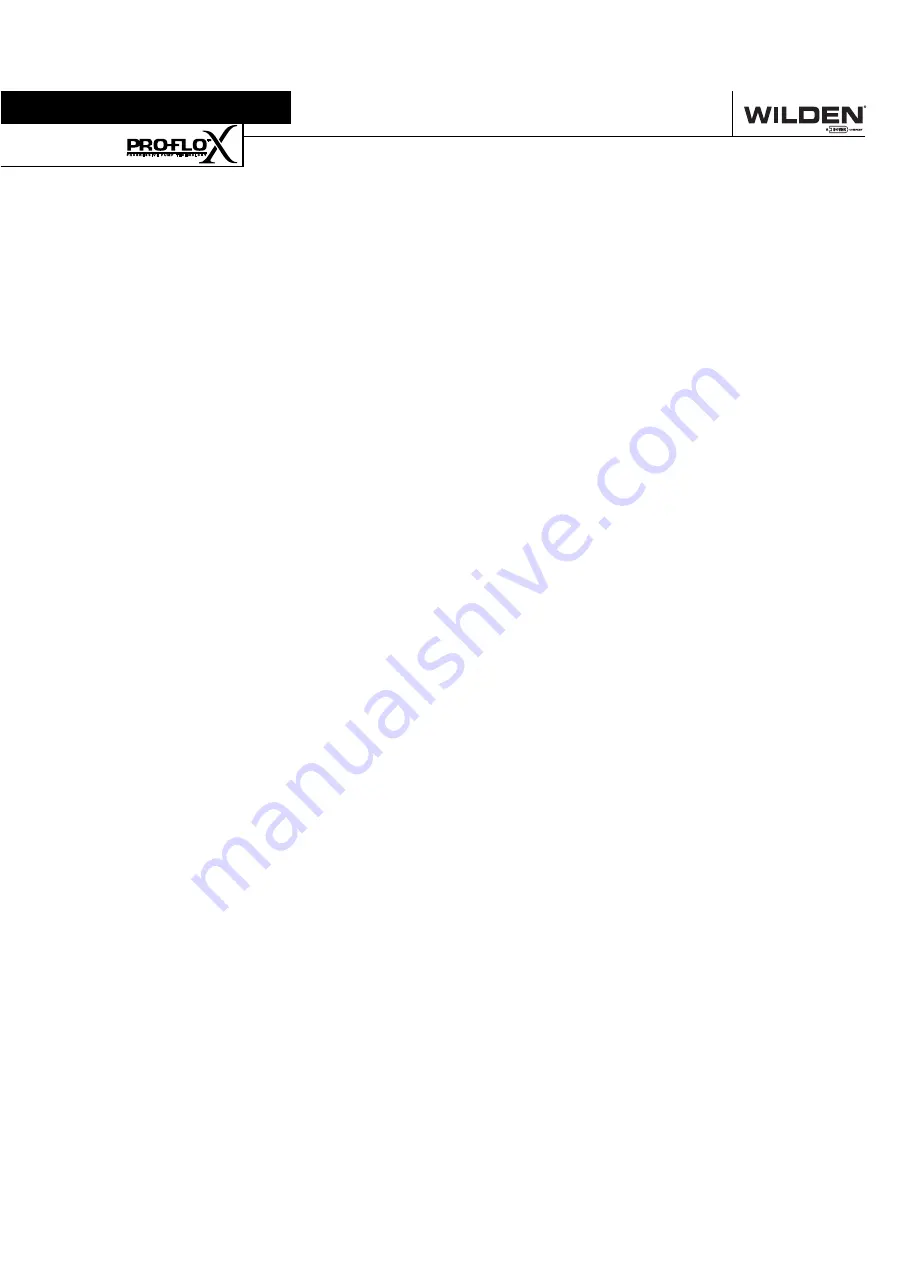
WIL-11111-E-03
13
WILDEN PUMP & ENGINEERING, LLC
S e c t i o n 6
S U G G E S T E D I N S T A L L A T I O N
Wilden pumps are designed to meet the performance requirements
of even the most demanding pumping applications. They have been
designed and manufactured to the highest standards and are avail-
able in a variety of liquid-path materials to meet your chemical-
resistance needs. Refer to the performance section of this manual for
an in-depth analysis of the performance characteristics of your pump.
Wilden offers the widest variety of elastomer options in the industry
to satisfy temperature, chemical-compatibility, abrasion-resistance
and flex concerns.
The suction-pipe size should be at least the equivalent or larger than
the diameter size of the suction inlet on your Wilden pump. The
suction hose must be non-collapsible, reinforced type as these pumps
are capable of pulling a high vacuum. Discharge piping should also
be the equivalent or larger than the diameter of the pump discharge
which will help reduce friction losses. It is critical that all fittings and
connections are airtight or a reduction or loss of pump suction capa-
bility will result.
INSTALLATION:
Months of careful planning, study, and selection
efforts can result in unsatisfactory pump performance if installation
details are left to chance.
Premature failure and long-term dissatisfaction can be avoided if
reasonable care is exercised throughout the installation process.
LOCATION:
Noise, safety and other logistical factors usually dictate
where equipment will be situated on the production floor. Multiple
installations with conflicting requirements can result in congestion of
utility areas, leaving few choices for additional pumps.
Within the framework of these and other existing conditions, every
pump should be located in such a way that the following key factors
are balanced against each other to maximum advantage.
ACCESS:
First of all, the pump’s location should be easily accessible. If
it’s easy to reach the pump, maintenance personnel will have an easier
time carrying out routine inspections and adjustments. Should major
repairs become necessary, ease of access can play a key role in speed-
ing the repair process and reducing total downtime.
AIR SUPPLY:
Every pump location should have an air line large
enough to supply the volume of air necessary to achieve the desired
pumping rate. Use air pressure up to a maximum of 8.6 bar (125 psig)
depending on pumping requirements.
For best results, the pumps should use a 5μ (micron) air filter, needle
valve and regulator. The use of an air filter before the pump will ensure
that the majority of any pipeline contaminants will be eliminated.
SOLENOID OPERATION:
When operation is controlled by a solenoid
valve in the air line, three-way valves should be used. This valve allows
trapped air between the valve and the pump to bleed off which
improves pump performance. Pumping volume can be estimated by
counting the number of strokes per minute and then multiplying the
figure by the displacement per stroke.
MUFFLER:
Sound levels are reduced below OSHA specifications using
the standard Wilden muffler. Other mufflers can be used to further
reduce sound levels, but they usually reduce pump performance.
ELEVATION:
Selecting a site that is well within the pump’s dynamic
lift capability will assure that loss-of-prime troubles will be eliminated.
In addition, pump efficiency can be adversely affected if proper atten-
tion is not given to site location.
PIPING:
Final determination of the pump site should not be made
until the piping challenges of each possible location have been evalu-
ated. The impact of current and future installations should be consid-
ered ahead of time to make sure that inadvertent restrictions are not
created for any remaining sites.
The best choice possible to locate the pump will be a site featuring
the shortest and straightest hook-up of suction and discharge piping.
Unnecessary elbows, bends, and fittings should be avoided. Pipe sizes
should be selected to keep friction losses within practical limits. All
piping should be supported independently of the pump. In addition,
the piping should be aligned to avoid placing stress on the pump
fittings.
Flexible hose or expansion joints can be installed to aid in absorbing
the forces created by the natural reciprocating action of the pump. If
the pump is to be bolted down to a solid location, a mounting pad
placed between the pump and the foundation will assist in minimiz-
ing pump vibration. Flexible connections between the pump and rigid
piping will also assist in minimizing pump vibration. If quick-closing
valves are installed at any point in the discharge system, or if pulsation
within a system becomes a problem, a surge suppressor (SD Equal-
izer®) should be installed to protect the pump, piping and gauges
from surges and water hammer.
If the pump is to be used in a self-priming application, make sure
that all connections are airtight and that the suction lift is within the
model’s ability.
NOTE:
Materials of construction and elastomer material have an effect
on suction-lift parameters. Please refer to the performance section for
specifics.
When pumps are installed in applications involving flooded suction or
suction head pressures, a gate valve should be installed in the suction
line to permit closing of the line for pump service.
Pumps in service with a positive suction head are most efficient
when inlet pressure is limited to 0.5 – 0.7 bar (7–10 psig). Premature
diaphragm failure may occur if positive suction is 0.7 bar (10 psig) and
higher.
BLOW OUT AIR LINE FOR 10 TO 20 SECONDS BEFORE ATTACHING TO
PUMP TO MAKE SURE ALL PIPE LINE DEBRIS IS CLEAR. ALWAYS USE AN
IN-LINE AIR FILTER.
PUMPS SHOULD BE THOROUGHLY FLUSHED WITH WATER BEFORE
INSTALLING INTO PROCESS LINES. FDA AND USDA PUMPS SHOULD
BE CLEANED AND/OR SANITIZED BEFORE USE ON EDIBLE PRODUCTS.
SUBMERSIBLE APPLICATIONS:
Pro-Flo X™ pumps can be used for
submersible applications, when using the Pro-Flo X™ submersible
option. Turbo-Flo™ pumps can also be used for submersible applica-
tions.
NOTE:
Pro-Flo® and Accu-Flo™ pumps are not submersible.
ALL WILDEN PUMPS ARE CAPABLE OF PASSING SOLIDS. A STRAINER
SHOULD BE USED ON THE PUMP INTAKE TO ENSURE THAT THE PUMP'S
RATED SOLIDS CAPACITY IS NOT EXCEEDED.
CAUTION:
DO NOT EXCEED 8.6 BAR (125 PSIG) AIR SUPPLY PRESSURE.
AIR-OPERATED PUMPS:
To stop the pump from operating in an
emergency situation, simply close the “shut off” valve (user supplied)
that is installed in the air-supply line. A properly functioning valve will
stop the air supply to the pump, therefore halting output. The shut-off
valve should be located far enough away from the pumping equip-
ment so that it can be reached safely in an emergency situation.
NOTE:
In the event of a power failure, the shut-off valve should be
closed if the restarting of the pump is not desired once power is
regained.
Содержание HX400S
Страница 25: ...N O T E S ...
Страница 30: ...N O T E S ...