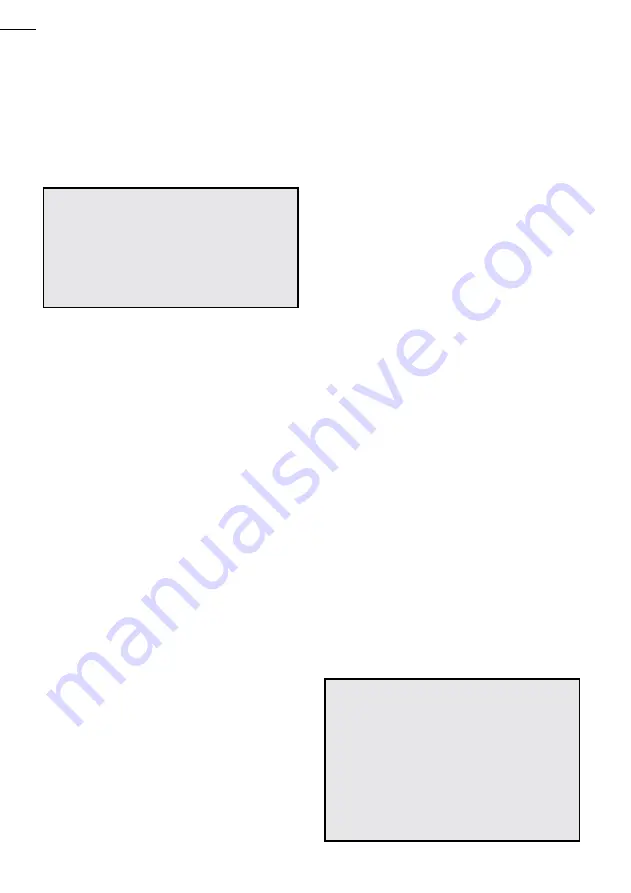
13
12
Wirefeeder W67 | Operator Manual | Model No W67-40
Refer to the Weldmatic power source
Operators Manual for gas and weld setting
and gun position information.
6 BASIC WELDING INFORMATION
Dust
Care should be taken to prevent excessive
build-up of dust and dirt within the welding
power source. It is recommended that
at regular intervals, according to the
prevailing conditions, the equipment
covers be removed and any accumulated
dust be removed by the use of a dry, low
pressure compressed air, or a vacuum
cleaner. The machine should be blown
out with compressed air at least every 12
months as grinding dust can settle on PCB
componentry causing failure. Failure to
maintain machines may void warranty.
Wirefeed
In order to obtain the most satisfactory
welding results from the G.M.A.W. process,
the wirefeed must be smooth and constant.
Most causes of erratic wirefeed can be
cured by basic maintenance. Check that the:
1 Feed rolls are the correct size and type
for the wire in use. Check also that the
drive groove is aligned with the wire and
that the groove is not worn;
2 Gun cable liner is clear of dust and swarf
build-up. When replacement becomes
necessary, fit only the correct liner (see
page 20). The build-up of dust can be
minimised by regular purging of the liner
7 GENERAL MAINTENANCE
8 EXTERNAL TROUBLE SHOOTING
with dry compressed air. This may be
conveniently done each time the wire
spool is replaced;
3 Welding tip is free of obstructions such
as spatter build-up. Ream out the tip
bore with a suitable size oxy-tip cleaner.
Replace the welding tip as it becomes
worn;
4 Feed roll pressure is not excessive. The
pressure should be just sufficient to
feed the wire evenly. Excessive pressure
will deform the electrode wire and make
feeding more difficult;
5 Consumable wire spool holder rotates
smoothly and that the braking action is
not excessive. The spool should only
have sufficient braking to prevent over
run when the motor stops. This also may
be conveniently checked each time the
wire is replenished;
7 Welding wire is straight and free of
buckles or ‘waviness’. To check, remove
2 or 3 metres of wire from the spool.
Clamp one end in a vice or similar,
then holding the other end pull the wire
out straight. Look down the length of
the wire, any buckles will be obvious.
Buckled wire is extremely difficult to
feed reliably and should be replaced;
8 Welding wire is free of surface rust.
Replace if rust is evident.
Before removing the equipment
cover, ENSURE that the equipment
is disconnected from the mains
power supply. When the equipment
is energised LETHAL VOLTAGES are
present.
Refer to the Weldmatic power
source Operators Manual for
trouble shooting tips. If these
checks do not identify the fault
condition, the equipment should be
returned to a WIA Service agent.
Phone 1300 300 884 for details of
your nearest service agent.
Содержание W67-1
Страница 1: ...Wirefeeder WELDING COM AU OPERATORS MANUAL W67 1 From serial numbers W67A...
Страница 15: ...15 Fig 3 Wirefeeder Assemble and Parts List 11 1 ASSEMBLY AND PARTS LIST W67 WIREFEEDER...
Страница 26: ...26 Wirefeeder W67 Operator Manual Model No W67 40 NOTES...
Страница 27: ...27 NOTES...