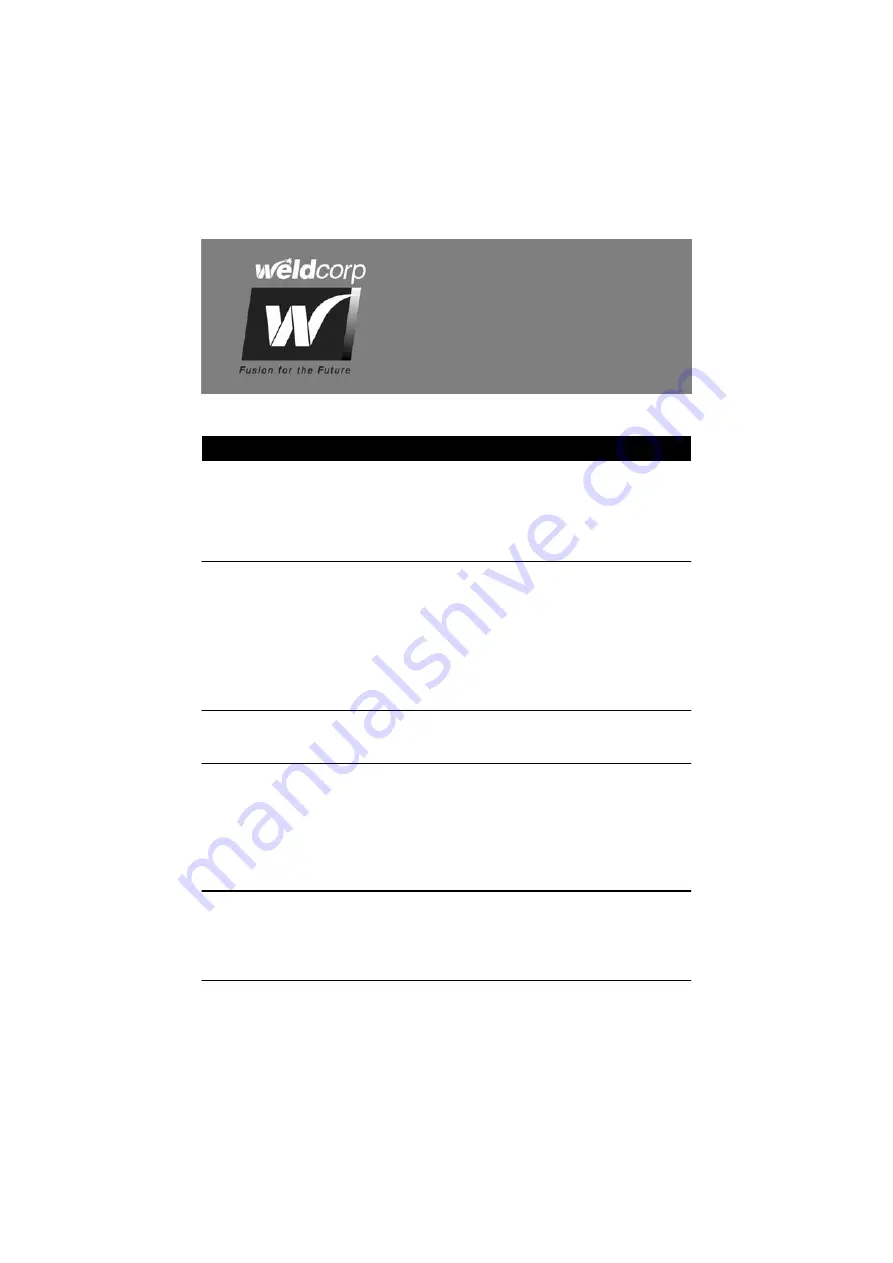
Page 16
T R O U B L E S H O O T I N G G U I D E
FAULT
REASON
REMEDY
Excessive
Electrode
Consumption
Improper size/or geometry
of electrode for current
required
Use larger electrode
Excessive heating in holder Check for proper contact
Contaminated electrode
Replace electrode
Contami-
nated
Electrode
Base metal is dirty or
greasy
For surface cleanliness use appropriate
chemical cleaners alcohol, wire brush or
abrasive
Contaminant
elements
that
our gas may exist within
the base material itself
If possible, improve base material.
Modify welding parameters to accom-
modate out gassing effect
Check for electrode con-
tamination
Remove contaminated portion of elec-
trode, regrind electrode
Electrode
Dimensions
Be sure electrode dimen-
sions are appropriate for
application
Electrode tip dimensions vary according
to the welding application—refer to the
guide on page 10
Cable Layout In so far as possible, try to
layout cables from power
supply to welding torch as
straight as possible
Occasionally, cables are coiled like a
garden hose. The coil becomes a giant
inductor causing resistance that re-
duces starting energy. Inductance ef-
fects can also be caused by having
welding power cables very close to
grounded steel plates.
Grounding
Problems
Make sure clamps and
clamp inserts are clean of
oxidation. Make sure
ground clamp is not worn.
Oxidation and/ or worn equipment can
cause poor ground between part and
clam/ inserts which may hinder arc
starting, wander and other inconsisten-
cies.