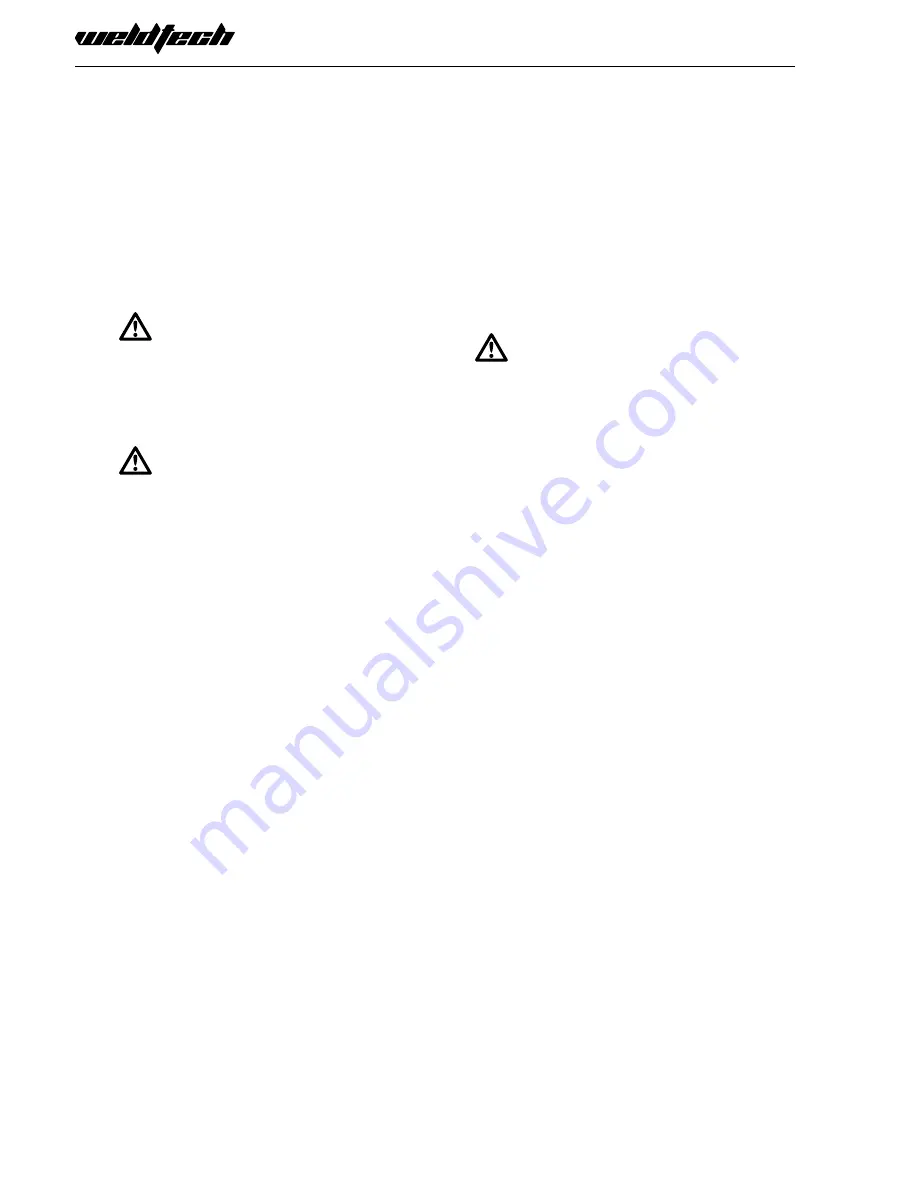
24
3. Use protective screens or barriers to protect
others from flash and glare; warn others not to
watch the arc.
4. Wear protective clothing made from durable,
flame-resistant material (wool and leather) and
foot safety protection.
5. Never wear contact lenses while welding.
Noise Can Damage Hearing
CAUTION!
Noise from some processes can damage hearing.
Use AS/NZS compliant ear plugs or ear muffs if
the noise level is high.
Work Environment Safety
DANGER!
Remove any combustible material from the work
area.
1. When possible, move the work to a location well
away from combustible materials. If relocation
is not possible, protect the combustibles with a
cover made of fire resistant material.
2. Remove or make safe all combustible materials
for a radius of 10 metres around the work area.
Use a fire resistant material to cover or block all
doorways, windows, cracks, and other openings.
3. Enclose the work area with portable fire resistant
screens. Protect combustible walls, ceilings,
floors, etc., from sparks and heat with fire re-
sistant covers.
4. If working on a metal wall, ceiling, etc., prevent
ignition of combustibles on the other side by
moving the combustibles to a safe location. If
relocation of combustibles is not possible, desig-
nate someone to serve as a fire watch, equipped
with a fire extinguisher, during the welding pro-
cess and well after the welding is completed.
5. Do not weld or cut on materials having a com-
bustible coating or combustible internal struc-
ture, as in walls or ceilings, without an approved
method for eliminating the hazard.
6. After welding, make a thorough examination for
evidence of fire. Be aware that visible smoke or
flame may not be present for some time after
the fire has started. Do not weld or cut in atmos-
pheres containing dangerously reactive or flam-
mable gases, vapours, liquids, and dust. Provide
adequate ventilation in work areas to prevent ac-
cumulation of flammable gases, vapours, and dust.
7. Do not apply heat to a container that has held
an unknown substance or a combustible mate-
rial whose contents, when heated, can produce
flammable or explosive vapours. Clean and
purge containers before applying heat. Vent
closed containers, including castings, before pre-
heating, welding, or cutting.
Electricity Can Kill
DANGER!
Touching live electrical parts can cause fatal shocks
or severe burns. The electrode and work circuit is
electrically live whenever the output is on.
The input power circuit and machine internal circuits
are also live when power is on. In semi-automatic or
automatic wire welding, the wire, wire reel, drive roll
housing, and all metal parts touching the welding
wire are electrically live. Incorrectly installed or im-
properly grounded equipment is a hazard.
1. Do not touch live electrical parts.
2. Wear dry, hole-free insulating gloves and body
protection.
3. Insulate yourself from the work and the ground
using dry insulating mats or covers.
4. Disconnect input power before installing or ser-
vicing this equipment. Lock input power, discon-
nect switch open, or remove line fuses so power
cannot be turned on accidentally.
5. Properly install and ground this equipment ac-
cording to national, state, and local codes.
6. Turn off all equipment when not in use. Discon-
nect power to equipment if it will be left unat-
tended or out of service.
7. Use fully insulated electrode holders. Never dip
the holder in water to cool it or lay it down on
the ground or the work surface. Do not touch
holders connected to two welding machines at
the same time or touch other people with the
holder or electrode.
8. Do not use worn, damaged, undersized, or poor-
ly spliced cables.
9. Do not wrap cables around your body.
10. Connect work piece to a good electrical ground.
Содержание EZITIG 200AC/DC
Страница 1: ...OPERATING INSTRUCTIONS EZITIG 200AC DC 200A MULTI PROCESS TIG WELDER www weldtech net nz...
Страница 11: ...11 EZITIG200 AC DC Welding Machine www weldtech net nz Wiring Diagram...
Страница 18: ...18 MMA Stick Troubleshooting...
Страница 21: ...21 EZITIG200 AC DC Welding Machine www weldtech net nz TIG Welding Troubleshooting...