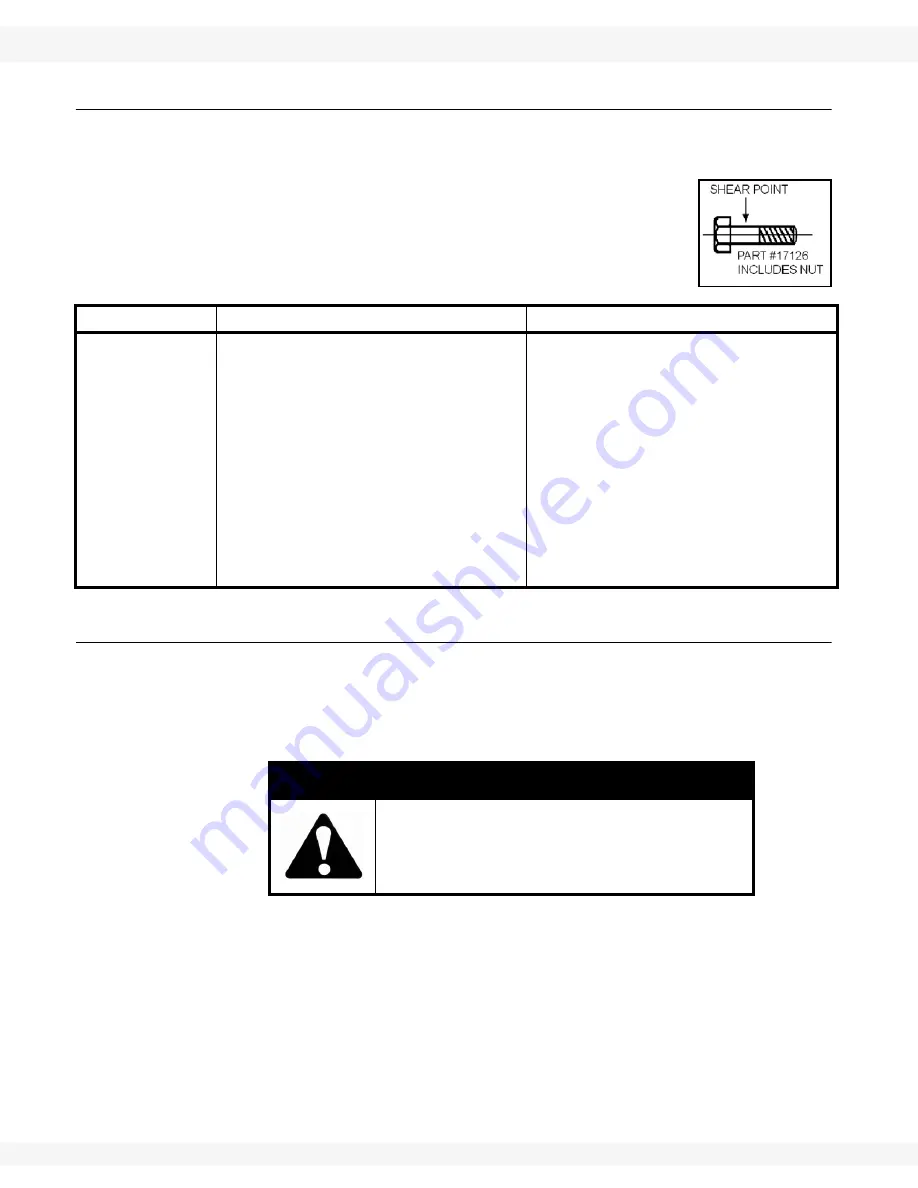
5. O
PERATION
W
ESTFIELD
- G
RAIN
A
UGERS
MK 130 P
LUS
X
61’ - 81’
58
30259
5.2. AUGER DRIVE & LOCKOUT PROCEDURE
Note: If shearbolt in the PTO driveline fails, shut down and lock out tractor to replace
bolt.
The MK130 Plus uses one 3/8” x 1" grade 8 bolt through the
shank shear. Part 18454 includes nut.
5.3. HYDRAULICS
1. Ensure that the hydraulic line is properly connected and secure.
2. Keep hydraulic line away from moving parts.
3. Do not disconnect the hydraulic coupling when under pressure. For the cor-
rect procedure, consult this manual or your tractor manual.
Drive Type
Before Operation
Lockout
PTO Driveline
Before starting, ensure
• PTO driveline is securely
attached to the tractor and jack-
haft
• tractor park brake in engaged
and/or wheels are chocked
• you are not exceeding the maxi-
mum operating length of 40-5/8”
of the PTO driveline
• PTO drive on the tractor is in the
off position
Shut off tractor’s engine and remove
key or coil wire from tractor.
• If removing key is impossible,
remove PTO driveline from trac-
tor.
WARNING
Escaping hydraulic fluid under pressure can
cause serious injury if it penetrates the skin.
Wear protective clothing when working
around hydraulic equipment.
Содержание MK 130 PLUS 71
Страница 6: ...1 INTRODUCTION WESTFIELD GRAIN AUGERS MK 130 PLUS X 61 81 6 30259 ...
Страница 14: ...2 SAFETY FIRST WESTFIELD GRAIN AUGERS MK 130 PLUS X 61 81 14 30259 Figure 2 2 DECAL 17698 DECAL 28615 ...
Страница 18: ...2 SAFETY FIRST WESTFIELD GRAIN AUGERS MK 130 PLUS X 61 81 18 30259 ...
Страница 32: ...3 ASSEMBLY WESTFIELD GRAIN AUGERS MK 130 PLUS X 61 81 32 30259 Figure 3 19 ...
Страница 50: ...3 ASSEMBLY WESTFIELD GRAIN AUGERS MK 130 PLUS X 61 81 50 30259 ...
Страница 72: ...7 TROUBLESHOOTING WESTFIELD GRAIN AUGERS MK 130 PLUS X 61 81 72 30259 ...
Страница 74: ...8 APPENDIX WESTFIELD GRAIN AUGERS MK 130 PLUS X 61 81 74 30259 ...