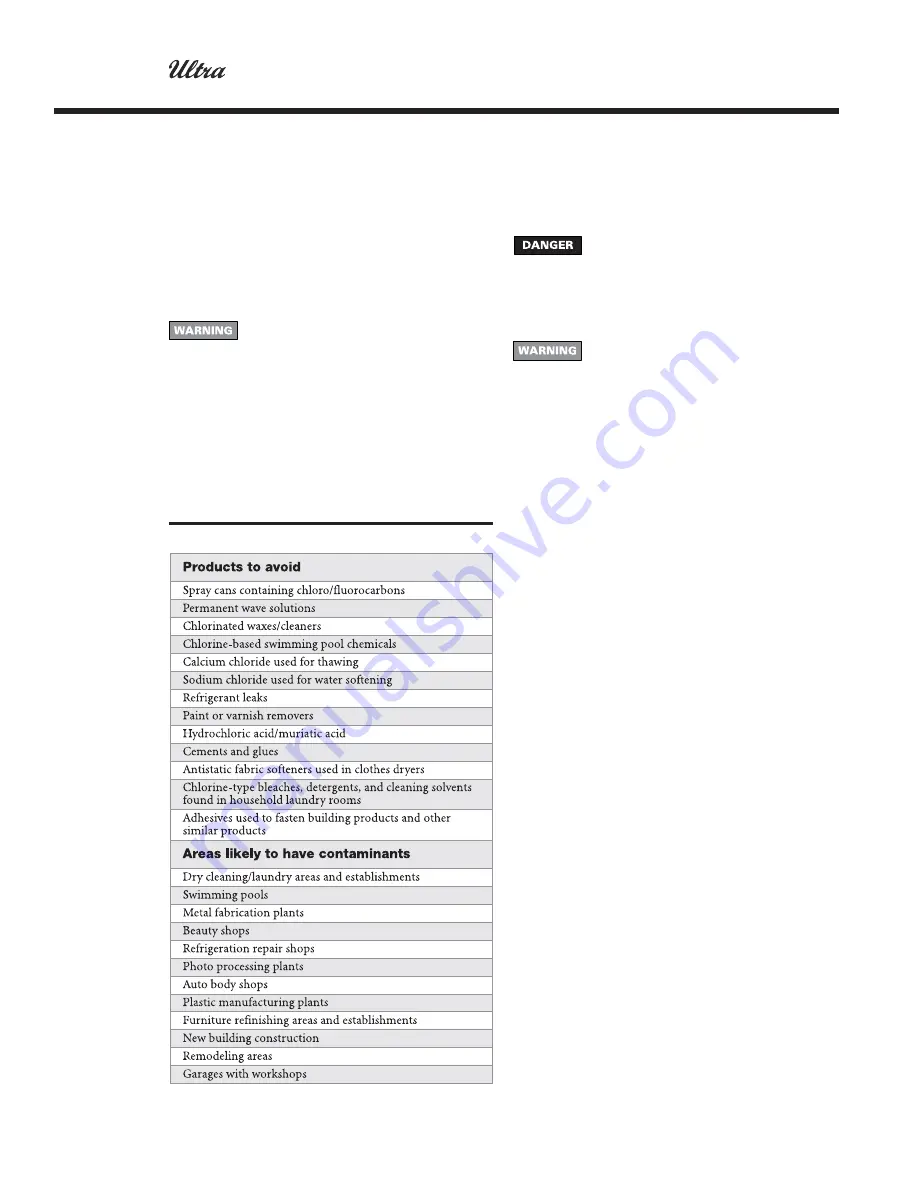
Part number 550-100-026/0404
GAS
-
FIRED
WATER
BOILER
SERIES
2 — Boiler Manual
8
Table 1
Corrosive contaminants and sources
Prevent combustion air
contamination
Install air inlet piping for the Ultra boiler as described in
the Ultra Boiler Vent Supplement. Do not terminate vent/
air in locations that can allow contamination of
combustion air. Refer to Table 1 for products and areas
which may cause contaminated combustion air.
You must pipe combustion air to the boiler
air intake. Ensure that the combustion air
will not contain any of the contaminants
below. Contaminated combustion air will
damage the boiler, resulting in possible
severe personal injury, death or substantial
property damage. Do not pipe combustion
air near a swimming pool, for example.
Also avoid areas subject to exhaust fumes
from laundry facilities. These areas will
always contain contaminants.
Prepare boiler location
(continued)
1
When removing a boiler from
existing common vent system:
Do not install the Ultra boiler into a
common vent with any other appliance.
This will cause flue gas spillage or appliance
malfunction, resulting in possible severe
personal injury, death or substantial
property damage.
Failure to follow all instructions can result
in flue gas spillage and carbon monoxide
emissions, causing severe personal injury
or death.
At the time of removal of an existing boiler, the following
steps shall be followed with each appliance remaining
connected to the common venting system placed in
operation, while the other appliances remaining connected
to the common venting system are not in operation.
a. Seal any unused openings in the common venting
system.
b. Visually inspect the venting system for proper size
and horizontal pitch and determine there is no
blockage or restriction, leakage, corrosion or other
deficiencies which could cause an unsafe condition.
c. Test vent system — Insofar as is practical, close all
building doors and windows and all doors between
the space in which the appliances remaining
connected to the common venting system are located
and other spaces of the building. Turn on clothes
dryers and any appliance not connected to the
common venting system. Turn on any exhaust fans,
such as range hoods and bathroom exhausts, so they
will operate at maximum speed. Do not operate a
summer exhaust fan. Close fireplace dampers.
d. Place in operation the appliance being inspected.
Follow the lighting instructions. Adjust thermostat
so appliance will operate continuously.
e. Test for spillage at draft hood relief opening after 5
minutes of main burner operation. Use the flame of
a match or candle, or smoke from a cigarette, cigar,
or pipe.
f.
After it has been determined that each appliance
remaining connected to the common venting system
properly vents when tested as outlined herein, return
doors, windows, exhaust fans, fireplace dampers, and
any other gas-burning appliance to their previous
conditions of use.
Any improper operation of common venting system
should be corrected so the installation conforms with
the National Fuel Gas Code, ANSI Z223.1 — latest edition.
Correct by resizing to approach the minimum size as
determined using the appropriate tables in Part 11 of
that code. Canadian installations must comply with
B149.1 or B149.2 Installation Code.