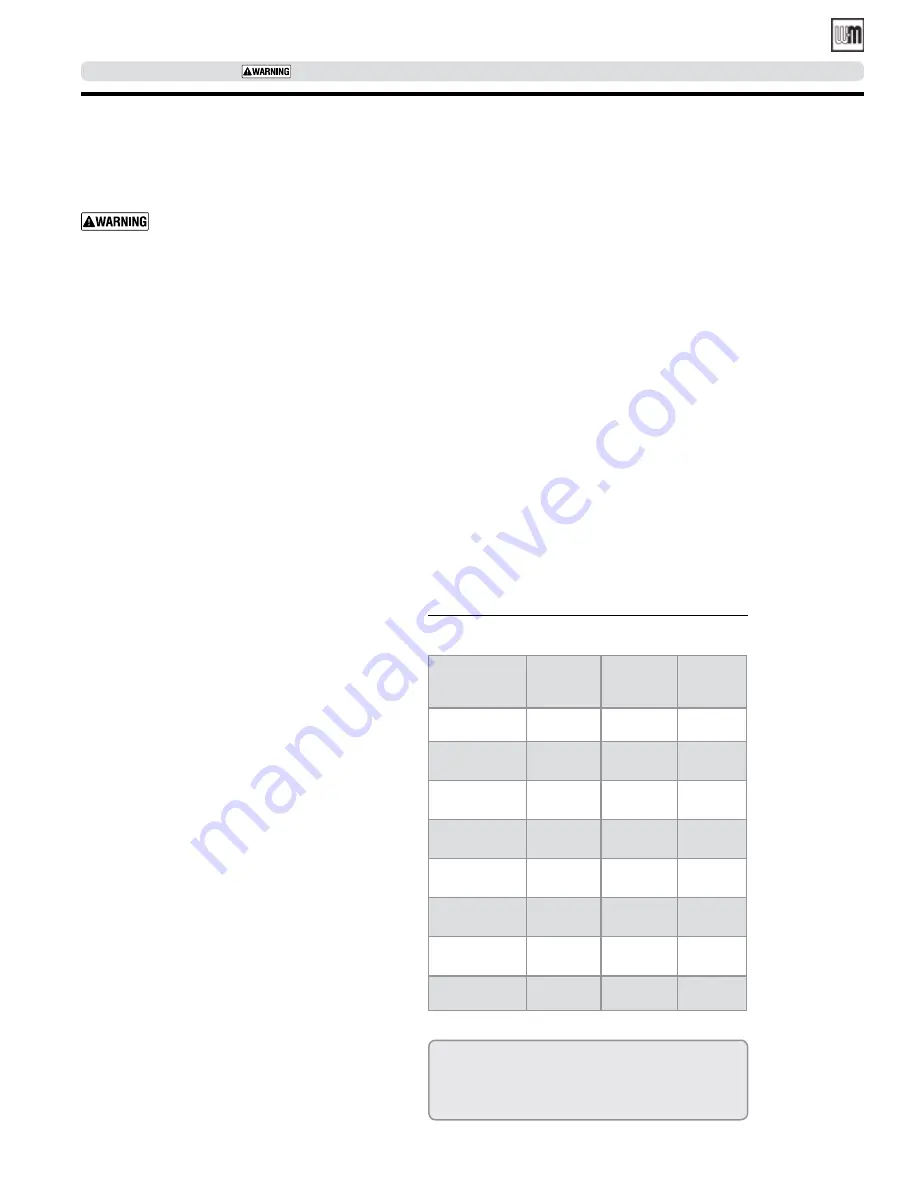
SERVICE TECHNICIAN ONLY — read and follow completely.
Provide air for combustion and
ventilation
Do not install exhaust fan in boiler room.
Adequate combustion and ventilation air:
•
Assures proper combustion.
•
Reduces risk of severe personal injury or death from
possible flue gas leakage and carbon monoxide
emissions.
Older buildings with single-pane windows, minimal
weather-stripping and no vapor barrier often provide
enough natural infiltration and ventilation without
dedicated openings.
New construction or remodeled buildings are most
often built tighter. Windows and doors are weather-
stripped, vapor barriers are used and openings in
walls are caulked. As a result, such tight construction
is unlikely to allow proper natural air infiltration and
ventilation.
Follow state, provincial or local codes when sizing
adequate combustion and ventilation air openings. In
absence of codes, use the following guidelines when
boiler is in a confined room (defined by NFPA 31 as
as less than 7200 cubic feet per 1 GPH input of all ap-
pliances in area. A room 8 ft. high x 33.5 ft. x 33.5 ft.
is 7200 cu. ft.).
Permanent Openings
Provide two permanent openings, one within 12 inches
of ceiling, one within 12 inches of floor. Minimum
height or length dimension of each rectangular opening
should be at least 3 inches.
Inside air
When inside air is used, each opening must freely
connect with areas having adequate infiltration from
outside. Each opening should be at least 140 sq. in. per
1 GPH input (1 sq. in. per 1000 Btu input) of all fuel-
burning appliances plus requirements for any equip-
ment that can pull air from room (including clothes
dryer and fireplace).
Outside air
When outside air is used, connect each opening directly
or by ducts to the outdoors or to crawl or attic space
that freely connects with outdoors. Size per below:
•
Through outside wall or vertical ducts — at least
35 sq. in. per 1 GPH input (1 sq. in. per 4000 Btu
input) of all fuel-burning appliances plus require-
ments for equipment that can pull air from room
(including clothes dryer and fireplace).
•
Through horizontal ducts — at least 70 sq. in. per 1
GPH boiler input (1 sq. in. per 2000 Btu input) of all
fuel-burning appliances plus requirements for any
equipment that can pull air from room (including
clothes dryer and fireplace).
Where ducts are used, they should have same cross-
sectional area as free area of openings to which they
connect. Compensate for louver, grille or screen block-
age when calculating free air openings. Refer to their
manufacturer’s instructions for details. If unknown,
use:
•
Wood louvers, which provide 20-25% free air.
•
Metal louvers or grilles, which provide 60-75%
free air.
Lock louvers in open position or interlock with equip-
ment to prove open before boiler operation.
Foundation
Lay a foundation, if needed. Boiler may be installed
on non-carpeted combustible flooring. Solid concrete
blocks can be used to create a pad.
For residential garage installation, install boiler so
burner is at least 18 inches above floor to avoid contact
with gasoline fumes.
A level concrete or masonry foundation is required
when:
•
Floor could possibly become flooded.
•
Non-level conditions exist.
Before installing boiler
(continued)
Installation instructions:
Packaged boiler
— Continued on page 10
Non-packaged boiler — Continued on page 12
Boiler
model
Length
inches
Width
inches
Min.
height
inches
WGO-2
14
22
2
WGO-3
17
22
2
WGO-4
17
22
2
WGO-5
20
22
2
WGO-6
23
22
2
WGO-7
26
22
2
WGO-8
29
22
2
WGO-9
32
22
2
Table 1
Boiler foundation sizes
Part number 550-141-826/1014
9
GOLD
WGO
OIL-FIRED NATURAL DRAFT WATER BOILER — SERIES 3 —
Boiler Manual