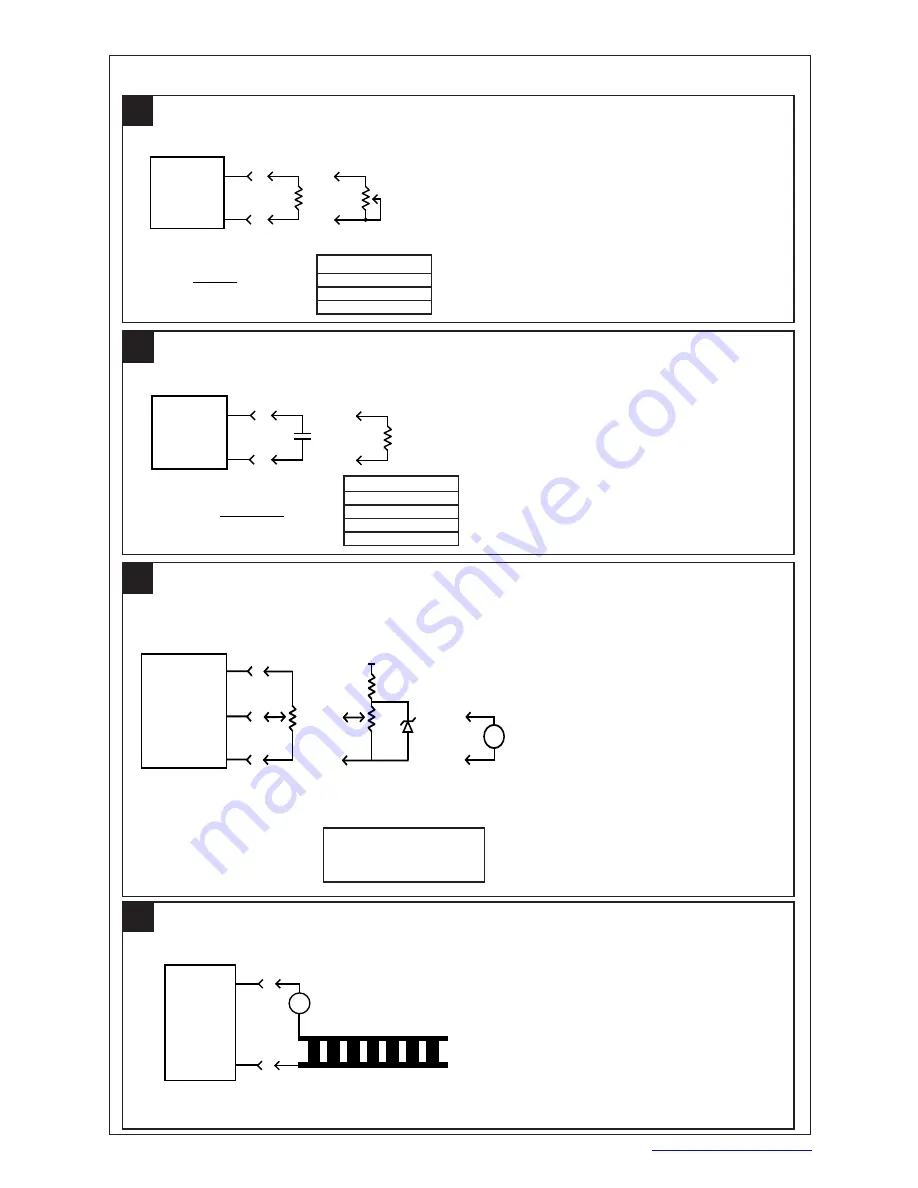
HTC4000 TEMPERA
TURE CONTROLLER
www.teamwavelength.com
© 2012
HTC4000-62400-B
PAGE 8
The controller adjusts the temperature
of the load until the voltage across the
temperature sensor equals the Setpoint
Input voltage (pins 8 & 15). To adjust the
temperature setpoint, first determine the
voltage across the sensor at the target
temperature; apply that same voltage
across pins 8 and 15 of the controller.
The diagrams to the left show three
possible configurations for setpoint
voltage input.
C
INT
=
1 M
Ω
T
INT
17
18
Fixed,
Metal Film
OR
R +
R -
Adjustable
(500 k
Ω
typical)
PROP
PROP
Use a trimpot no more than twice the
calculated value of R
PROP
for best resolution.
R
PROP
sets the gain of the system from 1
to 100. A higher proportional gain can
help minimize the time to settling but may
destabilize loads with long intrinsic lag times.
Too low a gain may result in oscillations
about setpoint. For most applications, a gain
of 33 works (R
PROP
= 10 kΩ). Change the
proportional gain while the output is OFF.
Proportional Gain - Pins 17 & 18
C
int
sets the integral time constant of the
system from 0 to 10 seconds. Use a capacitor
with Dissipation Factor less than 1% for best
performance. These typically include metallized
film polyester, polypropylene & some ceramic
capacitors. Capacitors with Dissipation Factors
>1% (typically electrolytic, tantalum, and ceramic)
will cause drift in the Integrator circuit. To disable
the integrator, use a 1 M
Ω
resistor across pins
19 & 20.
R
PROP
=
500 k
Ω
GAIN - 5 k
Ω
19
20
C +
C -
INT
INT
C
INT
Fixed,
Metal Film
OR
1 M
Ω
C
INT
1 M
Ω
1
µ
F
5
µ
F
10
µ
F
T
INT
0 (OFF)
1 second
5 seconds
10 seconds
4
8
3.675 V Ref Out
Setpoint Input
(V+ Maximum)
Common 5
R
1
R
1
= 10 k to
100 k
Ω
Use Ref
Voltage
Provided
R
1
Use V+
for higher
sense voltage
1 k
Ω
V+
OR
Apply
Remote
Voltage
+
-
V
REF
Select V
REF
to cover
your temperature range
OR
11
12
TEC +
TEC -
Optional Ammeter
to monitor
TE Current
A
Connect the TE module and an ammeter
if you want to monitor TE current. Current
flows from positive to negative when the
HTC is cooling with an NTC temperature
sensor. When using an LM335, AD590,
RTD, or other PTC sensor, reverse the
polarity of the leads (i.e. connect the
positive lead of the TE module to TEC-
and the negative lead of the TE module
to TEC+).
Integrator Time Constant - Pins 19 & 20
Temperature Setpoint - Pins 8 & 5 (Pin 4 optional)
TE Module & Output Current Measurement - Pins 11 & 12
Monitor setpoint with a DVM
at pins 7 & 5, or actual sensor
voltage across pins 6 & 5.
6
5
7
8
R
PROP
495 k
Ω
5 k
Ω
0
Ω
GAIN
1
50
100
OPERATION WITH THERMOELECTRICS, continued
Example:
Desired Temperature:
25
°
C
Sensor:
10 k
Ω
thermistor
Resistance at 25
°
C:
10 k
Ω
Bias Current:
100
µ
A
V
SET
= 10 k
Ω
* 100
µ
A = 1 V