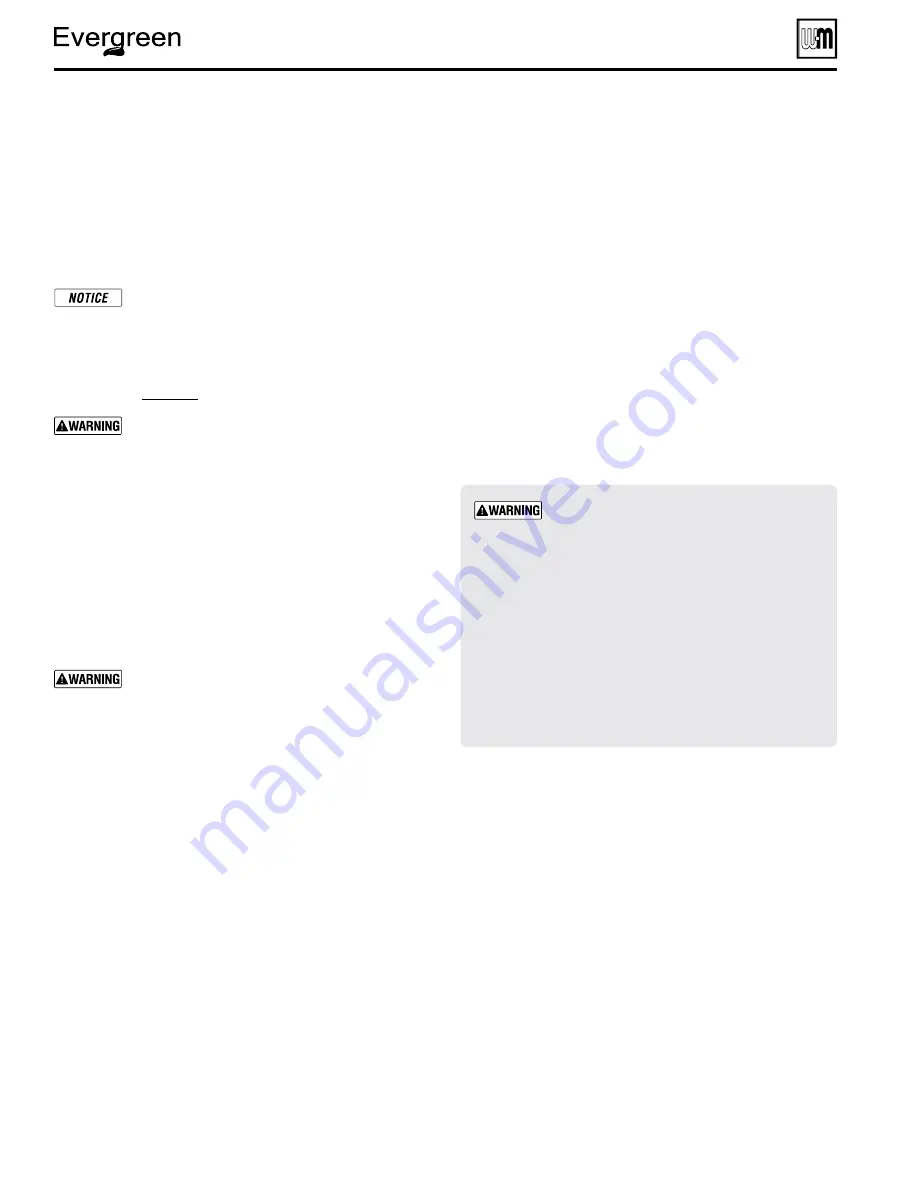
Boiler location
Part number 550-100-131/0120
– 6 –
®
gas
-
fired
water
boiler
— 220/299/300/399
Boiler Manual
Installations must comply with:
• Local, state, provincial, and national codes, laws, regulations
and ordinances.
• National Fuel Gas Code, ANSI Z223.1/NFPA 54 - latest
edition.
• National Electrical Code.
• For Canada only: CAN/CSA B149.1, Natural Gas and Pro-
pane Installation Code, and any local codes.
The
Evergreen
®
boiler gas manifold and controls
met safe lighting and other performance criteria
when boiler underwent tests specified in ANSI
Z21.13 — latest edition.
Flooring
1. The boiler
must not
be installed on carpeting.
Do not install boiler on carpeting even if founda-
tion is used. Fire can result, causing severe personal
injury, death or substantial property damage.
Before locating the boiler, check:
2. The boiler is suitable for INDOOR installation only.
3. Check for nearby connection to:
• System water piping
• Venting connections
• Gas supply piping
• Electrical power
• Condensate drain
4. Check area around boiler. Remove any combustible materials,
gasoline and other flammable liquids.
Failure to keep boiler area clear and free of com-
bustible materials, gasoline and other flammable
liquids and vapors can result in severe personal
injury, death or substantial property damage.
5. The boiler must be installed such that the gas ignition system
components are protected from water (dripping, spraying,
rain, etc.) during appliance operation and service (circulator
replacement, condensate trap, control replacement, etc.).
6. If new boiler will replace existing boiler, check for and correct
system problems, such as:
• Sediment or corrosion in system piping — clean and flush
piping BEFORE connecting the new boiler. See page 86.
• System leaks causing oxygen corrosion or heat exchanger
cracks from hard water deposits.
• Incorrectly-sized expansion tank.
• Lack of freeze protection in boiler water causing system
and boiler to freeze and leak.
Residential garage installation
Precautions
1. Take the following special precautions when installing the
boiler in a residential garage. If the boiler is located in a
residential garage:
• Mount the boiler with its bottom at least 18 inches above
the floor. This complies with the National Fuel Gas Code,
ANSI Z223.1 NFPA 54 -latest edition for U. S. installa-
tions, or
Natural Gas and Propane Installation Code,
CAN/CSA
B149.1 and B149.2 for Canadian installations.
• Locate or protect the boiler so it cannot be damaged by
a moving vehicle.
• Ensure that the installation complies with all applicable
codes.
• Prevent boiler water and condensate from freezing.
Provide air openings to room
Evergreen
®
boiler alone in boiler room
(Direct Vent)
1. No air ventilation openings into boiler room are needed if
clearances around
Evergreen
®
boiler are at least equal to the
SERVICE clearances shown in Figure 1, page 7.
2. For spaces that DO NOT supply the minimum service clear-
ances, provide two openings as shown in Figure 1, page 7.
Each opening must provide 1 square inch free area per 1,000
Btuh of boiler input.
Evergreen
®
boiler in same space with other gas
or oil-fired appliances
1. Follow the sizing requirements shown in Figure 26, page 24.
The space must be provided with combustion/
ventilation air openings correctly sized for all
appliances located in the same space as the
Evergreen
®
boiler.
Reinstall boiler jacket front door after servic-
ing. The boiler front door must be securely
fastened to the boiler to prevent boiler from
drawing air from inside the boiler room. This
is particularly important if the boiler is located
in the same room as other appliances.
Failure to comply with the above warnings
could result in severe personal injury, death
or substantial property damage.
Vent and air piping
1. The
Evergreen
®
boiler requires a special vent system, designed
for pressurized venting.
Evergreen
®
boilers are rated ANSI
Z21.13 Category IV (pressurized vent, likely to condense in
the vent). See instructions beginning on page 19.
2. You must also install air piping from outside to the boiler
air intake adapter. The resultant installation is categorized as
direct vent (sealed combustion). Note prevention of combus-
tion air contamination on page 19 when considering vent/
air termination.
3. Vent and air must terminate near one another unless oth-
erwise specified in this manual. Vent and air piping may be
routed vertically through the roof or out a side wall, following
the options give in this manual. You may use any of the vent/
air piping methods covered in this manual. Do not attempt
to install the boiler using any other means.
4. Be sure to locate the boiler such that the vent and air piping
can be routed through the building and properly terminated.
The vent/air piping lengths, routing and termination method
must all comply with the methods and limits in instructions
beginning on page 19.
Содержание Evergreen EVG 220
Страница 134: ...Part number 550 100 131 0120 134 gas fired water boiler 220 299 300 399 Boiler Manual Notes...
Страница 135: ...Part number 550 100 131 0120 135 gas fired water boiler 220 299 300 399 Boiler Manual Notes...
Страница 136: ...136 gas fired water boiler 220 299 300 399 Boiler Manual...