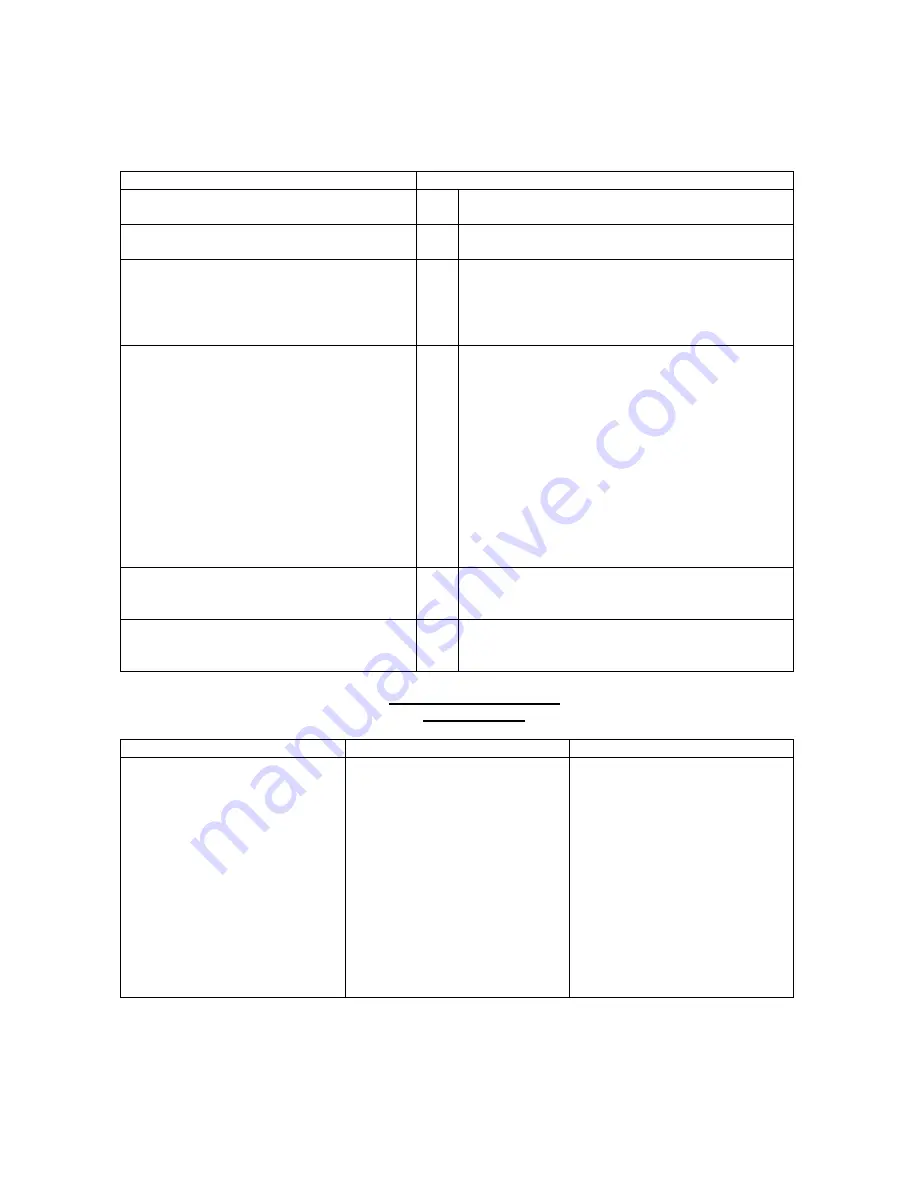
© Welding Industries Malaysia Sdn. Bhd. reserves all rights even in the event of industrial property rights. We reserve all rights of dis-
posal such as copying and passing on to third parties. Specification may vary from country to country. V1.1.06
10.0 WELDING FAULTS
FAULT
POSSIBLE CAUSE AND REMEDY
1 Wel
d deposit ‘stringy’ and incomplete
1 a
1 b
Torch moved over workpiece too quickly
Gas mixture incorrect
2 Weld deposit too thick
2 a
2 b
Torch moved over workpiece too slowly
Welding voltage too low
3 Arc unstable excessive spatter and
weld porosity
3 a
3 b
3 c
Torch held too far from the workpiece
Rust grease or paint on workpiece
Insufficient shielding gas; check gas contents
gauge, regulator setting and operation of gas
valve
4 Wire repeatedly burns back
4 a
4 b
4 c
Torch held too close to the workpiece
Intermittent break in the welding circuit caused
by:
(1) Contact tip loose-tighten
(2) Contact tip damaged-replace
(3) Welding wire or liner corroded-replace
wire or liner
Wire feed slipping caused by:
(1) Restriction in liner (such as kinks) or
contact tip-check and replace if necessary
(2) Worn-out feed rolls-replace
(3) Guide tube or pressure roll alignments
incorrect.
5 Burning holes in the workpiece
5 a
5 b
5 c
Torch moved too slowly or erratically
Welding volts too high
Wire feed speed too high
6 Lack of penetration
6 a
6 b
6 c
Torch moved too fast
Welding volts too low
Wire feed speed too low
SHIELDING GAS TABLE
MIG WELDING
Metal
Gas
Remarks
Mild Steel
CO2
Argon + CO2
Argon + CO2 + Oxygen
Argon controls spatter
Oxygen improves arc stability
Aluminium
Argon
Argon Helium
Stable Arc-Sound welds
Higher heat input
Suitable for heavy sections
Stainless Steel
Argon + CO2 + Oxygen
Argon + Oxygen
Arc stability
Minimum spatter
Copper, Nickel and Alloys
Argon
Argon Helium
Suitable for light gauges
Higher heat input
Suitable for heavy sections