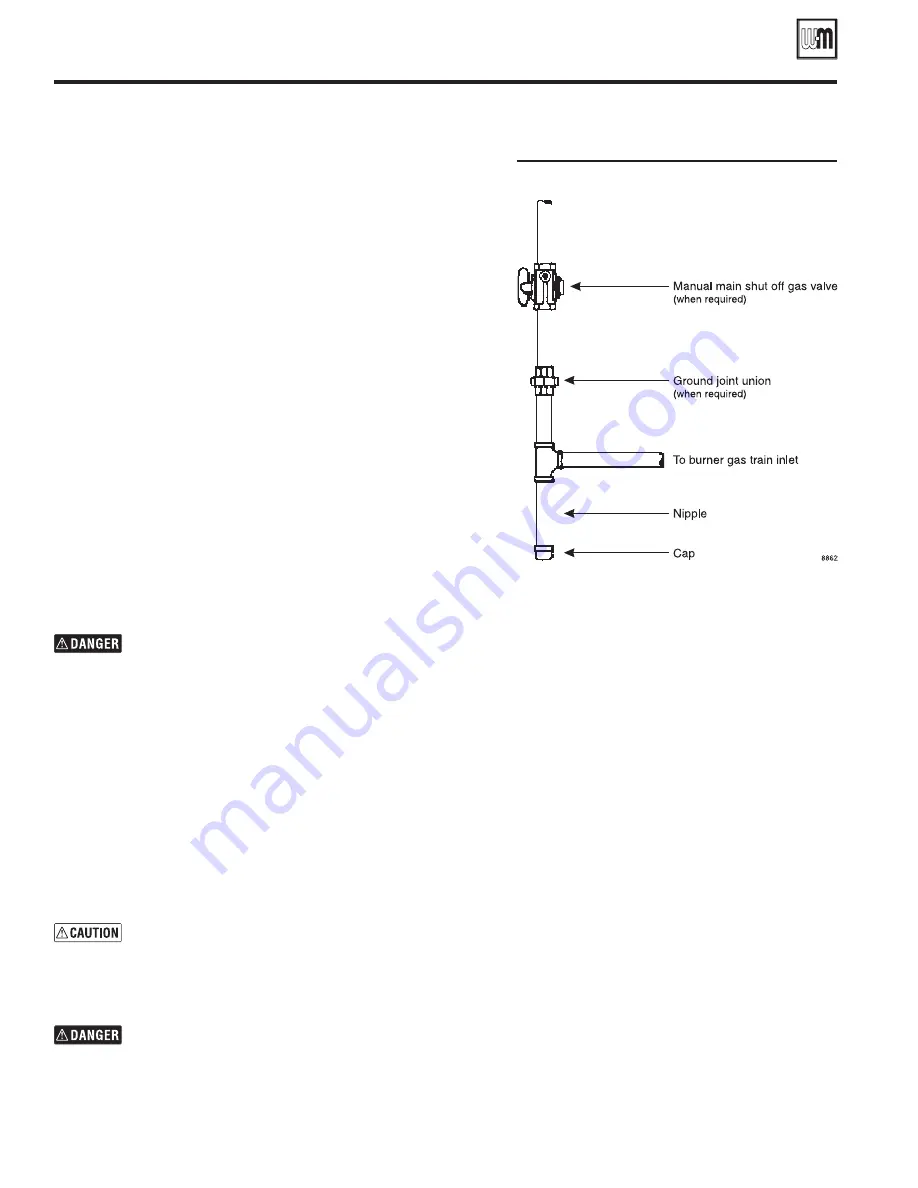
Weil-McLain 88 Water and steam boilers — Series 2 —
for Gas, Light Oil, & Gas/Light Oil-Fired Burners
32
Part No. 550-100-068/1009
Install fuel piping
'ASPIPING
In sizing the gas piping, the following factors should be consid-
1.
ered:
Diameter and length of the gas supply piping.
a.
Number of fittings.
b.
Maximum gas consumption (including any possible future
c.
expansion).
Allowable loss in gas pressure from the gas meter outlet to
d.
the boiler.
Minimum inlet natural gas pressure required at manual main shut-
2.
off valve — see the burner manual and material list.
Follow good piping practices.
3.
Pipe joint compound (pipe dope) must be resistant to the corrosive
4.
action of liquefied petroleum gases and applied sparingly only to
the male threads of pipe joints.
A ground joint union must be installed in the piping to provide
5.
for servicing. The supply piping must include a manual shut-off
valve and sediment trap. See Figure 48.
Piping must be supported by hangers, not by the burner or its
6.
accessories.
Purge all air from the supply piping.
7.
All gas piping must be tested for leaks after installation. Use soap
8.
suds mixture only.
Fuel oil piping
To prevent oil flow in case of oil line breakage:
s 5SEANTISYPHONDEVICEWHENANYPARTOFTHEOILTANK
is above burner level.
s 5SE CHECK VALVE IN SUCTION LINE ON BURNER SIDE OF
manual shut-off valve nearest tank when top of fuel
oil tank is below burner level.
Failure to comply could result in fuel leakage or fire, caus-
ing potential severe personal injury, death or substantial
property damage.
A two-pipe fuel oil piping system is required for all installations.
1.
Supply and return lines must enter tank from top, extending to
2.
within 4 to 6 inches from bottom of tank.
Use oil filter sized for fuel pump suction gear capacity.
3.
Install oil filter.
4.
Do not install filter outside or close to an outside wall.
Use continuous copper tubing to reduce possible piping leaks and
5.
to ensure reliable seal when oil piping is buried.
Use flare fittings, not compression fittings.
6.
&IREHAZARD
— DO NOT USE soldered fittings. No safe
repair can be made.
Follow good piping practices.
7.
Pipe joint compound (pipe dope) must be resistant
8.
to corrosive action of fuel oil. Apply sparingly only
to male threads of pipe joints.
Supply and return piping should be sized to design
9.
conditions, but not less than ½" O.D. continuous
copper tubing.
Auxiliary fuel oil pump is recommended when
10.
suction line lift exceeds 12 feet.
Install swing joints so they will tighten as buried
11.
tank settles to prevent fuel line breakage.
Where iron pipe is required by local codes, make
12.
swing joints with nipples and elbows several inches
long on both suction and return line. Locate close
to tank.
Install manual shut-off valve in suction line piping
13.
near burner and where piping enters building from
outside tank.
Pitch suction line piping toward fuel tank.
14.
Provide tee and plug at highest point in suction
15.
line to release air from suction line and aid in
priming.
Gas supply piping
&IGURE