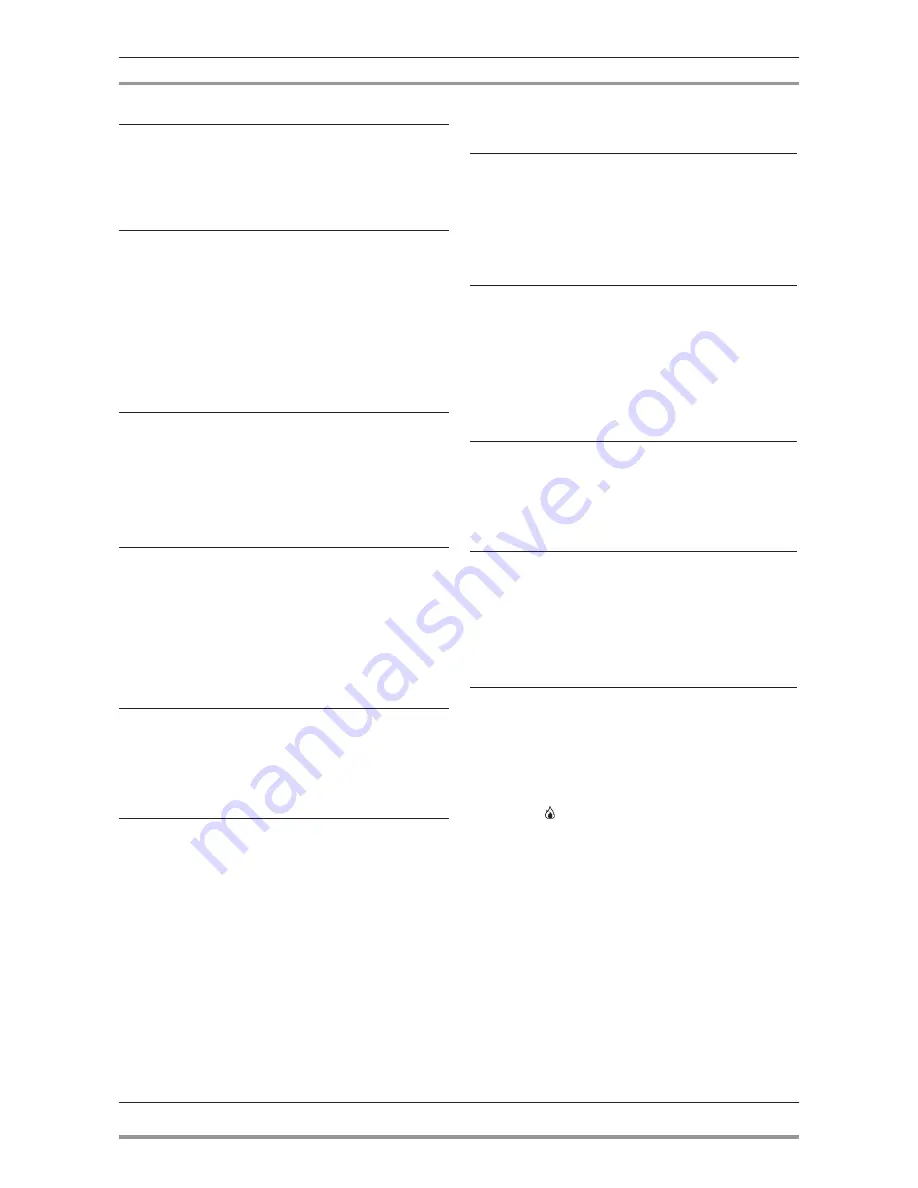
5 - SET-UP FOR OPERATION
5.1.9 Operator training
• Explain and show the user how the machine works according to
the instructions, and hand him this manual.
• Remind the user that any structural alterations or any building
modification or renovation may affect the combustion air supply,
thus requiring a second operation check.
5.1.10 Conversion and adjustment
To change over form one kind of gas to another, for example from
methane to liquid gas, or to another type of gas, the use of suitable
nozzles for the main burner is required, in accordance with the table
"TECHNICAL DATA".
The nozzles of the main burners and pilot for different types of gas,
marked with the relative diameter in hundredths of mm, are in an
envelope which is provided with the appliance. After transforma-
tion or adaptation, carry out operating checks as described in para-
graph 5.1.8, "Operation control."
5.1.11 Replacing burner nozzles of open flames or of
solid top for the models AGB 489/WP - AGS 775/WP
(Fig. 1)
To replace the nozzle (1): remove the grill or the top, the burner
cover, the burner body and the tray of the top.
Then unscrew the screws (2) which fasten the primary air bushing
and replace the nozzle (1). See the table "TECHNICAL DATA".
Once the suitable nozzle has been installed, adjust the distance of
the primary air and fasten the bushing with the appropriate screw.
See the table "TECHNICAL DATA".
5.1.12 Setting reduced capacity power (Fig. 1)
The minimum setting screw (5) should be adjusted as follows:
• for operation with LPG it should be screwed all the way down;
• for operation with methane, use the gas flow table to check the
value in l/min with respect to the operating alorific value (meas-
urement in accordance with the volumetric method). Start the
appliance in accordance with the instructions. Turn the knob to
the minimum position and use screw (5) to adjust the flow (clock-
wise = flow reduction; conter-clockwise = flow increase).
5.1.13 Replacement of pilot nozzle for gas oven GN 2/1
(Fig. 2A)
Remove the front/lower panel by removing the fastening screws.
Remove the closure (11). Use a screwdriver to unscrew and replace
the nozzle (12) (see table, "TECHNICAL DATA").
When finished, replace the closing screw (11) and the relative seal (13).
5.1.14 Replacement of pilot nozzle for gas oven MAXI
(Fig. 2C)
After opening the oven door, remove the protection from the nozzle
zone, remove the nut (11), slide out the bicone (13) and the injector (12).
Replace the injector (12), see the table "TECHNICAL DATA", and
replace all parts in reverse order.
5.1.15 Replacement of pilot nozzle for gas oven GN 2/1
(Fig. 2A)
Remove the lower panel as previously described. Remove the fas-
tening screw (2) of the primary air bushing (4) and push the bushing
into the venturi tube. The nozzle (3) is now easily accessible.
After substituting the nozzle based on the type of gas and the tech-
nical data, reassemble everything and adjust the distance "A" of the
primary air. See the table "TECHNICAL DATA".
5.1.16 Replacement of nozzle of gas oven GN 1/1 (Fig.
2B) and gas oven MAXI (Fig. 2C)
After opening the door, remove the grill, the grill supports and the
stainless steel bottom, then unscrew the protection form the nozzle
zone.
Remove the air adjustment by unscrewing screw (2). The nozzle is
now accessible. Replace it with one that is suitable for the type of
gas to be used. See the table "TECHNICAL DATA". After replace-
ment, reassemble everything and perform air adjustment (see the
table "TECHNICAL DATA").
5.1.17 Adjusting the pilot flame (solid top AGB 488/WP
- AGB 491/WP) (Fig. 5)
Remove the control panel after having loosened the fixing screws.
Remove securing screw (11).
Use a screwdriver to set the adjusting screw (12) according to the
gas used.
Replace securing screw (11) and relative gasket (13).
5.1.18 Replacing the burner nozzle (solid top Fig. 5)
Remove the bottom panel as described above. Loosen screw (45)
fixing the primary air bushing and push the latter into the Venturi
tube.
The nozzle is now perfectly accessible.
After replacing the nozzle according to the type of gas being used
and the technical data, reassemble everything and adjust the pri-
mary air distance “A” (see “technical data” table).
5.1.19 Adjusting the low flame (solid top, Fig. 5)
After having removed the control panel, adjust the low flame screw
(50) as follows:
-
when using LPG, it should be fully screwed down;
-
when using natural gas, check the gas flow table for the value in
l/min which corresponds to the working heat value (calculated
according to the volumetric method).
Turn on the appliance according to the instructions, turning the
knob to high (
) for about 15 minutes, then turn the knob to low
and using screw (50) adjust the flow (clockwise = decrease in flow;
counter-clockwise = increase in flow).
064_03
- GAS KITCHENS
15
· 26
07/2007