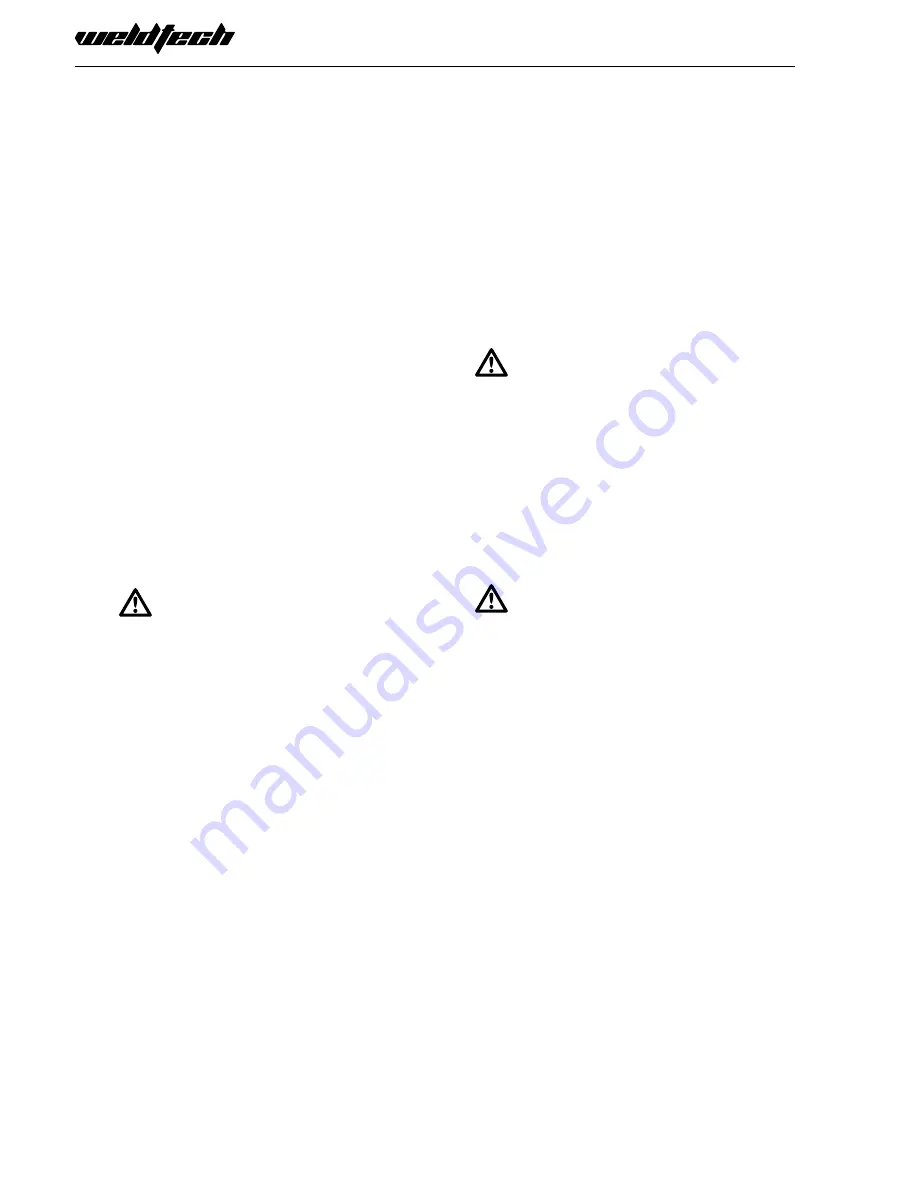
32
8. Connect the work lead/clamp to the job as close
to the welding area as practical to prevent weld-
ing current from travelling long, possibly un-
known paths and causing electric shock and fire
hazards.
9. Do not use a welder to thaw frozen pipes.
10. Remove the stick electrode from the holder or
cut off the welding wire at the contact tip when
not in use.
Sparks & Hot Metal
WARNING!
Chipping and grinding causes flying metal, and
as welds cool they can throw off slag.
1. Wear an AS/NZS approved face shield or safety
goggles. Side shields are recommended.
2. Wear appropriate safety equipment to protect
the skin and body.
Cylinders
WARNING!
Gas cylinders contain gas under high pressure. If
damaged, a cylinder can explode. Since gas cyl-
inders are normally part of the welding
process, be sure to treat them carefully.
1. Protect compressed gas cylinders from excessive
heat, mechanical shocks, and arcs.
2. Install and secure cylinders in an upright posi-
tion by chaining them to a stationary support or
equipment cylinder rack to prevent falling or tip-
ping.
3. Keep cylinders away from any welding or other
electrical circuits.
4. Never allow a welding electrode to touch any
cylinder.
5. Use appropriate shielding gas, regulators, hoses,
and fittings designed for the specific application;
maintain them and their associated parts in
good condition.
6. Turn your face away from the valve outlet when
opening the cylinder valve.
3. If ventilation is poor, use an approved air-sup-
plied respirator.
4. Read the Safety Data Sheets (SDS) and the man-
ufacturer’s instruction for the metals, consuma-
bles, coatings, and cleaners.
5. Work in a confined space only if it is well venti-
lated, or while wearing an air-supplied respirator.
Shielding ga es used for welding can displace air
causing injury or death. Be sure the breathing air
is safe.
6. Do not weld in locations near degreasing, clean-
ing, or spraying operations. The heat and rays of
the arc can react with vapours to form highly
toxic and irritating gases.
7. Do not weld on coated metals, such as galva-
nized, lead, or cadmium plated steel, unless the
coating is removed from the weld area, the area
is well ventilated, and if necessary, while wearing
an air- supplied respirator. The coatings and any
metals containing these elements can give off
toxic fumes if welded.
Fire & Explosive Risks
WARNING!
Sparks and spatter fly off from the welding arc.
The flying sparks and hot metal, weld spatter,
work piece, and hot equipment can cause fires
and burns.
Accidental contact of electrode or welding wire to
metal objects can cause sparks, overheating, or fire.
1. Protect yourself and others from flying sparks
and hot metal.
2. Do not weld where flying sparks can strike flam-
mable material.
3. Remove all flammables within 10m of the weld-
ing site.
4. Be alert that welding sparks and hot materials
from welding can easily go through small cracks
and openings to adjacent areas.
5. Watch for fire, and keep a fire extinguisher near-
by.
6. Be aware that welding on a ceiling, floor, bulk-
head, or partition can cause fire on the hidden
side.
7. Do not weld on closed containers such as tanks
or drums.
Содержание WT200MP
Страница 1: ...OPERATING INSTRUCTIONS WT200MP 200A MULTI PROCESS MIG MMA STICK TIG WELDER www weldtech net nz...
Страница 10: ...10 Welding Settings...
Страница 24: ...24 MMA Stick Troubleshooting...
Страница 27: ...27 WT200MP Welding Machine www weldtech net nz TIG Welding Troubleshooting...
Страница 34: ...34...
Страница 35: ...35 WT200MP Welding Machine www weldtech net nz...