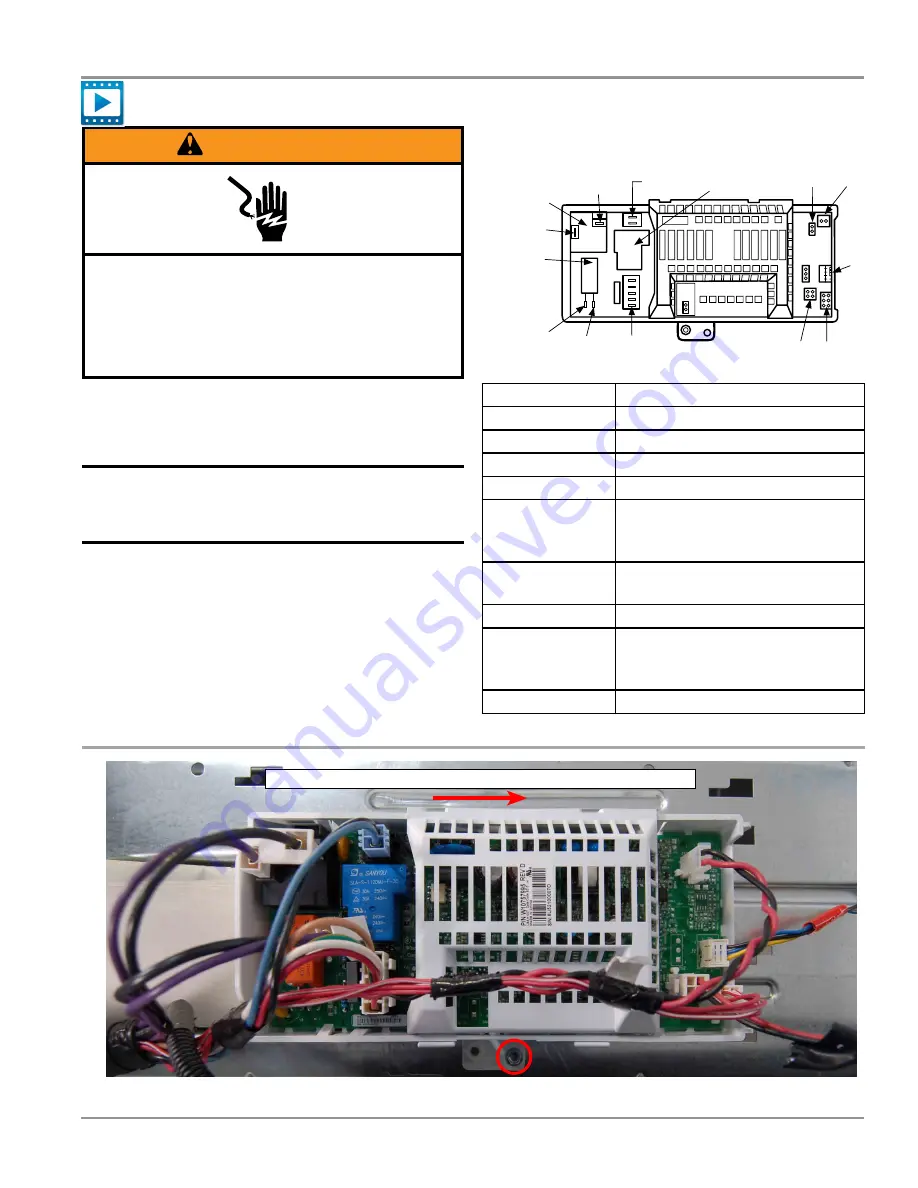
COMPONENT ACCESS
Whirlpool & Maytag 9.2 Cu. Ft. Steam Dryer
n
4-5
Removing the Appliance Control Unit (ACU)
To Remove the Appliance Control Unit (ACU)
IMPORTANT: Electrostatic Discharge (ESD) Sensitive Device.
Failure to follow the ESD precautions outlined at the
beginning of Section 3 “Testing” may destroy, damage, or
weaken the main control assembly.
1.
Unplug dryer or disconnect power.
2.
Perform the procedures on page 4-3, “Removing the Top
Panel” prior to performing the following steps.
3.
Disconnect all connectors from the ACU (see Figure 1).
4.
Using a 1/4” nut driver, remove the one (1) hex-head
screw securing the ACU to the control bracket (location
circled in Figure 2).
5.
Reach under control bracket and locate release tab.
Depress tab and slide ACU towards front of dryer to
disengage from bracket. Remove Appliance Control Unit.
WARNING
Electrical Shock Hazard
Disconnect power before servicing.
Failure to do so can result in death or
electrical shock.
Replace all parts and panels before operating.
Connector
Component(s)
Heater Relay #1
Gas & Electric Heaters
Heater Relay #2
Electric Heater Only
J2
User Interface
J6
Drum LED
J8
Water Valve
Door Switch
Neutral & GND
J9
L1
Motor
J13
Moisture Sensor
J14
Inlet Thermistor
Outlet Thermistor
Model (Gas)
J23
Rear Moisture Sensor (some models)
Appliance Control Unit (Figure 1)
3$*(
FOR SERVICE TECHNICIAN’S USE ONLY
DO NOT REMOVE OR DESTROY
Figure 2 - ACU Connectors & Pinouts
J2 – WIDE TO UI (+5 VDC)
J2-1 BLK +5VDC
J2-2 BLU DATA
J2-3 YEL 5V GND
J8 – WATER VALVE/DOOR SWITCH
J8-5
OPEN
J8-4 TAN DOOR SWITCH
J8-3 WHT NEUTRAL
J8-2 G/Y CHASSIS GND
J8-1 RED WATER VALVE
(ON SOME MODELS)
J6 – DRUM LED
J6-1 RED
J6-2 BLK
J6-3
J6-4
J9 – MOTOR/L1
J9-2 BLK L1
J9-1 LT BLU MOTOR
J13 – MOISTURE SENSOR
J13-1 BLK MOISTURE SENSOR
J13-2 RED MOISTURE SENSOR
J14 – THERMISTORS
J14-1 RED INLET THERMISTOR
J14-2 RED INLET THERMISTOR
J14-3 R/W OUTLET THERMISTOR
J14-4 BLK MODEL (GAS)
J14-5 BLK MODEL RTN (GAS)
J14-6 R/W OUTLET THERMISTOR
J13
J2
J9
J14
J8
K3
K2
K1
Heater Relay #1
(Gas & Elect.)
L1 – BLK
Heater (E) – VLT
Heater (G) – RED
Heater Relay #2
(Elect. Only)
L1 – BLK
Heater – VLT
Motor Relay
J6
J23
(on some
models)
J23 – REAR MOISTURE SENSOR
(on some models)
J23-1 Y/R
MOISTURE SENSOR
J23-2 YEL
MOISTURE SENSOR
Figure 2 - Appliance Control Board
Depress tab under bracket and then slide ACU towards front of dryer.