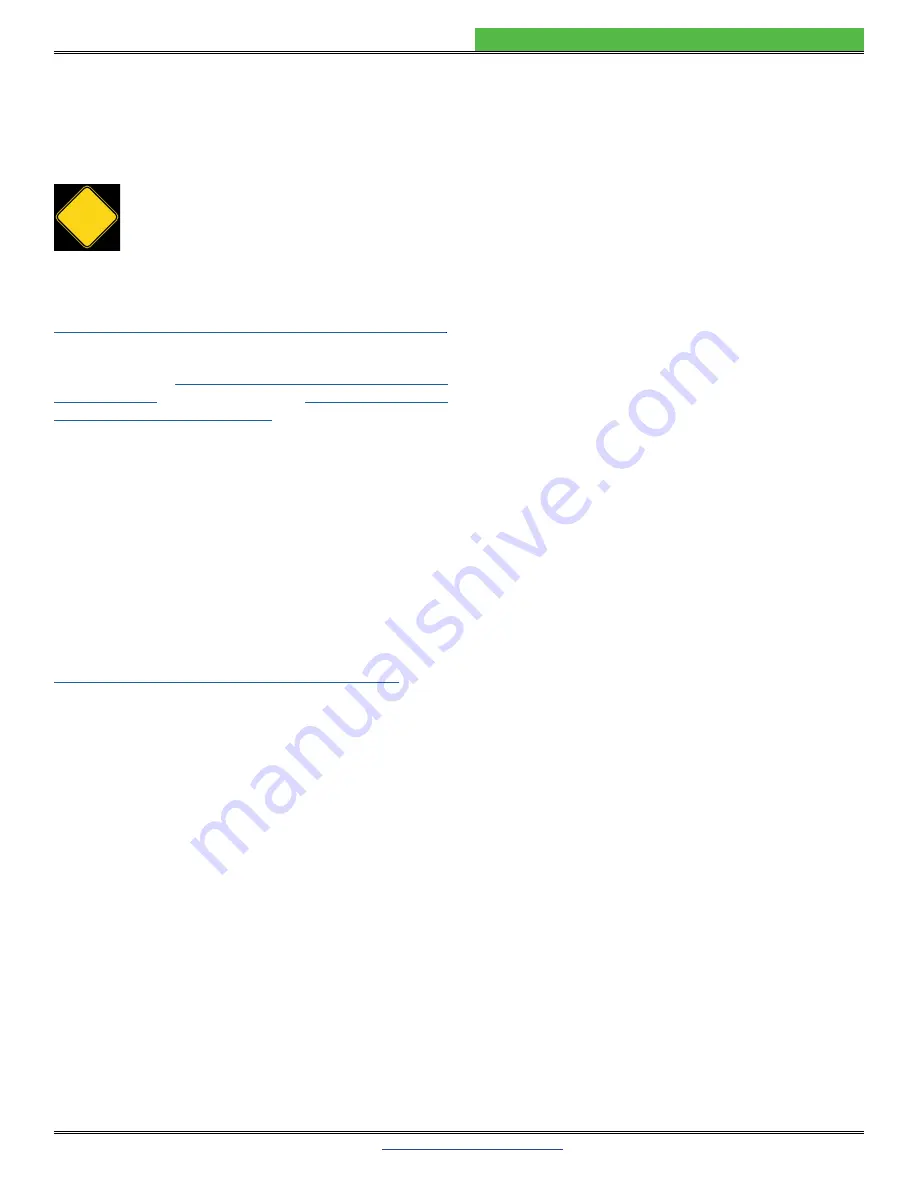
© 2023
7
WHY5640 TEMPERATURE CONTROLLER
SAFETY INFORMATION
SAFE OPERATING AREA — DO NOT EXCEED
INTERNAL POWER DISSIPATION LIMITS
!
To ensure safe operation of the WHY5640
Thermoelectric Controller, it is imperative
that you determine that the unit will be
operating within the internal heat dissipation
Safe Operating Area (SOA).
Visit the Wavelength Electronics website for the most
accurate, up-to-date, and easy to use SOA calculator:
www.teamwavelength.com/support/design-tools/soa-tc-calculator/
For more information on Safe Operating Area, see our
Application Note
AN-LDTC01: The Principle of the Safe
and our SOA video:
Operating Area (SOA) Calculator
PREVENT DAMAGE FROM ELECTROSTATIC
DISCHARGE
Before proceeding, it is critical that you take precautions
to prevent electrostatic discharge (ESD) damage to the
controller and your load. ESD damage can result from
improper handling of sensitive electronics, and is easily
preventable with simple precautions.
For more information regarding ESD, see Application Note
AN-LDTC06: Basics: Electrostatic Discharge (ESD).
We recommend that you always observe ESD precautions
when handling the WHY5640 controller.
THERMAL MANAGEMENT KITS
The WHY5640 has many thermal management accessories.
They include thermal washers, heatsinks, and fans. These
products are available either as individual accessories,
or bundled together in kits. The use of these thermal
management accessories helps ensure that the WHY5640
will remain in the SOA during operation.
THEORY OF OPERATION
The WHY5640 is a analog Proportional, Integral (PI) control
loop for use in thermoelectric or resistive heater temperature
control applications. The WHY5640 maintains precision
temperature regulation using an active resistor bridge circuit
that operates directly with thermistors or RTD temperature
sensors.
The fundamental operating principle is that the controller
adjusts the TEC drive current in order to change the
temperature of the sensor that is connected to the thermal
load. The goal is to make the resistance of the sensor match
the setpoint resistance, and then keep them equal in spite
of changes to ambient conditions and variations in thermal
load.
The controller measures the load temperature by the
resistance of the sensor as well as the difference between
resistances of the sensor and the setpoint resistor.
While the output is enabled the controller continuously
compares the setpoint resistance and the actual sensor
resistance. If there is a difference between the two values
the controller adjusts the output current—thereby driving the
TEC or heater to change temperature—until the difference
is zero.
Once the actual sensor resistance equals the setpoint
resistance, the controller makes minor adjustments to the
output current in order to keep the difference at zero. If the
ambient temperature changes, for example, the controller
will adjust the drive current accordingly.
The controller includes features that help protect the load
from damage. These features are explained in detail in
Operating Instructions — Standalone on page 8
.
• Current limit:
Independent heating and cooling current
limits avoid over-driving and damaging the TEC or
heater.
• External or Onboard temperature setpoint control:
for
prototyping and benchtop applications the temperature
setpoint can be adjusted with the onboard trimpot on the
evaluation board. When the controller is integrated into
an automated control system, the temperature setpoint
can be adjusted by an external voltage signal.
• Local Enable on WHY5690 Evaluation Board:
the
controller can be configured so that the output is always
on whenever power is applied to the unit.
• Control loop:
the controller employs a smart
Proportional-Integrating control loop to adjust the drive
current.