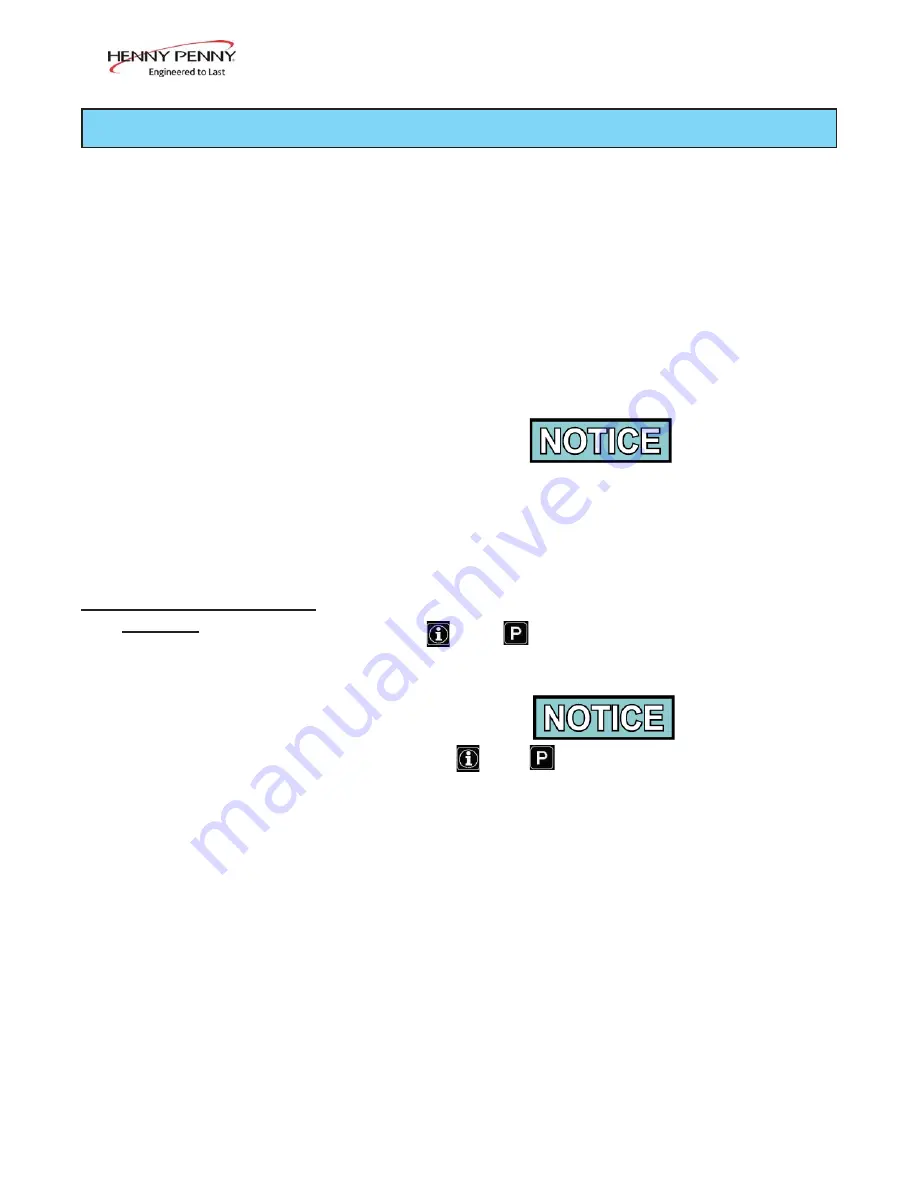
Model EEG-153, 154
3-1
SECTION 3. INFORMATION MODE
This historic information can be recorded and used for operation-
al and technical help and allows you to view the following:
• 1. E-LOG
• 2. LAST LOAD
• 3. DAILY STATS
• 4. OIL STATS
• 5. REVIEW USAGE
• 6. INPUTS
• 7. OUTPUTS
• 8. OIL TEMP
Not all Information Mode functions are discussed in this
section. To ensure proper operation of fryer, please consult
Henny Penny Corp. before changing any of these settings.
For more information on these functions, contact Technical
Support at 1-800-417- 8405, or 1-937-456-8405.
1. E-LOG
(error code log)
Press and buttons at the same time and “*INFO
MODE*” shows in the display, followed by “1. E-LOG”.
Press and to exit Information Mode at anytime.
Press ▼ and “A. (date & time) *NOW* show in displays.
This is the present date and time.
Press ▼ and if a error was recorded, “B. (date, time, and
error code information)” shows in display. This is the latest error
code that the controls recorded.
Press ▼ and the next latest error code information can be seen.
Up to 10 error codes (B to K) can be stored in the E-LOG
section.
• 9. CPU TEMP
• 10. COMMUNICATION INFO
• 11. ANALOG INFO
• 12. ACTIVITY LOG
• 13. OIL LEVELS
• 14. PUMP VALVE INFO
• 15. AIF INFO
3-1. INFORMATION MODE
DETAILS
May 2012
Содержание EVOLUTION ELITE EEG-15 Series
Страница 1: ...SERVICE M A N U A L WENDY S EVOLUTION ELITE Gas REDUCED OIL CAPACITY OPEN FRYER MODEL EEG 153 EEG 154...
Страница 2: ......
Страница 67: ...Model EEG 153 154 6 25 83289 1 2 WELL FULL VAT 3 4 WELL SEE NEXT PAGE May 2012...
Страница 68: ...Model EEG 153 154 6 26 77318 3 4 WELL FULL VAT 1 2 WELL SEE PREVIOUS PAGE May 2012...
Страница 69: ...Model EEG 153 154 6 27 May 2012...
Страница 70: ......
Страница 71: ......