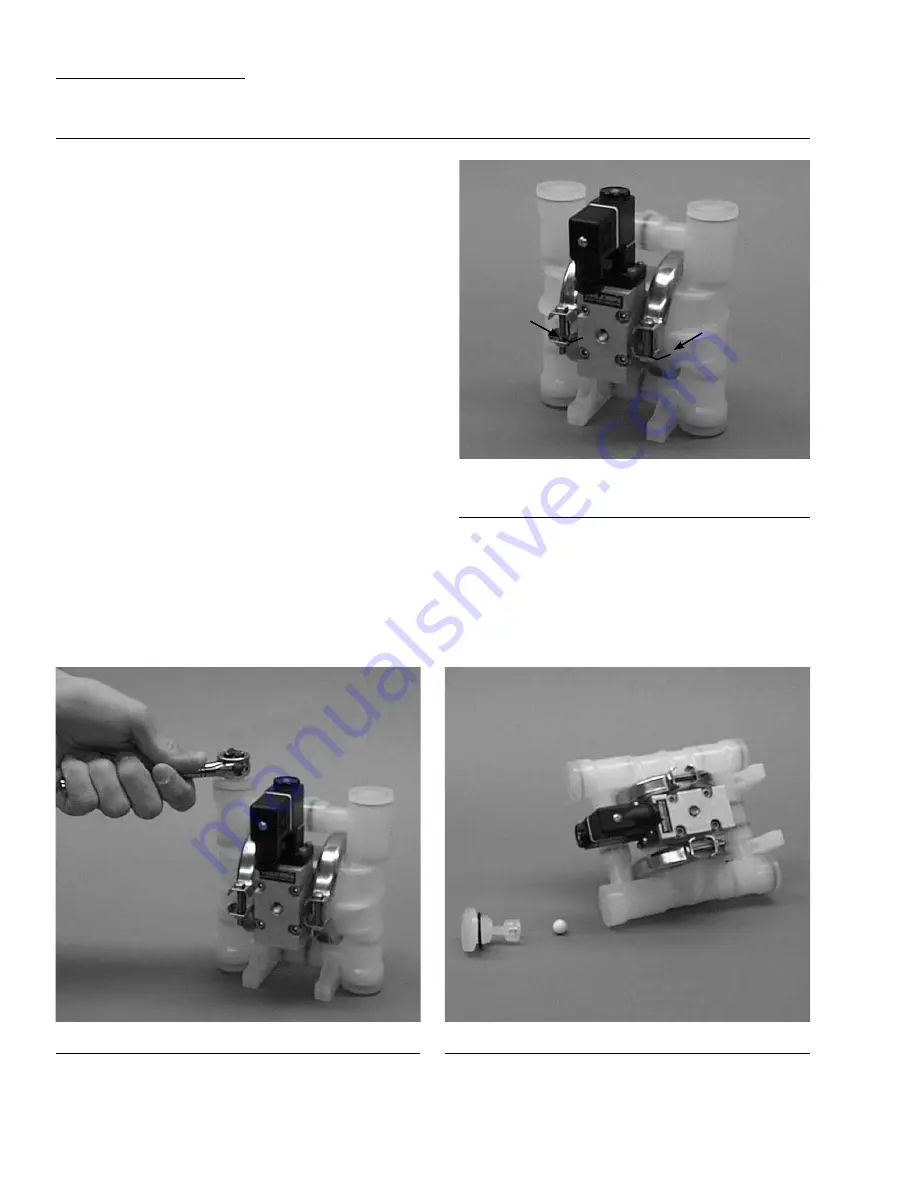
WILDEN PUMP & ENGINEERING CO.
12
WIL-10020-E-06
SECTION 8A
MODEL A.025
DIRECTIONS FOR DISASSEMBLY/REASSEMBLY
Step 2.
Figure 2
Using a 1/4" socket wrench, remove the top retainer.
Step 3.
Figure 3
Inspect the ball retainer, retainer o-ring, and valve ball. Check
for nicks, gouges, chemical attack or abrasive wear. Replace
worn parts with genuine Wilden parts for reliable perfor-
mance. Repeat Step 2 for remaining top retainer.
CAUTION:
Before any maintenance or repair is attempted, the
compressed air line to the pump should be disconnected and
all air pressure allowed to bleed from the pump. Disconnect
all intake, discharge, and air lines. Drain the pump by turning
it upside down and allowing any fluid to flow into a suitable
container. Be aware of any hazardous effects of contact with
your process fluid.
The Wilden model A.025 is an air-operated, double-diaphragm
pump with all wetted parts of polypropylene or PVDF. The
single-piece center section, consisting of center block and air
chambers, is molded from polypropylene. All fasteners and
hardware are stainless steel. All o-rings used in the pump are
of special materials and should only be replaced with factory-
supplied parts.
PLEASE read all directions before starting disassembly.
TOOLS REQUIRED:
1/4" Socket Drive
3/8" Box Wrench
7/16" Wrench
3/16" Rod
Adjustable Wrench
Vise equipped with soft jaws (such as plywood, plastic
or other suitable material)
NOTE:
The model used for these instructions incorporates PTFE
diaphragms and balls. Models with rubber/TPE diaphragms are
the same except where noted.
Figure 1
DISASSEMBLY:
Step 1.
Before actual disassembly is started, turn pump upside
down and drain all liquid trapped in the pump into a suit-
able container. Be sure to use proper caution if liquid is
corrosive or toxic. Mark each liquid chamber to its respec-
tive air chamber for easy alignment during reassembly.