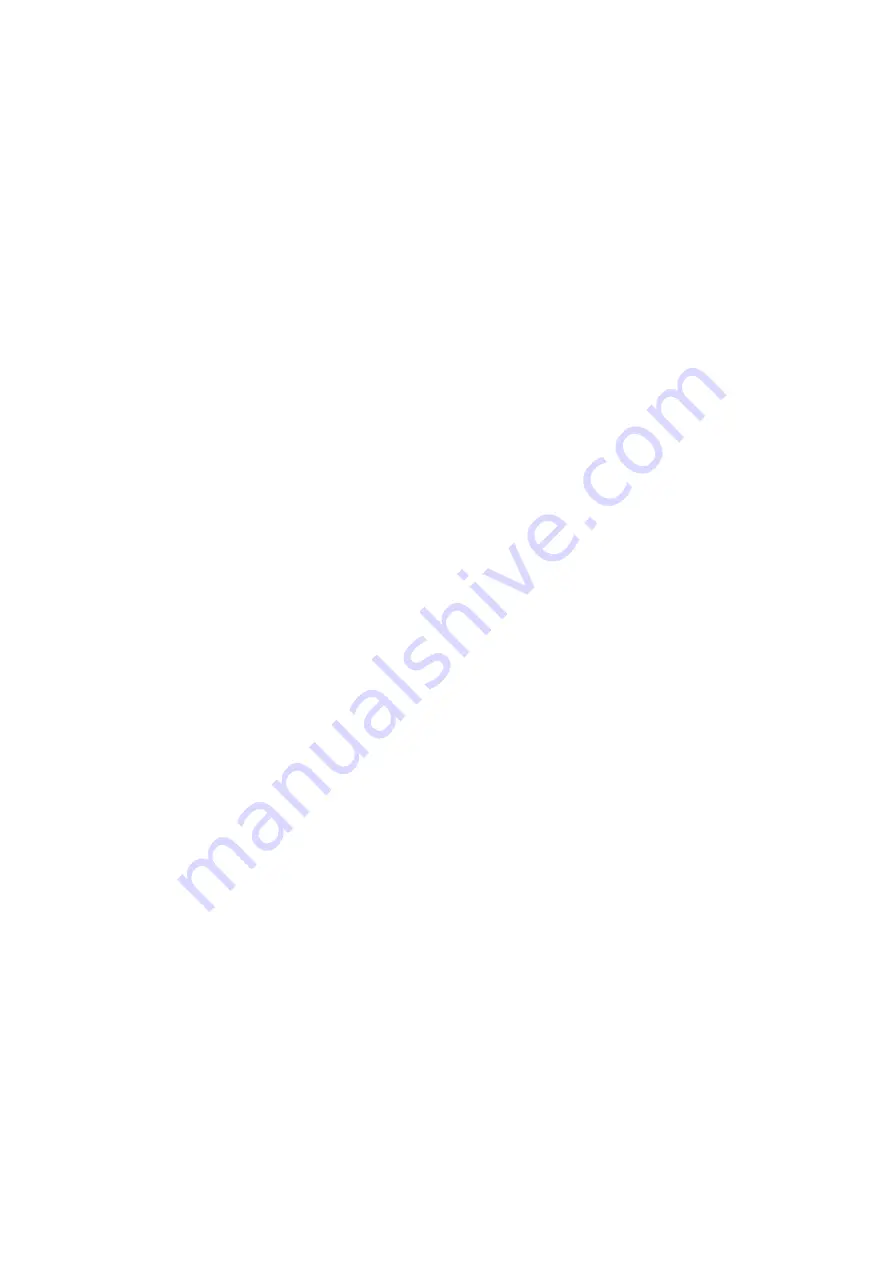
11.8
Establishing the Arc and Making Weld Beads
Before attempting to weld on a finished piece of work, it is recommended that practice welds be made on
a sample metal of the same material as that of the finished piece. The easiest welding procedure for the
beginner to experiment with MIG welding is the flat position. The equipment is capable of flat, vertical and
overhead positions. For practicing MIG welding, secure some pieces of 1.6mm or 2.0mm mild steel plate
(150 x 150mm). Use 0.9mm flux cored gasless wire or a solid wire with shielding gas.
11.9
MIG Voltage & Wire Speed Settings
Manual MIG welding setting requires some practice by the operator, as the machine has two control
settings that have to balance. These are the Wire Speed control and the welding Voltage control.
Voltage is essentially the power in the welding arc that sets the heat. The wire speed feed simply controls
the rate at which the welding wire is fed into the weld pool. For any voltage position setting, there will be
a specific corresponding ‘sweet spot’ in the wire feeding speed that will give the smoothest and most stable
welding arc. The correct wire feeding speed for a given voltage setting is affected by welding wire type and
size, shielding gas, welding material and joint type.
The recommended process for setting a MIG (in Manual mode) is:
1.
Set the welding voltage as desired
2.
Slowly adjust the wire speed until the arc is smooth and stable.
3.
When reaching this point, if the penetration/ heat input is too much/ not enough, adjust the
voltage setting and repeat the process.
4.
If not able to achieve a smooth and stable arc with the desired heat input for the weld, it is likely
that a change in wire size and/or shielding gas type is required (assuming all other factors are
correct).
Synergic function makes the setup of MIG welding much simpler as follows:
1.
Choose Synergic program to suit wire type and size and shielding gas
2.
Select amperage output or material thickness
3.
The machine calculates the optimal voltage and wire speed for the application
4.
Obviously other variables such as welding joint type, position and thickness, air temperature can
affect the optimal voltage and wire feed setting, so voltage can be adjusted to fine-tune for
optimal performance.
11.9.1
Setting Wire Speed/Amperage
The welding current (amperage) is determined by the Wire Speed control.
Increased Wire Speed will increase the current and result in a shorter arc.
Less Wire Speed will reduce the current and lengthen the arc.
11.9.2
Setting Voltage
Increasing the welding voltage hardly alters the current level, but lengthens the arc. By decreasing the
voltage, a shorter arc is obtained with a little change in current level.
11.9.3
Changing to a different welding wire
When changing to a different welding wire diameter, different control settings are required. A thinner
welding wire needs more Current (Wire Speed) to achieve the same current level. A satisfactory weld
cannot be obtained if the Current (Wire Speed) and Voltage settings are not adjusted to suit the welding
wire diameter and the dimensions of the work piece.
Содержание WeldForce WF-205MST
Страница 36: ... 36 Weldclass 2019 E O E Edition 2 1 Figure 25 ...
Страница 37: ...WF 205MST Weldclass 2019 E O E Edition 2 1 37 8 6 Primary Schematic Circuit Diagram Figure 26 ...
Страница 42: ... 42 Weldclass 2019 E O E Edition 2 1 Figure 33 Figure 34 Figure 35 Figure 36 ...
Страница 77: ...WF 205MST Weldclass 2019 E O E Edition 2 1 77 NOTES ...
Страница 78: ... 78 Weldclass 2019 E O E Edition 2 1 ...
Страница 79: ...WF 205MST Weldclass 2019 E O E Edition 2 1 79 ...
Страница 80: ... 80 Weldclass 2019 E O E Edition 2 1 www Weldclass com au WF 205MST ...