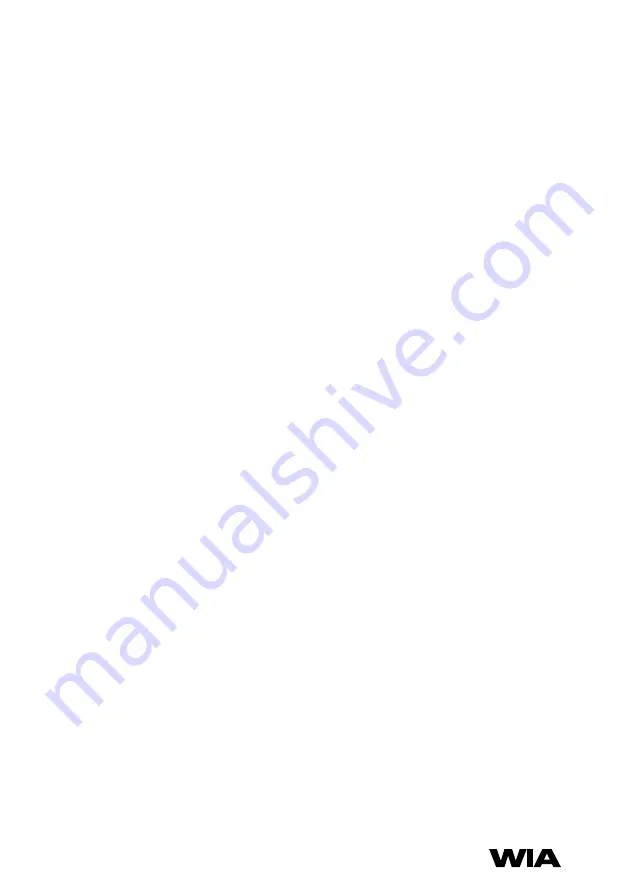
7
6
1 INTRODUCTION
Gas Metal Arc Welding (G.M.A.W.) is an
arc welding process where a consumable
wire is fed by motor driven feed rolls to a
welding gun, and where welding current is
supplied from the welding power source.
The welding arc is struck between the work
piece and the end of the wire, which melts
into the weld pool. The arc and the weld
pool are both shielded by gas flow from the
gun, or in the case of “self shielded” wires,
by gases generated by the wire core.
The process is very versatile in that by
selection of the correct wire composition,
diameter and shielding gas, it can be used
for applications ranging from sheet-metal
to heavy plate, and metals ranging from
carbon steel to aluminium alloys.
The Weldmatic Fabricator has been
designed to be used with consumable
wires in the range from 0.6mm to 1.6mm
diameter. The smaller wire sizes are used
when welding at lower currents, such as
sheet-metal applications. Increasing the
wire diameter permits higher welding
currents to be selected.
A common application of G.M.A.W. is for
welding Mild Steel. In this application, a
Mild Steel solid consumable wire such as
AUSTMIG ES6 is used with a shielding gas
of Carbon Dioxide, or Argon mixed with
Carbon Dioxide. Alternatively, Flux-cored
consumable wires are available in both gas
shielded, and ‘gasless’ self shielding types.
Stainless steel and Aluminium can be
welded with G.M.A.W. using the correct
consumable wire and shielding gas.
2 RECEIVING
Check the equipment received against
the shipping invoice to make sure the
shipment is complete and undamaged. If
any damage has occurred in transit, please
immediately notify your supplier.
The Weldmatic 356 package contains;
– Weldmatic 356 Power Source
CP147-2
– W64-1 Wire Feeder with 10m
interconnection cable. 35mm
2
weld
cable.
– 10m Work Lead with Clamp
– Welding Torch 300 A 3.6m with Centre
Fire Consumables.
– Gas Regulator
– Gas Hose
– (This) Operating Manual
The Weldmatic 396 package contains;
– Weldmatic 396 Power Source
CP148-2
– W64-1 Wire Feeder with 10m
interconnection cable. 50mm
2
weld
cable.
– 10m Work Lead with Heavy Duty G
Clamp
– Welding Torch 300 A 3.6m with Centre
Fire Consumables.
– Gas Regulator
– Gas Hose
– (This) Operating Manual