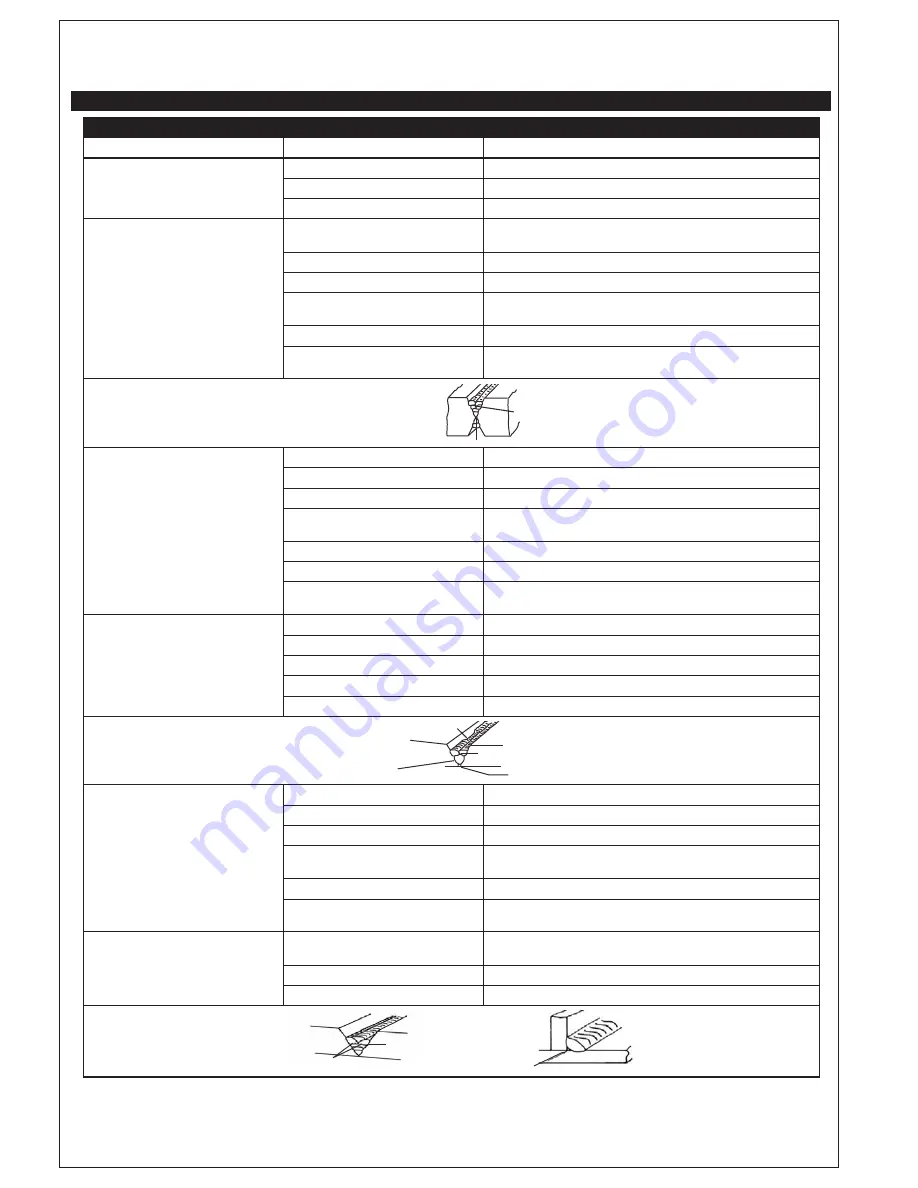
MMA WELDING TROUBLESHOOTING
Troubleshooting - MMA Weld Quality
Fault
Cause
Remedy
A gap is left by failure of the weld metal to
fill the root of the weld.
Welding current too low.
Increase welding current.
Electrode too large for joint.
Use smaller diameter electrode.
Insufficient gap.
Allow wider gap.
Non-metallic particles are trapped in the
weld metal.
Non-metallic particles may be trapped in
undercut from previous run.
If a bad undercut is present clean slag bout and cover with a run from a
smaller gauge electrode.
Joint preparation too restricted.
Allow for adequate penetration and room for cleaning out the slag.
Irregular deposits allow slag to be trapped.
If very bad, chip or grind out irregularities.
Lack of penetration with slag trapped
beneath weld bead.
Use smaller electrode with sufficient current to give adequate penetra-
tion. Use suitable tools to remove all slag from comers.
Rust or mill scale is preventing full fusion.
Clean joint before welding.
Wrong electrode for position in which
welding is done.
Use electrodes designed for position in which welding is done, otherwise
proper control of slag is difficult.
Incorrect Sequence
Figure 1: Example of insufficient gap or incorrect sequence
Insufficient Gap
A groove has been formed in the base
metal adjacent to the toe of a weld and
has not been filled by the weld metal
(undercut).
Welding current is too high.
Reduce welding current.
Welding arc is too long.
Reduce the length of the welding arc.
Angle of the electrode is incorrect.
Electrode should not be inclined less than 45° to the vertical face.
Joint preparation does not allow correct
electrode angle.
Allow more room in joint for manipulation of the electrode.
Electrode too large for joint.
Use smaller gauge electrode.
Insufficient deposit time at edge of weave.
Pause for a moment at edge of weave to allow weld metal build-up.
Power source is set for MIG (GMAW)
welding.
Set power source to STICK (MMA) mode.
Portions of the weld run do not fuse to the
surface of the metal or edge of the joint.
Small electrodes used on heavy cold plate.
Use larger electrodes and preheat the plate.
Welding current is too low.
Increase welding current.
Wrong electrode angle.
Adjust angle so the welding arc is directed more into the base metal.
Travel speed of electrode is too high.
Reduce travel speed of electrode.
Scale or dirt on joint surface.
Clean surface before welding.
Figure 2: Example of Lack of Fusion
Lack of inter-run fusion
Lack of side fusion, scale dirt;
small electrode; amperage too low
Lack of fusion caused by dirt; electrode
angle incorrect; rate of travel too high
Lack of root fusion
Gas pockets or voids in weld metal
(porosity)
High levels of sulphur in steel.
Use an electrode that is designed for high sulphur steels.
Electrodes are damp.
Dry electrodes before use.
Welding current is too high.
Reduce welding current.
Surface impurities such as oil, grease,
paint, etc.
Clean joint before welding.
Welding in a windy environment.
Shield the weld area from the wind.
Electrode damaged i.e. flux coating
incomplete.
Discard damaged electrodes and only use electrodes with a complete
flux coating.
Crack occurring in weld metal soon after
solidification commences
Rigidity of joint.
Redesign to relieve weld joint of severe stresses or use crack resistance
electrodes.
Insufficient throat thickness.
Travel slightly slower to allow greater build up in throat.
Weld current is too high.
Decrease welding current.
Figure 3: Example of Slag Inclusion
Not cleaned, or incorrect electrode
Slag trapped
in undercut
Slag trapped in root
15