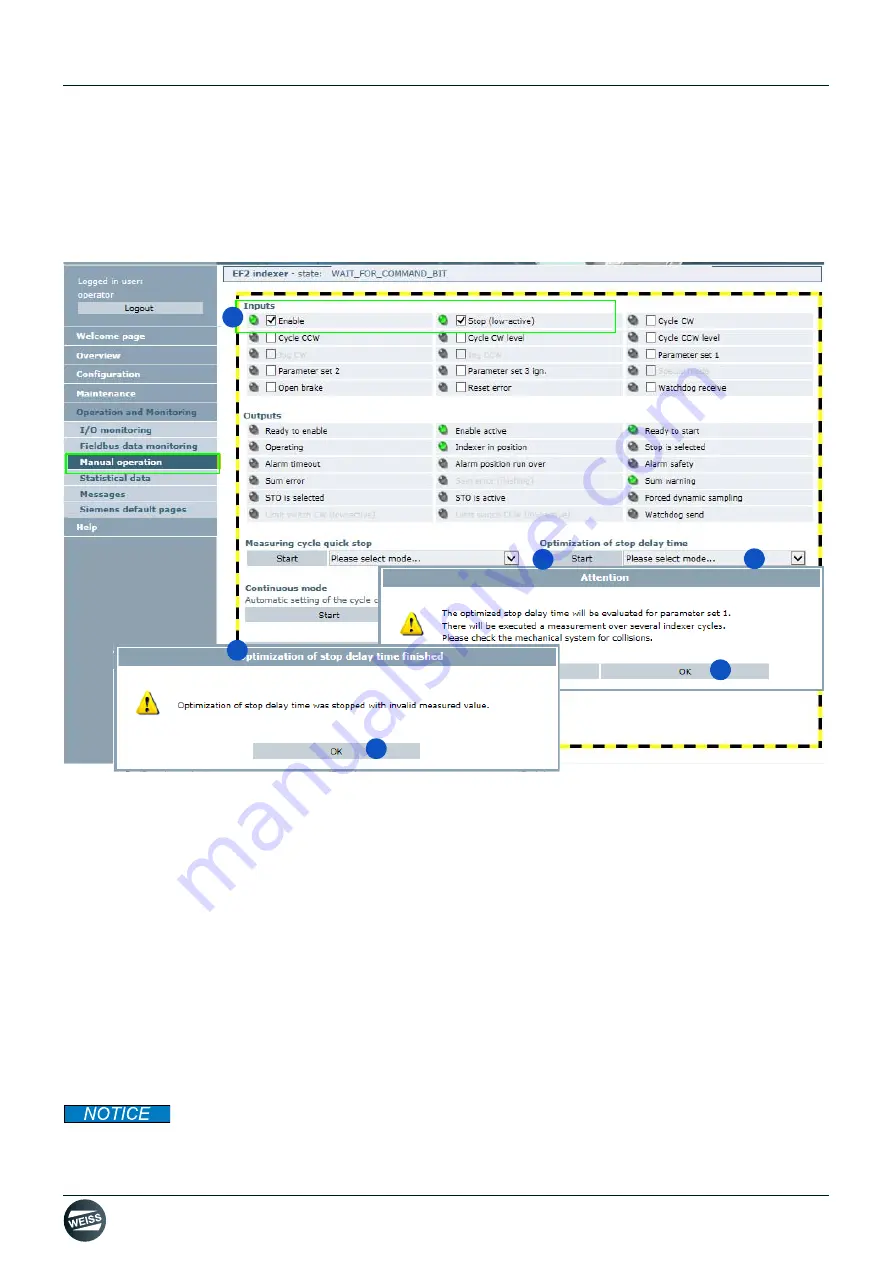
Manual R06-2016
124 / 172
ROTARY INDEXING TABLE CONTROLLER EF2...B
OPERATION / DESCRIPTION OF WEISS SOFTWARE |
8.5 Operation and Monitoring
8.5.3.4 Manual operation: Optimization of stop delay time
Condition for manual operation: The control authority has to be activated.
The control authority of the browser window is indicated by the yellow and black frame around the input field.
The Optimization of stop delay time should always be carried out after the Measuring cycle quick stop.
Fig. 74: Manual operation: Optimization of stop delay time
The "Optimization of stop delay time" function is used to determine the optimal starting position on the position cam.
1. Set the inputs "Enable" and "Stop (low-active)".
These two inputs have to be set in order to enable manual operation.
2. Select mode.
Measurement - only CW
Measurement - only CCW
Alternating
3. Start the "Optimization of stop delay time" function.
Confirm messages in the following windows that open up.
The determined stop delay time will be displayed in the dynamic parameters (chapter 8.3.6 „Dynamic parame-
ters“ on page 107).
4. After finishing manual operation: Release control authority.
Changes
The function needs to be repeated for every change of the rotary indexing table (e.g. change of load).
3.
2.
1.
4.
4.
5.
Содержание 3RT2017-1BB42
Страница 1: ...MANUAL ELECTRICAL SYSTEM DOCUMENTATION ROTARY INDEXING TABLE CONTROLER EN_06_2016 EF2 ...
Страница 170: ...Manual R06 2016 170 172 ROTARY INDEXING TABLE CONTROLLER EF2 B APPENDIX 13 5 Personal notes 13 5 Personal notes ...
Страница 171: ...Manual R06 2016 171 172 ROTARY INDEXING TABLE CONTROLLER EF2 B APPENDIX 13 5 Personal notes ...