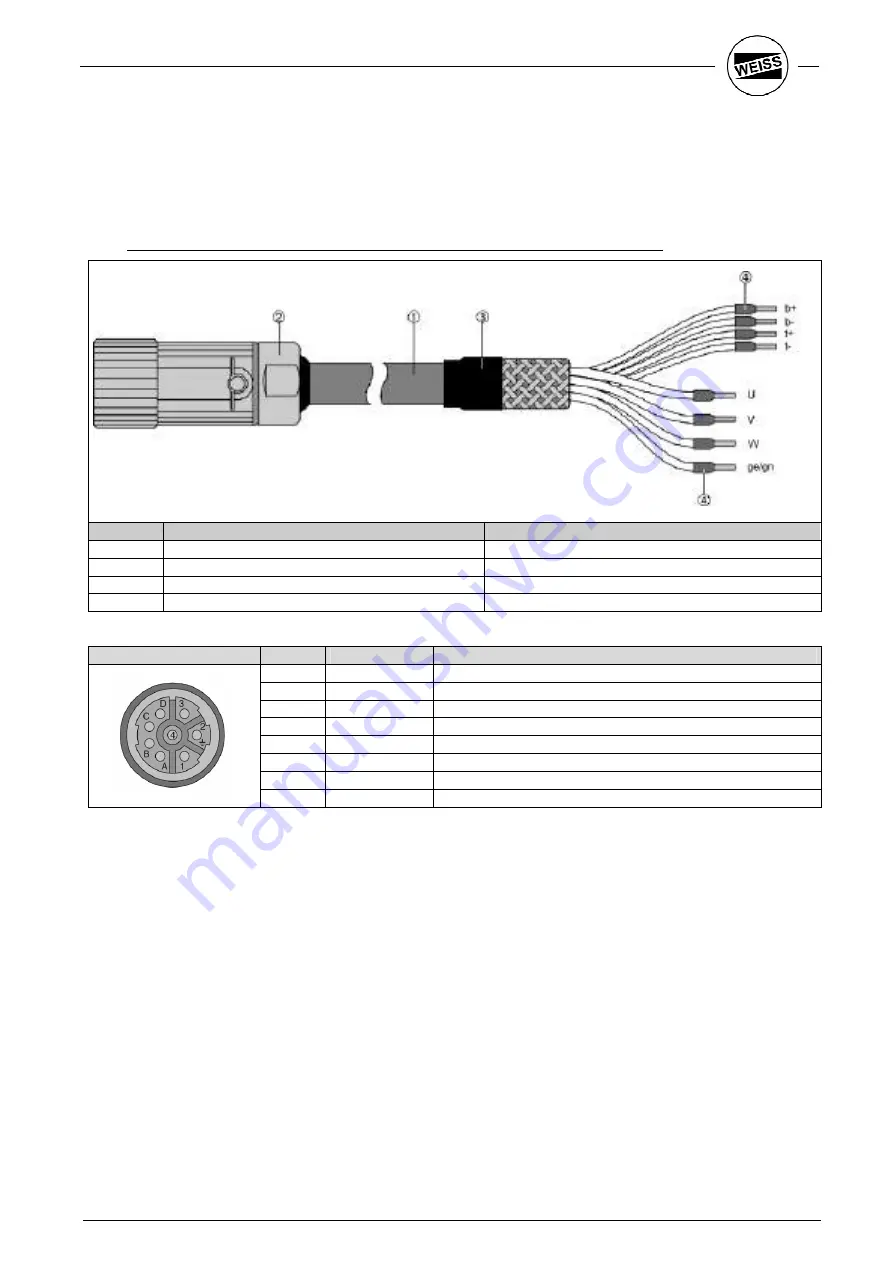
39
WAS.handling Electro Documentation
6 Appendix
6.1 Assignment of Cables
The following lines are available in length 5m, 10m, 15m, 20m, 25m.
6.1.1 Assignment of Motor line (563-100000070…74 to 563-100000080…84):
Item
Description
Remark
1
Motor line
4 x1,5mm² + 2 x 2 x 0,75 mm²
2
Circular Connector
BSTA 108 FR 19 08 0006 000
3
Shrink wrap
4
Wire tip sleeve
Circular Connector
Pin
Designation
Function
1
U
Motor connection U
4
V
Motor connection V
3
W
Motor connection W
2
PE
protective ground connector
A
T+
Temperature sensor
B
T-
Temperature sensor
C
B+
Break + (Reserved)
D
B-
Break - (Reserved)
Rote Marking = vertical motor (Z - Axis)
Blue Marking = horizontal motor (Y - Axis)
Содержание HP140
Страница 1: ...04 2010 ...
Страница 13: ...WAS handling Electro Documentation 10 2 3 Terminology HP140 T B B Type Motor coil Measurement system Design ...
Страница 15: ...WAS handling Electro Documentation 12 Drilling template Fixing screws M5 ...
Страница 17: ...WAS handling Electro Documentation 14 Drilling template Fixing screws M5 ...
Страница 20: ...17 WAS handling Electro Documentation ACOPOS 1022 three phase connection 3 x 400V 480V ...
Страница 46: ...43 WAS handling Electro Documentation ...
Страница 47: ......
Страница 48: ......